Capable of grinding holes up to 15µ fine in a wide variety of materials
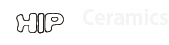
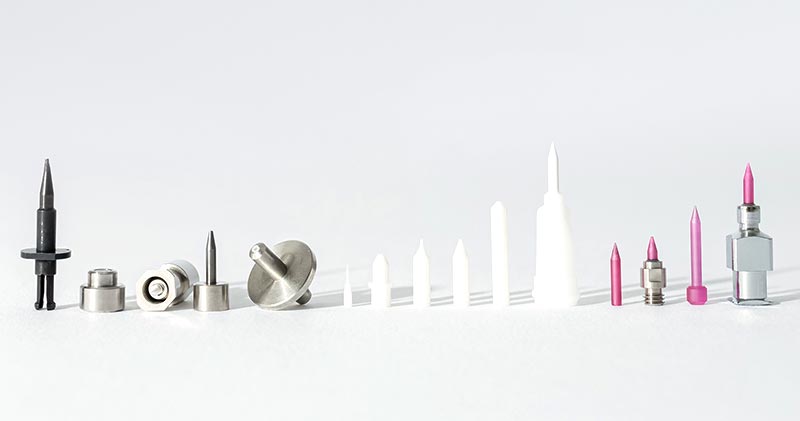
Custom dispensing nozzles made to your specifications
Fine hole grinding from 15 microns is possible.
The grinding process is controlled at the 1-micron level, with minimal variation.
Orbray offers products with size control at the 1-micron level using laser, drilling, and other micro-hole processing technologies.
Dispensing nozzles and picking nozzles can be made according to request
<Pharmaceutical dispenser nozzles>
Pharmaceuticals are often expensive, so unnecessary dispensing can significantly increase costs.
Applicable to a wide variety of materials
We can make dispensing nozzles and picking nozzles from diamond, tempered alumina, zirconia, ruby, sapphire, tungsten carbide, stainless steel, vespel, and other materials best suited to your equipment and solvent. Ruby nozzles, in particular, are our original product.
Ceramics are turned into high-density materials through HIP (Hot Isostatic Pressing).
The HIP treatment densifies (shrinks) the material while maintaining its shape.
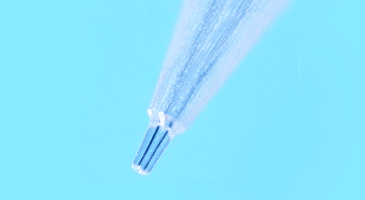
Alumina 99.99%
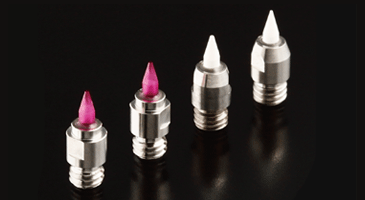
Ruby nozzle
<Picking nozzles for transporting fine chips>
We can manufacture picking nozzle (Adsorption nozzles) suitable for miniaturized chips, such as the 0201 chips (with outer dimensions of 0.2 x 0.1 mm) and 0402 chips (with outer dimensions of 0.4 x 0.2 mm), which are commonly used for multilayer ceramic capacitors, among other applications.
Small Batch Production
We accept orders from small lot sample production. We have many examples of joint development for special applications. One example is the realization of an alumina permeable nozzle that allows the user to check the internal flow path.
Smooth bore surface with a roughness of less than 0.010 microns.
Our unique high-precision mirror polishing process has achieved an inner surface smoothness of less than Ra0.010 microns.
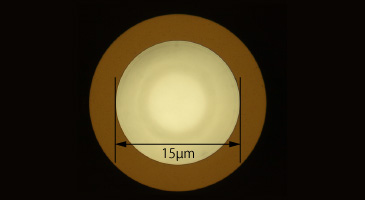
Fine Hole Processing(Nozzle tip)
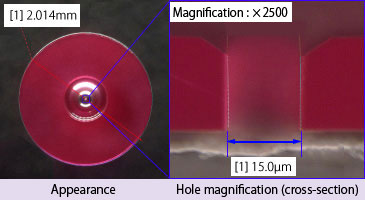
Orifice Type
>> Dispensing nozzles and needle |
>> Winding nozzle | >> Orifice nozzles | >> Pharmaceutical and reagent dispensing nozzles |
>> Picking nozzles | >> Picking collets | Injection nozzle | High precision needle | Specialty nozzle and needle |
Contact
Product type
HIP processed for high density, resulting in less chipping
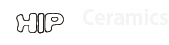
- High density by HIP process Less chipping
- Due to injection molding, there is no variation in the internal shape.
- Customized shapes can be produced to meet customer needs.
- Excellent cost performance.
- High quality and long life.
Monocrystalline ruby nozzles and needles
- Low resistance due to its single-crystal structure
- Mirror-polished inner surface allows for smooth flow of coating liquid and reduces clogging
- Holes as small as φ15 µm, up to φ30 µm, are available
- High quality and long service life
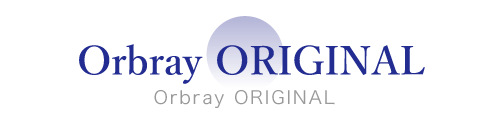
Orifice type nozzles
- Suitable for inkjet printers, semiconductor manufacturing, medical equipment, etc.
- The single-crystal ruby sapphire allows for good wettability and stable liquid flow.
- Compared with metal nozzles, it enables straight dispensing without any streaks or burrs.
All dispensing nozzles and picking nozzles are compatible with double threaded screw and luer lock.
Typical example of dispensing nozzles (precision nozzles)
We will manufacture according to the dimensions specified in the alphabetical part of the drawing.
Dispensing Nozzles / Needles
Applications: Dispensing liquids, adhesives, chemicals, greases, foods (chocolate, cream, etc.)
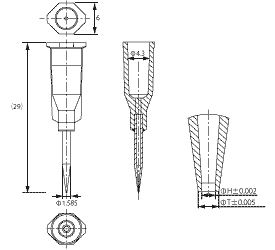
Ruby(Single Cristal) | Ceramic (Zirconia) |
Hard Metal | |||
---|---|---|---|---|---|
tip(I.D) (H) |
tip(O.D) (T) |
tip(O.D) (H) |
tip(O.D) (T) |
tip(I.D) (H) |
tip(O.D) (T) |
φ0.025~0.3 | φ0.055~0.5 | φ0.015~φ0.3 | φ0.045~φ0.45 | φ0.1~φ0.7 | φ0.13~φ0.8 |
Nozzle length: (further discussion required) |
Dimension:mm
The thickness of one side of the tip | Ruby | Ceramic | Hard Metal |
---|---|---|---|
Minimum | 0.015 | 0.015 | 0.015 |
Dimension:mm
*The thickness of one side of the tip (O.D.-I.D.) / 2.
*For a small diameter hole, a minimum wall thickness (one side) of 0.015mm is required.
*Example: In the case of a tip inner diameter of φ0.025mm, the minimum tip outer diameter is φ0.055mm.
*Laser marking can be applied to the flange. (Additional charges may apply)
*Please contact us with your desired dimensions and shape and consult us.
Dispensing nozzles and fluid injection nozzles often have a crawling problem when dispensing low viscosity fluids.
Orbray's dispensing nozzles can solve this problem by proposing a shape, material, and surface specification near the tip of the nozzle.
For example, during the production of precision parts or semiconductor-related parts, if a small amount of adhesive is used in a small area, the low viscosity of the fluid can cause crawling on the side of the nozzle tip. Our proprietary microfabrication technology allows us to improve the tip shape and surface roughness.
Ruby Sapphire Orifice Nozzles
Applications: Inkjet printers, semiconductor production, medical equipment
Ruby(Single crystal) | |||
---|---|---|---|
I.D | Hole straight length | O.D | Thickness |
φ0.014~2.5 | Same inner diameter - Inner diameter x 2 | φ0.8~6 | φ0.3~0.8 |
Sapphire(single crystal) | |||
I.D | Hole straight length | O.D | Thickness |
φ0.014~2.5 | Same inner diameter - Inner diameter x 2 | φ0.8~15 | φ0.3~0.8 |
Dimension:mm
Ruby sapphire aperture nozzles
Applications: Inkjet printers, semiconductor production, medical equipment
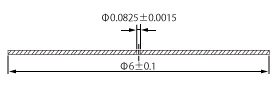
Ruby(Single crystal) | |||
---|---|---|---|
I.D | O.D | Thickness | Top and bottom surface roughness |
φ0.02~2.5 | φ0.5~10 | Same inner diameter - Inner diameter x 2 | Ra0.01 |
Sapphire(single crystal) | |||
I.D | O.D | Thickness | Top and bottom surface roughness |
φ0.02~2.5 | φ0.5~30 | Same inner diameter - Inner diameter x 2 | Ra0.01 |
Ceramic (Zirconia) | |||
I.D | O.D | Thickness | Top and bottom surface roughness |
φ0.02~2.5 | φ0.5~10 | Same inner diameter - Inner diameter x 2 | Ra0.01 |
Dimension:mm
*Please contact us with the dimensions and shape you require.
These dispensing nozzles are for inkjet printers, semiconductor manufacturing, and medical equipment. Monocrystalline ruby and sapphire have better surface roughness and wettability than polycrystalline materials, and therefore, the liquid flow is more stable. For example, a metal nozzle may not be able to apply the liquid straightly due to minute machining striations, scratches, or burrs.
In such cases, single-crystal ruby and sapphire, which have high hardness (Hv2000), have good straightness of hole processing by our processing technology, and by polishing the inside diameter, it is possible to dispense the coating material straight without any striations or burrs as with metal dispensing nozzles.
Picking nozzles and collets
Applications: Transportation of semiconductor products (resistors, IC chips, LEDs, sensors, etc.), inspection equipment, substrate mounting, precision components, and fine chips
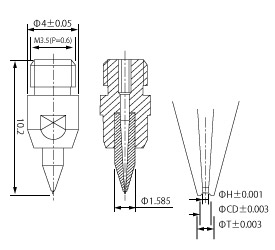
Ruby(Single crystal) | Ceramic(Zirconia) | Hard Metal | |||
---|---|---|---|---|---|
tip(I.D) (H) |
tip(O.D) (T) |
tip(I.D) (H) |
tip(O.D) (T) |
tip(I.D) (H) |
tip(O.D) (T) |
φ0.025~0.3 | φ0.055~0.5 | φ0.015~φ0.3 | φ0.045~φ0.45 | φ0.1~φ0.7 | φ0.13~φ0.8 |
Dimension:mm
*Laser marking can be applied to the flange. (Laser marking can be applied to the flange area (optional).
*Please contact us with your desired dimensions and shape.
Picking nozzles are used for semiconductor products (resistors, IC chips, LEDs, sensors, etc.), inspection equipment, substrate mounting, precision parts, and microchip transfer.
In recent years, the miniaturization of device products has led to the miniaturization of mounted parts such as semiconductor chips and sensors. We produce suction and transfer nozzles and collets for various industries, and can also manufacture picking nozzles and collets for extremely small chips (chip size 0201).
We can also manufacture nozzles with a shape that meets the user's application by making full use of our precision machining capabilities.
For example, if there is a sensor in the center of the workpiece to be conveyed and the user does not want to touch it, we can manufacture picking nozzles(adsorption nozzles) with a concave shape only in the center to minimize the surface to be touched.
Pharmaceutical and reagent dispensing nozzles
Application: Discharge of medicines and reagents during production of medical products
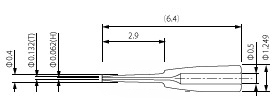
Ceramic (Zirconia) | |
---|---|
tip(I.D)(H) | tip(O.D)(T) |
φ0.04~0.13 | φ0.1~1.0 |
Dimension:mm
*Please contact us if you require single crystal ruby or single crystal sapphire.
*Please contact us for the dimensions and shape you require.
These dispensing nozzles are used in the process of discharging drugs and reagents when producing medical products.
Since the components of drugs and reagents are not allowed to change, it is often impossible to use metal nozzles, which are prone to corrosion.
Therefore, Orbray can manufacture dispensing nozzles made of high-purity ceramics, ruby, or sapphire, monocrystalline materials that are highly resistant to chemicals.
The reagent is expensive and cannot be wasted, so it is important to apply the right amount at the right time, and by machining the tip finely, it is possible to apply the reagent as close as possible to the area to be dispensed.
Also, single crystals of ruby and sapphire can be seen inside by shining light through them, making it possible to check the state of inflow.
Problem Solving
Problem solving of dispensing nozzles (Precision nozzles)
Enabling high-precision control of dispensing volume
Unstable dispensing conditions caused by the viscosity of the fluid to be dispensed can lead to low productivity if the fluid cannot be dispensed precisely (in the right amount) to the targeted location. Our dispensing nozzles improve fluidity by devising fluid flow paths in the nozzle bore, which prevents clogging and bending of the fluid, thereby improving dispensing accuracy.
Our ceramic nozzles also have an extremely smooth fluid path surface, which improves fluidity, shortens tact time, and improves yield.
Prevents interference with a variety of workpieces in fine dispensing
When dispensing in a narrow area, the tip of the precision nozzle may come into contact with the workpiece, causing the fluid to stick or string outside of the targeted area. To solve such problems, we offer nozzles that are as close as possible to the application position by making the nozzle tip as sharp as possible and machining a clearance so that it does not contact the workpiece, enabling precise application even in narrow spaces.
Problem Solving of Picking nozzles (Collets)
Proposal of picking nozzles suited to the workpiece is possible
We can design an adsorbed surface that matches your workpiece. From the selection of material, we can propose a collet tip shape design suitable for a wide variety of workpieces.
Example,
With metal nozzles, the nozzle tip wears out or bends, preventing accurate application.

Wear-resistant measures can be taken using ruby, sapphire, and ceramic, which are resistant to wear
Do not want to touch the surface of the workpiece to be adsorbed.

The nozzle tip can be processed into a concave shape so that it does not touch the workpiece surface and can be applied to only a corner of the workpiece as much as possible.
Heat is generated during suction.

Proposal of Vespel, a heat-resistant resin, is possible.
Long life is realized with high wear-resistant material
For the problem of tip wear of picking collets, hard materials such as single-crystal ruby, reinforced alumina, and zirconia are used to achieve long life with excellent wear resistance.
In addition, the low wear of the tip allows workpiece positional accuracy to be maintained over a long period of time, contributing to overall productivity improvement.
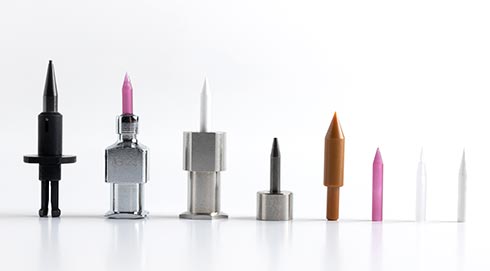
Problem Solution Examples
Precision machining significantly improves productivity of LCD panels by controlling the amount and reproducibility of minute (liquid crystal) coating.
Our core technologies of "cutting, grinding, and polishing" are used in various fields such as semiconductors, industrial equipments, medical parts manufacturing, and laboratories. As the size of LCD panels increases, more precise control of coating volume is required, and our monocrystalline ruby nozzles, which enable stable and precise control of coating volume with long life, are useful in the field. Especially in the manufacturing process of LCD panels for flat-screen TVs and PCs, adhesives are applied to a wide range of areas with dispensing nozzles and needles. Orbray contributes to the improvement of dispensing accuracy through precision machining of nozzle shape, hole size, and bore diameter, as well as surface roughness to meet the customer's requirements.
Custom dispenser nozzles order flow (from consultation to delivery)
Inquiry
Please feel free to contact us. We will respond to your request with ultra-precision processing.

Specification Confirmation,
Examination, and Proposal
After confirming the requested specifications (drawings, cartoon drawings, etc.), our engineers with know-how and experience examine the material and shape while confirming the customer's requirements, and make a proposal after incorporating them in the examination drawings.

Trial production
at our factory
After the specifications are finalized, we manufacture the prototype at our factory in Akita Prefecture with speedy and careful manufacturing.

Inspection
As a manufacturer of ultra-precision products, we have the ability to inspect products at the sub-micron level to provide high quality products.

Notes
*A two-pronged screw is a screw with two screw spirals. The distance that a screw with one helix (one-way screw) advances in one rotation is called the lead, but a two-way screw has twice the lead of a regular screw in the same one rotation, enabling quick mounting with fewer rotations.
There are differences in the mounting part depending on the equipment manufacturer and model. Generally, the two-joint screw type is the mainstream, but please confirm this when considering the product.
*What is a luer lock: A threaded, more pull-resistant type of fixture system that prevents fluid leakage in syringes and other medical devices.