Brushless Motor
Because the rotor is free of other objects (no brush), it is designed for high power, and noise-less by principle. It is suitable for long-life use.
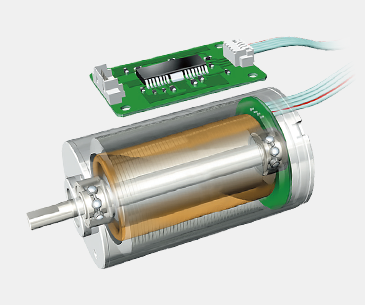
Output | Because of no-contact design (no brush/commutator like cored/coreless motor), large current can be input and heat in the coil dissipates quickly |
---|---|
Life | Long life time because of no-contact design |
Control | Linear characteristics |
Cogging | No magnetic cogging |
In our brushless motor, we removed the mechanical contacts such as brushes and commutators used in conventional brushed motors, and applied an electric signal to take their place. The brushless motor requires an electric circuit board because there is no commutator. This motor (circuit board) has two types, one with a magnetic sensor, and the other with no sensor. The one with the magnetic sensor detects its position via the sensor, and the other detects the rotor magnet position via back-EMF. Brushless motor's features are as follows:
Features
- Stator coil is located outside in inner rotor type brushless motor. Therefore, it is good in heat dissipation.
Because there are no contacts (brush/commutator), large current can be input to answer to high power needs. - No mechanical noise and no electric noise for switching current(no brush and no commutator)
- Long life and high reliability (due to no-contact design)
In Orbray's brushless motor, stator is a slot-less core with cup-shaped coil, and rotor is the magnet inside. Therefore, magnetic force is even regardless of coil/magnet position, and motor rotation is free of cogging.
Issues & Challenges in Brushless Motor
As brushless motors have no mechanical contacts for polarity switching, they have high power and long lifespan. However, due to the rotating magnet core, the inertia is much larger than that of coreless brushed motor and the response time slower.
Orbray presents brushless motors that address these issues equally.
Brushless Motor Standard Model
Pro- ducts |
Geared Motor | Dia. [mm] |
Len- gth [mm] |
Nominal Voltage [V] |
Nominal Values | No load | Stall | Mecha- nical time constant [ms] |
Max effici- ency [%] |
Option | CAD download |
||||||||
---|---|---|---|---|---|---|---|---|---|---|---|---|---|---|---|---|---|---|---|
Torque [mNm] |
Speed [rpm] |
Cur- rent [mA] |
Out- put [W] |
Speed [rpm] |
Cur- rent [mA] |
Tor- que [mNm] |
Cur- rent [mA] |
Con nec tion |
Bearing | Encoder | |||||||||
slee- ve |
BB | with | no | ||||||||||||||||
BMN04-0829 | Planetary | 4 | 8 | 3.0 | 0.01 | 24,200 | 53 | 0.04 | 37,000 | 28 | 0.04 | 100 | 9.2 | 22 | A (sensor- less) |
○ | × | 2D 3D |
2D 3D |
BMN07-1207 | Planetary | 7 | 13 | 3.0 | 0.06 | 17,100 | 182 | 0.2 | 21,300 | 120 | 0.30 | 430 | 7.3 | 22 | B(A※) | ○ | × | 2D 3D |
2D 3D |
BMN07-1218 | Planetary | 7 | 13 | 5.0 | 0.06 | 17,900 | 117 | 0.2 | 22,300 | 78 | 0.30 | 280 | 7.7 | 22 | B(A※) | ○ | × | 2D 3D |
2D 3D |
BMS10-1003 | Spur Planetary |
10 | 10 | 4.0 | 0.17 | 30,400 | 384 | 0.9 | 37,900 | 185 | 0.86 | 1190 | 10.9 | 37 | C | ○ | × | 2D 3D |
2D 3D |
BMS10-1008 | Spur Planetary |
10 | 10 | 6.0 | 0.15 | 27,100 | 208 | 0.8 | 33,800 | 103 | 0.75 | 630 | 11.1 | 36 | C | ○ | × | 2D 3D |
2D 3D |
BMS10-1803 | Spur Planetary |
10 | 18 | 7.4 | 0.63 | 27,000 | 351 | 4.5 | 31,300 | 63 | 4.54 | 2140 | 3.9 | 69 | C | ○ | × | 2D 3D |
2D 3D |
BMS10-1806 | Spur Planetary |
10 | 18 | 12.0 | 0.68 | 30,800 | 268 | 4.9 | 35,800 | 49 | 4.86 | 1621 | 4.1 | 68 | C | ○ | × | 2D 3D |
2D 3D |
BMS12-1503 | Spur Planetary |
12 | 15 | 7.4 | 1.05 | 21,461 | 523 | 3.9 | 26,200 | 113 | 5.73 | 2350 | 4.3 | 61 | D | ○ | × | 2D 3D |
2D 3D |
BMS12-1506 | Spur Planetary |
12 | 15 | 12.0 | 1.10 | 25,683 | 394 | 5.2 | 31,000 | 82 | 6.33 | 1877 | 4.6 | 63 | D | ○ | × | 2D 3D |
2D 3D |
BMS12-2102 | Spur Planetary |
12 | 21 | 7.4 | 1.83 | 19,200 | 706 | 6.9 | 22,800 | 100 | 11.60 | 3940 | 2.7 | 71 | D | ○ | × | 2D 3D |
2D 3D |
BMS12-2104 | Spur Planetary |
12 | 21 | 12.0 | 1.60 | 21,100 | 418 | 7.7 | 24,300 | 70 | 12.09 | 2700 | 2.8 | 70 | D | ○ | × | 2D 3D |
2D 3D |
BMS16-2001 | Spur Planetary |
16 | 20 | 7.4 | 3.20 | 18,800 | 1305 | 9.4 | 23,800 | 188 | 15.06 | 5450 | 5.7 | 66 | D | ○ | △ | 2D 3D |
2D 3D |
BMS16-2004 | Spur Planetary |
16 | 20 | 12.0 | 2.42 | 19,700 | 620 | 9.7 | 23,200 | 113 | 15.97 | 3460 | 5.3 | 67 | D | ○ | △ | 2D 3D |
2D 3D |
BMS16-2013 | Spur Planetary |
16 | 20 | 24.0 | 2.45 | 21,100 | 334 | 10.6 | 24,800 | 60 | 16.30 | 1880 | 5.5 | 67 | D | ○ | △ | 2D 3D |
2D 3D |
BMS16-3001 | Spur Planetary |
16 | 30 | 7.4 | 3.25 | 12,600 | 807 | 9.5 | 14,500 | 123 | 25.10 | 5390 | 3.6 | 72 | D | ○ | △ | 2D 3D |
2D 3D |
BMS16-3002 | Spur Planetary |
16 | 30 | 12.0 | 3.90 | 14,800 | 660 | 15.4 | 16,600 | 86 | 35.33 | 5290 | 2.9 | 76 | D | ○ | △ | 2D 3D |
2D 3D |
BMS16-3010 | Spur Planetary |
16 | 30 | 24.0 | 3.86 | 14,000 | 311 | 14.0 | 15,800 | 41 | 33.84 | 2410 | 2.9 | 76 | D | ○ | △ | 2D 3D |
2D 3D |
BMS17-1821 | Not applicable |
17 | 18 | 24.0 | 2.36 | 16,000 | 291 | 6.2 | 20,000 | 72 | 11.80 | 1170 | 16.3 | 57 | D | × | ○ | 2D 3D |
2D 3D |
BMS22-2113 | Not applicable |
22 | 22 | 24 | 5.50 | 10,000 | 381 | 10.2 | 12,000 | 80 | 32.30 | 1850 | 7.9 | 62 | D | × | ○ | 2D 3D |
2D 3D |
Brushless Motor 4pole High Torque Model
Pro- ducts |
Geared Motor | Dia. [mm] |
Len- gth [mm] |
Nominal Voltage [V] |
Nominal Values | No load | Stall | Mecha- nical time constant [ms] |
Max effici- ency [%] |
Option | CAD download |
||||||||
---|---|---|---|---|---|---|---|---|---|---|---|---|---|---|---|---|---|---|---|
Torque [mNm] |
Speed [rpm] |
Cur- rent [mA] |
Out- put [W] |
Speed [rpm] |
Cur- rent [mA] |
Tor- que [mNm] |
Cur- rent [mA] |
Con nec tion |
Bearing | Encorder | |||||||||
slee- ve |
BB | with | no | ||||||||||||||||
B4S12-2108 with Encoder | Spur Planetary |
12 | 21 | 12.0 | 11.1 | 13111 | 277 | 4.5 | 15320 | 55 | 11.1 | 1592 | 3.5 | 66 | D | ○ | ○ | 2D 3D |
2D 3D |
B4S12-2109 with Encoder | Spur Planetary |
12 | 21 | 15.0 | 11.6 | 16646 | 279 | 5.9 | 19300 | 56 | 11.6 | 1678 | 4.2 | 67 | D | ○ | ○ | 2D 3D |
2D 3D |
B4S22-3210 with Encoder | Planetary | 22 | 32 | 24.0 | 10 | 6073 | 365 | 13.9 | 7000 | 53 | 75.5 | 2412 | 3.9 | 73 | E | × | ○ | 2D 3D |
2D 3D |
Meaning
- ○ = Available as standard
- △ = Available as option
- × = Not available
- A∼G = Pin assignment pattern (see table)
Brushless Motor Pin Assignment Pattern
Pattern | #1 | #2 | #3 | #4 | #5 | #6 | #7 | #8 | Applicable motor | |
---|---|---|---|---|---|---|---|---|---|---|
A | FPC | coil U | coil V | COM | coil W | - | - | - | - | BMN04, BMS07 (sensorless時) |
B | sensor V | sensor U | Gnd | Vdd | sensor W | coil V | coil W | coil U | BMS07 | |
C | leadwire | coil W | coil U | sensor U | sensor V | sensor W | coil V | Gnd | Vdd | BMS10 series |
D | coil U | coil V | coil W | Vdd | Gnd | sensor U | sensor V | sensor W | BMS12/ BMS16 series/ B4S12 |
|
E | coil W | coil V | coil U | Gnd | Vcc | sensor W | sensor V | sensor U | B4S22-3212 | |
F | Terminals | coil W | sensor W | COM | coil W | - | - | - | - | BRS/BRT17-15 BRS/BRT17-18 |
G | H1 sensor U | H2 Vcc | H3 Gnd | H4 sensor W | H5 sensor W | L1 coil U | L2 coil V | L3 coil W | BRS/BRT12-15 |
Outer Rotor Flat Brushless Motor
Products | Dia. [mm] | Thickness [mm] | Nominal Voltage [V] | No-load | Stall | ||
---|---|---|---|---|---|---|---|
Speed [rpm] | Current [A] | Toreque [mNm] | Current [A] | ||||
SOBL23-1207 | 23 | 12 | 12 | 5730 | 0.127 | 26.8 | 1.38 |
Driver
Products | Voltage supply:VCC | Applicable motor types |
---|---|---|
SSD06-R5A | 1.8~ 5.5 | Sensorless brushless motors; BMN04-08XX, BMN07-12XX |
SHSD24-01A | 7.5~ 26.4 | All Orbray brushless motors |
Contact
*Click here for detailed inquiries.
*If you cannot find the contact form, please click here.