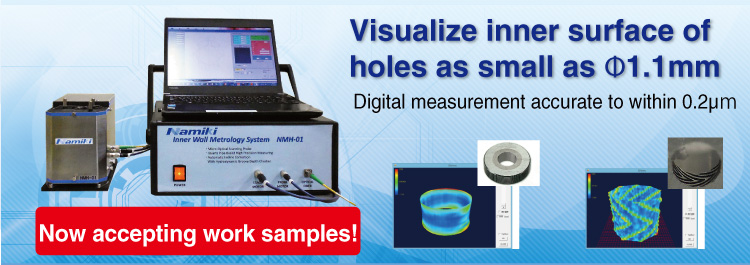
The importance of inner peripheral surface evaluation has been increasing for precision
pore-machined parts such as fuel injection nozzles in aerospace instruments, hollow parts in medical
devices, precision nozzles in analyzers, and hydrodynamic bearings.
Existing measuring instruments can evaluate inner diameter, roundness, surface roughness, and shape of
machined parts with relatively large inner diameters. However, these instruments are not able to gauge the
pore-machined parts unless the bodies of the parts are cut in half.
Orbray has developed the “NMH-02”an OCT inner peripheral surface measuring instrument that enables the
visualization of the inner peripheral surfaces of pores using optical interference of near infrared
light.
This unique invention was possible thanks to our micro motor technology and optical communication
technology. It combines our world's smallest φ0.9mm motor with our patented optical imaging probe, and
is equipped with our patented tilt correcting algorithm. It has the following new capabilities: (1)
Measurement of inner diameter as small as φ1.1mm; (2) simultaneous measurement of inner diameter,
roundness, and shape; (3) repeatability to an accuracy of σ=0.2μm; (4) ready-to-use convenience.
Our instrument is not only able to observe and measure the inner peripheral surfaces of pore-machined parts,
but can also simultaneously evaluate inner diameter, roundness, surface roughness, and shape, which used to
require using separate instruments for each. These features significantly reduce the measurement time from
about 30min to 30sec, and contribute to the improvement of measurement throughput for customers.
Features
- Smallest inner diameter measurable: 1.1mm
- Repeatability with accuracy of σ=0.2μm
- Setting free:work's inclination automatically adjusted by original computing.
- Measuring time:30min (conventional) reduced to 30sec
(simultaneous measurement of inner diameter/circularity/shape)
Comparison to conventional method
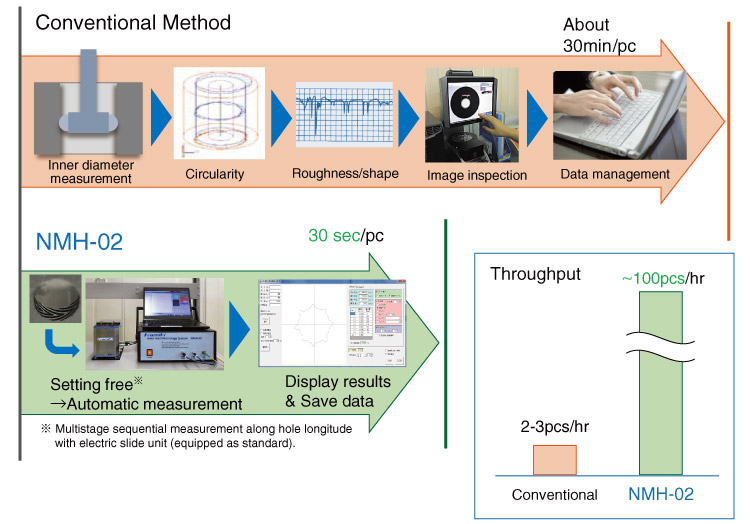
- Measurable Minimum Diameter φ1.1mm over
world's smallest φ0.9mm motor installed. - Repeated Measurement Accuracy: 0.2μm
Minimizing optical vibration and fluctuation by translucent standard pipe. - Setting free measurement
Auto- adjusting a work's inclined and eccentric state by arithmetic processing.
Measurement example
Link gauge
Gauge diameter:
φ3.900
3D picture
Measured result:
φ3.89977
(Center value)
2D inner diameter dataInner diameter data
at Z axis direction
Hydrodynamic bearing
Inner diameter:
φ1.60
3D picture
Measured
result:
φ1.60122
2D pictureAuto-detection of
dynamic pressure groove
Auto scratch detection
Inner diameter:
φ3.900
Dent detection
Vertical scratch detection