Achievement of micro-hole processing in brittle materials with in-house diamond micro drill
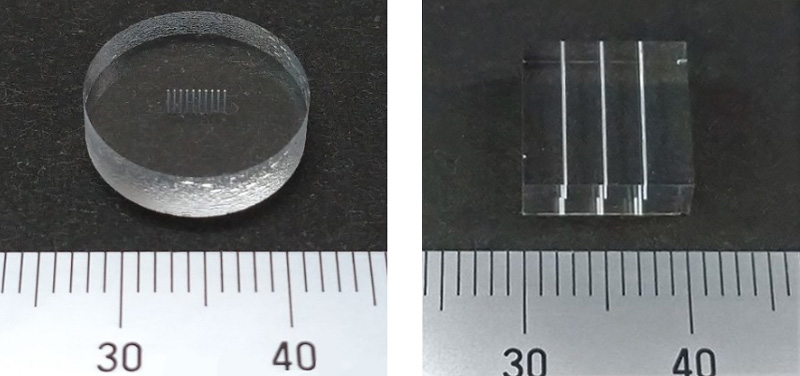
Overview: Micro-hole processing with micro drills
Drills are widely used for hole processing in the automobile, semiconductor, optical products, medical equipment, and other fields. Various materials are processed, such as metals, plastics, ceramics, and single crystal, and the hole diameters have a wide range from 50mm large to less than 0.1mm small. Generally, micro-hole processing with micro drills refers to drilling holes with diameters less than 2∼3mm. A typical example of this is drilling holes in a printed circuit board.
Micro-hole fabrication with drills is very difficult because the strength of the drill is low due to its small diameter, and deep holes are often needed. Micro-hole drilling is also affected by the small vibrations of the machine and radial run-out of the drill. And while high precision holes are often required, post-process finishing is very challenging.
The accuracy of micro-hole fabrication with a drill is determined by the matching between the drill and the machine tool, the tooling for holding the drill, as well as the drill itself. As indicated in the figure below, there are various types of drills, tooling, and machine tools. Therefore it is necessary to choose the drill and machine tool based on the specific purpose, and to optimize the fabrication conditions. This is where each company's know-how comes in.
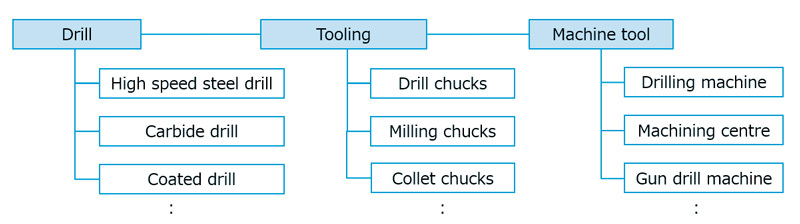
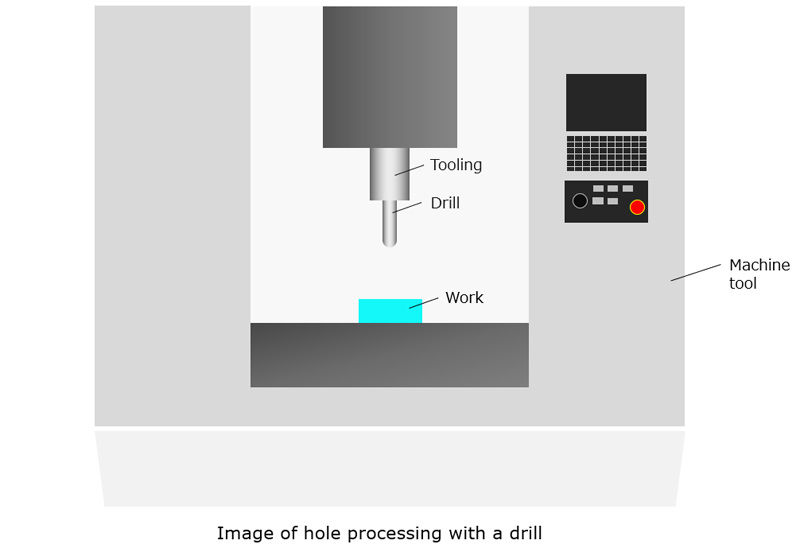
Classification of Orbray's diamond micro drill
Drills can be classified into three types: high speed steel, carbide, and coated. Coated drills have improved toughness and wear resistance, which is achieved by coating a high speed steel or carbide drill with titanium alloy or diamond. Our diamond micro drill was developed to solve the life problem of coated drills. It is made from polycrystalline diamond and can drill hard materials efficiently.
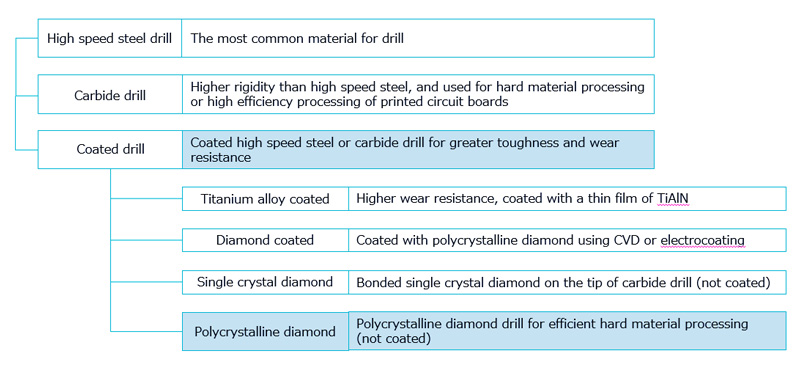
Features of micro-hole processing with Orbray's diamond micro drill
We have been mass producing diamond styluses for many years. In the stylus manufacturing process, it is necessary to polish the diamond tips into special shapes. By applying this polishing technique to micro drills, we have developed a diamond micro drill whose entire shank is made from polycrystalline diamond.
We offer the best solutions for micro-hole fabrication of brittle materials such as glass, alumina, ruby and sapphire with this diamond drill. We can process ultra long holes with a minimum diameter of 0.1mm and maximum aspect ratio over 60. Since the material of the whole shank is diamond, it is possible to process numerous holes consecutively. Moreover, as the sample is ground by the diamond, the inner surface of the hole can be polished by choosing the processing conditions. In this case, the final polishing process after drilling is not necessary and the hole is suitable for observation of liquid flow and use as a micro channel. Furthermore, we can combine the drilling process with our femtosecond laser, UV laser, and polishing techniques. It is possible to perform drilling on tubes as well as plates.
We are the drill manufacturer as well as the micro processing company. There are many tool manufacturers that sell drills, and also many micro processing companies. However, there are a limited number of companies that can produce both the micro drills and micro-holes. We have been doing micro-hole processing for more than thirty years since the development of the diamond micro drill. Since we have deep knowledge of both of the properties of the drill and the machine tools, we can provide a shorter lead time in terms of processing optimization than other manufacturers.
Comparing diamond micro drilling with other microfabrication technologies
This table compares diamond micro drilling with other microfabrication processes. For the purposes of comparison, the example used in the table is micro-hole processing in silica glass, which is frequently used for biology research needs.
Microfabrication processes |
Minimum diameter |
Maximum aspect ratio |
Surface roughness |
Damaged area from processing |
---|---|---|---|---|
Ultrasonic processing |
150μm |
3∼4 |
Rough |
Exists |
Diamond micro |
100μm |
60 |
Smooth |
Small |
Sandblasting |
100μm |
1∼1.5 |
Rough |
Exists |
25μm |
20 |
Rough |
Exists |
|
0.5μm |
100 |
Smooth |
None |
|
Dry etching |
0.01μm |
5 |
Very smooth |
None |
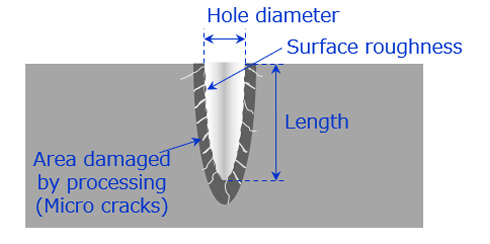
Silica glass is a brittle material that breaks easily, and it is generally difficult to form micro-holes in it.
Although ultrasonic processing and sandblasting can create holes around 100μm in diameter, they can only form short holes with an aspect ratio of 1∼4 because of limitations in tool fabrication and mask durability. Damage such as micro cracks often occurs around the hole surface, and the surface is rough, becoming like ground glass.
When it comes to drilling with normal carbide and coated drills, a long drill with a small diameter is hard to create, and the largest possible aspect ratio is only 4∼20. Additionally, with coated drills, if the coating film (such as diamond or diamond-like carbon) peels off, the carbide surface becomes exposed and wear resistance worsens, making it difficult to process numerous holes consecutively.
Our own company know-how has allowed us to make an extremely long drill, and this diamond micro drilling can form ultra long holes with a maximum aspect ratio over 60. The shank of our diamond micro drill is made entirely of diamond, so it is possible to cut material even with a small amount of frictional wear. Therefore we can fabricate a large number of holes continuously. In addition, since the diamond grinds the material, surface roughness and damage to the area can be minimized by optimizing the fabrication conditions, and we can offer the equivalent of a polished inner surface.
Regarding UV laser, femtosecond laser and dry etching, these processes are suitable for a more precise range of micro-hole fabrication. We have both UV laser and femtosecond laser, and we usually select the proper technology based on the processing dimensions. For example, in the case of a hole of micrometer order diameter and millimeter order length, we have established the following combination drilling method: Using our diamond micro drill, the large diameter hole is created partway through the material, and then the micrometer order hole is formed from the other side with the femtosecond laser.
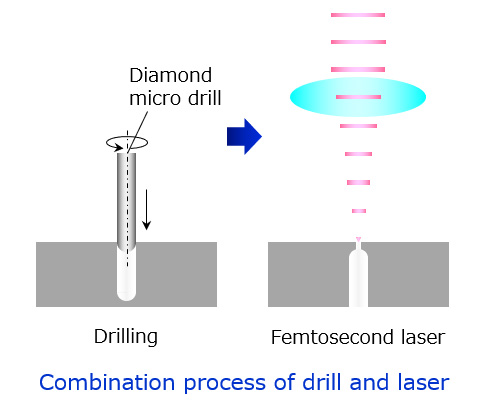
Another example of combination processing is micro drilling and polishing, which is our core technology. We can make the openings of the holes tapered by applying a final polishing. In these ways, we can offer the best solutions by choosing the most suitable processing and combining the fabrication techniques.
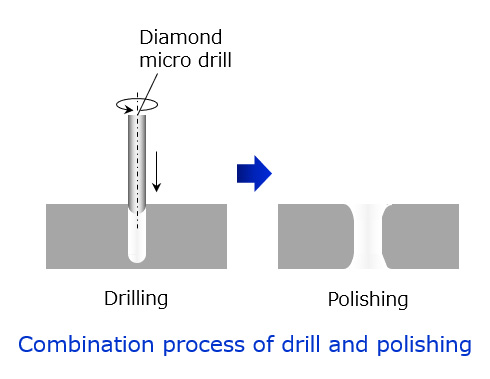
The shapes of the drilled materials can be cylinders and bottles as well as plates.
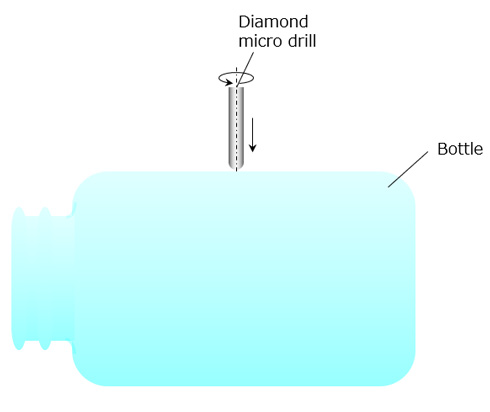
We have received many requests from customers regarding micro processing of brittle materials like glass, ceramics, and sapphire, and we have an extensive track record of producing both engineering samples and mass production quantities. We work with our customers starting from the design stage, to test samples, to mass production. Please do not hesitate to contact us for your micromachining needs.
Applications and examples
Ultra long hole with high aspect ratio
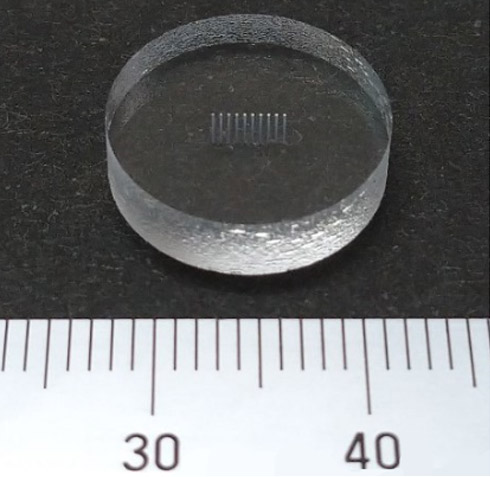
- Material: silica glass
- Spec.: φ0.1mm, L3.8mm, aspect ratio 38, 10 holes
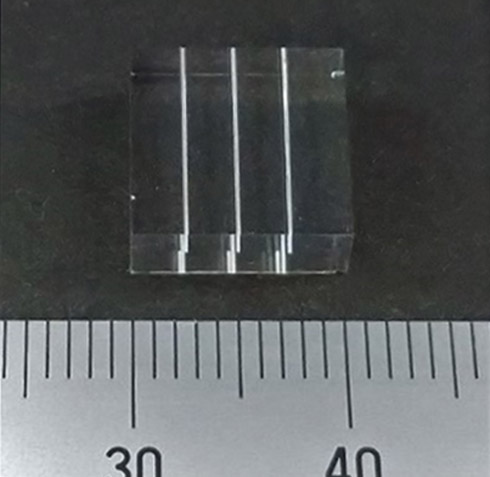
- Material: silica glass
- Spec.: φ0.15mm, L10mm, aspect ratio 67, 3 holes
>Numerous consecutive drillings
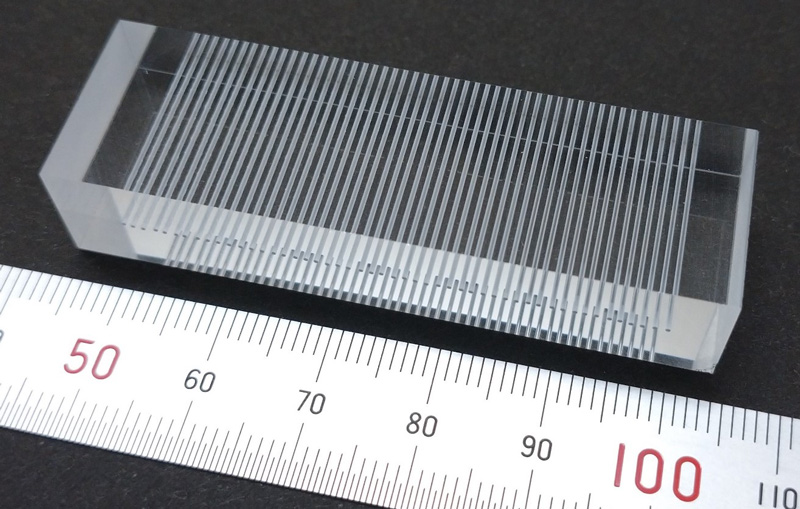
- Material: silica glass
- Spec.: φ0.46mm, L18mm, 50 holes, consecutive drilling
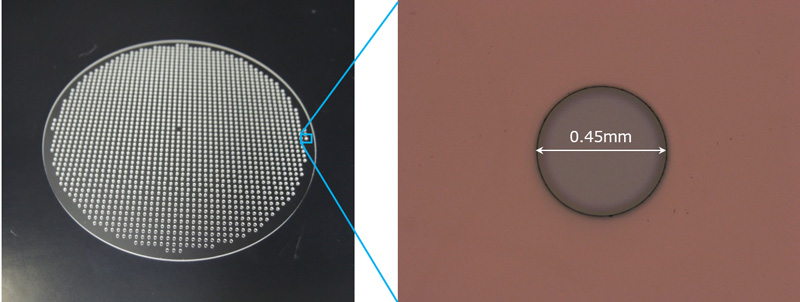
- Material: sapphire (φ2” wafer)
- Spec.: φ0.45mm, 1800holes, continuous processing
- It is possible to drill hard materials like sapphire continuously with the use of diamond.
Mirror-smooth finish processing of inner surface
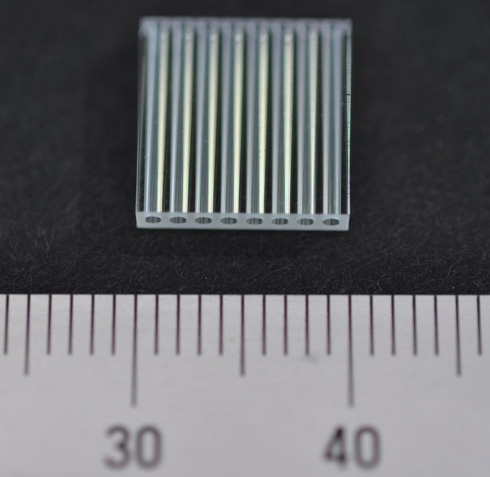
- Material: silica glass
- Spec.: φ0.8mm, L10mm
- Application: micro channel
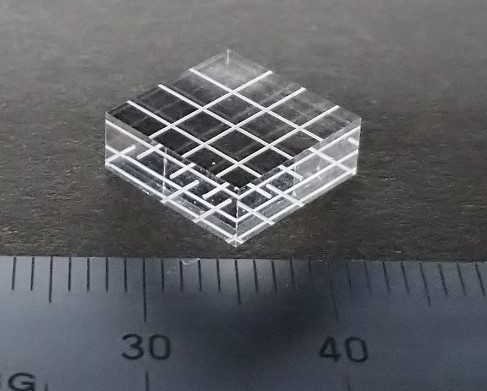
- Material: silica glass
- Spec.: φ0.2mm, L10mm, 3x3 orthogonal distribution holes
- Application: micro channel
- It is possible to manufacture holes that intersect orthogonally.
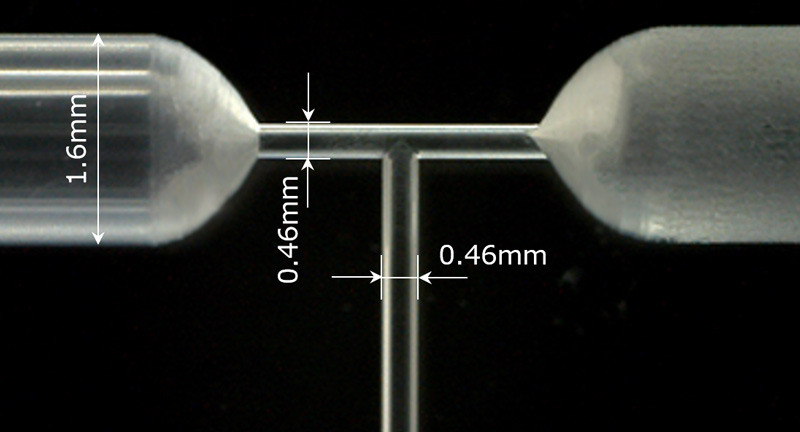
- Material: silica glass
- Spec.: T shape drilling with φ0.46mm and φ1.6mm
- Application: Micro channel
- It is possible to manufacture orthogonally-intersecting holes, or connect holes of different diameters.
Combination processing with diamond micro drill and femtosecond laser
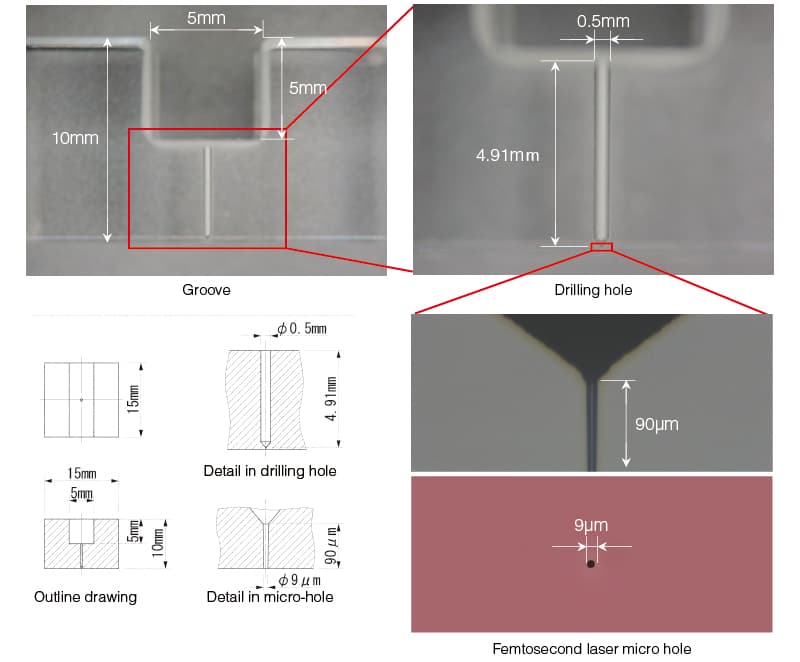
- Material: silica glass
- Spec.: groove width 5mm, depth 5mm;
micro drill hole φ0.5mm, L4.91mm;
femtosecond laser micro-hole φ9μm L90μm - Application: used for high-pressure liquid flow.