自社製ダイヤモンドドリルにより微細穴加工を実現
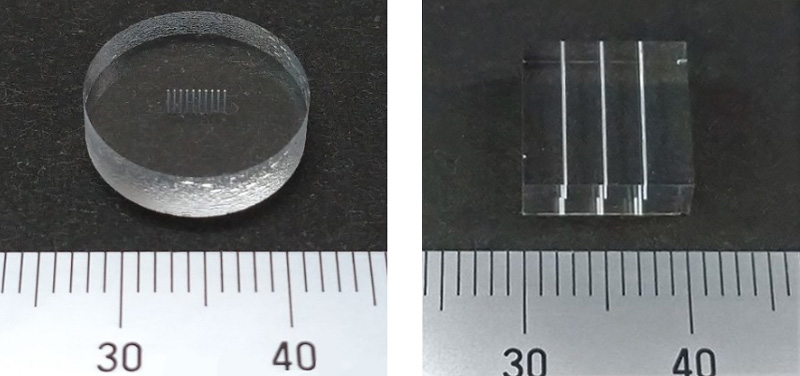
概要 マイクロドリルによる微細穴加工について
ドリルによる穴加工は、自動車、半導体、光学製品、医療機器など様々な分野で利用されています。加工される材料は金属、プラスチック、セラミックス、単結晶など多種多様で、寸法は50mm程度の大きな直径の穴から0.1mm以下の小さな穴まで広範囲にわたります。一般にマイクロドリルによる微細穴加工は、直径2~3mm以下の穴をドリルで加工することを指します。例えばプリント配線板の穴加工が代表的なものになります。ドリルによる微細穴加工は、ドリルの直径が小さくドリル強度が低くなる一方で、深い穴の加工が多いため、非常に難しいものになります。また機械の振動や振れに影響されたり、穴加工後の仕上げが困難であるのに高精度の穴が要求されるため、やはり非常に難しいものです。
ドリルによる微細穴加工の精度を決めるのは、ドリル本体はもちろんのこと、工作機械とのマッチング、さらにドリルを保持するツーリングも重要な要素となります。下の図のように、ドリル、工作機械、ツーリングにも様々な種類があります。そのため、目的に合ったドリルや工作機械を選択し、加工条件を最適化していく必要があります。これらは各社のノウハウでもあります。
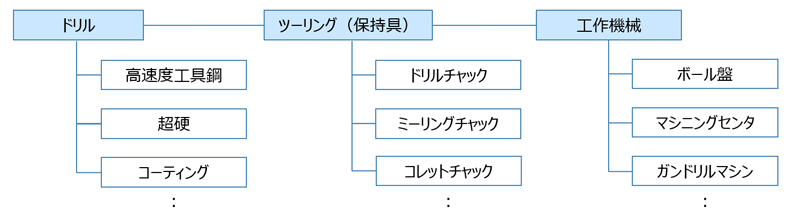
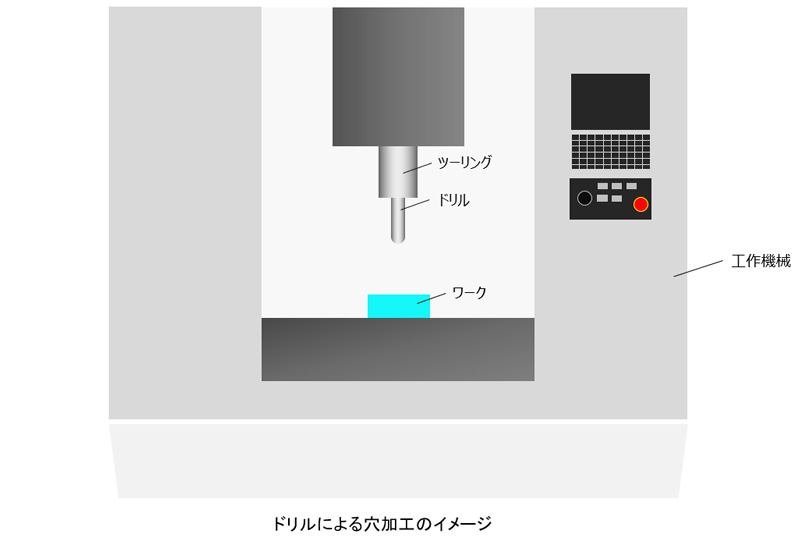
ドリルの中でのダイヤモンドマイクロドリルの位置づけ
ドリルはその材質で分類すると、高速度工具鋼(ハイス)、超硬合金、コーティングドリルの3つに分けられます。コーティングドリルは、ハイスや超硬にTi合金やダイヤモンドをコーティングすることで、ハイスや超硬よりも靭性や耐摩耗性を向上させたものです。当社のダイヤモンドマイクロドリルは、コーティングの摩耗による寿命を解決するために、全面を多結晶ダイヤモンドとして高硬度材を高能率で加工できるようにしたドリルとなります。
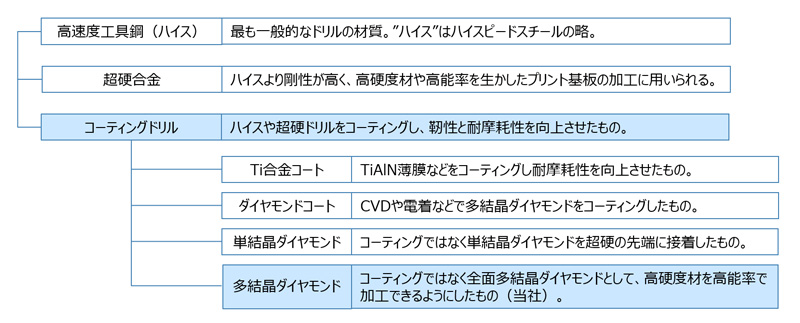
当社のダイヤモンドマイクロドリルによる微細穴加工の特徴
当社は長年ダイヤモンドレコード針を量産してきました。レコード針は、ダイヤモンドの先端を特殊な形状に研磨する必要があります。この研磨技術をマイクロドリルの加工に応用し、全面がダイヤモンドでできたダイヤモンドマイクロドリルを開発しました。
当社はこのダイヤモンドマイクロドリルを用いて、「ガラス、アルミナ、サファイア、ルビー」などの脆性材料に対する微細穴加工を最も得意とします。微細穴の最小径で0.1mm、最大アスペクト比>60の超ロングホールの加工が可能です。ドリル自体が全面ダイヤモンドを使用していますので、連続多穴加工も得意です。またダイヤモンドで素材を加工していきますので、加工条件を選択すれば穴内面を研磨面にすることも可能です。この場合は穴加工後の仕上げは不要で、液体などの流れを見るのにも適しており、微細流路(マイクロチャネル)としてもお使いいただけます。さらに当社保有のフェムト秒レーザー、UVレーザーや研磨技術との融合による加工も得意としております。穴開けをする母材の形状は、板材はもちろんのこと、円筒形状にも加工が可能です。
当社はドリルメーカーでありながら加工メーカーでもあります。ドリルを販売する工具メーカーは多数存在し、また加工専業メーカーも多数存在します。しかし、ドリルメーカーでありながら加工メーカーである会社の数は非常に限られます。当社はダイヤモンドマイクロドリルの開発から30年以上微細穴加工を行ってきており、ドリルの特性と工作機械の特性の両方を知り尽くしていますので、加工条件最適化の時間を短時間におさえることができるのも特徴です。
微細加工技術の中でのダイヤモンドマイクロドリルの位置づけ
ダイヤモンドマイクロドリルと他の微細加工技術を比べたのが下表になります。一例として、バイオ分野で頻繁に用いられる石英ガラスに対して微細穴加工をする場合について説明します。
微細加工技術 |
最小穴径 |
最大アスペクト比 |
表面粗さ |
加工変質層 |
---|---|---|---|---|
超音波 |
150μm |
3~4 |
粗い |
有り |
ダイヤモンド |
100μm |
>60 |
滑らか |
小 |
サンドブラスト |
100μm |
1~1.5 |
粗い |
有り |
25μm |
20 |
粗い |
有り |
|
0.5μm |
100 |
滑らか |
無し |
|
ドライエッチング |
0.01μm |
5 |
非常に滑らか |
無し |
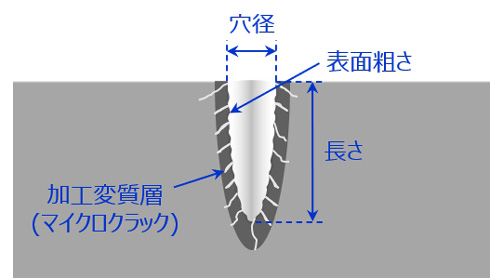
石英ガラスは脆性材料であるため割れやすく、一般に微細穴を形成するのは難しい素材です。
超音波やサンドブラストでは直径が100μm程度の微細穴は加工できますが、微小ツールの作製やマスク耐性が限られるためアスペクト比は1~4と長い穴の加工はできません。また穴の表面にはマイクロクラックなどの加工変質層ができ、表面粗さも粗く摺りガラス状になります。
次にドリル加工についてですが、通常の超硬やコーティングドリルによる穴加工では、微小径の長いドリルを作製するのが難しく、穴のアスペクト比は4~20にとどまります。一方、当社のダイヤモンドマイクロドリルでは、独自のノウハウにより非常に長いドリルを作製することができるため、最大アスペクト比>60という超ロングホールも加工可能です。またコーティングドリルでは、ダイヤモンドやダイヤモンドライクカーボンなどのコーティングが剥がれてしまえば、超硬が表面に露出して耐摩耗性が悪くなり、多数の穴を連続的に形成するのが難しくなります。しかし当社のダイヤモンドマイクロドリルはドリル全体がダイヤモンドでできていますので、多少の摩耗があってもダイヤモンドで切れることに変わりはありません。そのため、多数の穴を連続的に形成することが可能です。またダイヤモンドにより素材を加工していきますので、加工条件を選択すれば加工変質層や穴内面の表面粗さを非常に小さくすることができ、研磨面と同等にすることができます。
一方、UVレーザーやフェムト秒レーザー、ドライエッチングではより微細な範囲の穴加工が適していると言えるでしょう。当社ではUVレーザー、フェムト秒レーザーを保有していますが、加工寸法によって加工技術の使い分けをしています。例えば、直径がμmオーダー、長さがmmオーダーの穴が必要な場合、ダイヤモンドマイクロドリルで途中まで穴をあけ、先端のみフェムト秒レーザーでμmオーダーの穴を加工するという方法を確立しています。
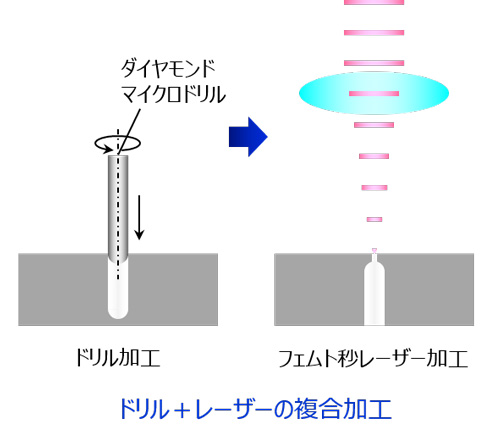
また例えば当社のコア技術である研磨技術を使って、マイクロドリルの穴の先端をテーパー状に広げることなども可能です。このように加工技術を適材適所に用いて融合させることも得意としております。
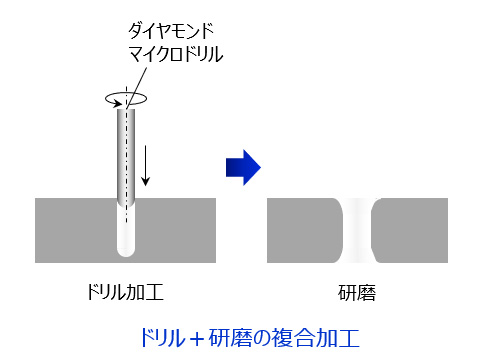
加工する母材は板材はもちろんのこと、円筒形状や瓶などにも加工することが可能です。
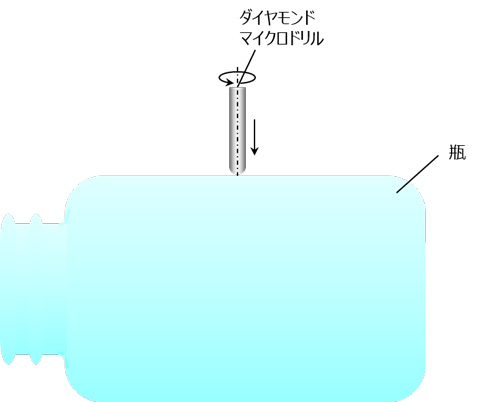
特にガラスやセラミックス、サファイアといった脆性材料の微細加工については、お客様から多数のご要望をいただき、豊富な加工実績・量産実績があります。試作ではお客様と一緒に形状・レイアウト等を打合せ、図面化することから始めます。試作から量産まで微細加工でお困りのことがございましたら、当社までお気軽にお問い合わせください。
加工実績・用途例
高アスペクト比・超ロングホール
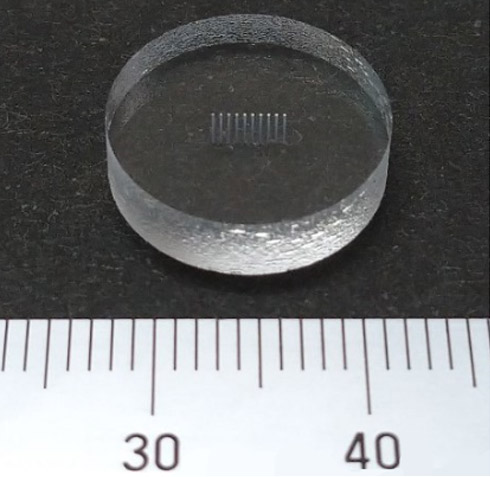
- 素材:石英ガラス
- 仕様:φ0.1mm, L3.8mm, アスペクト比38, 10穴
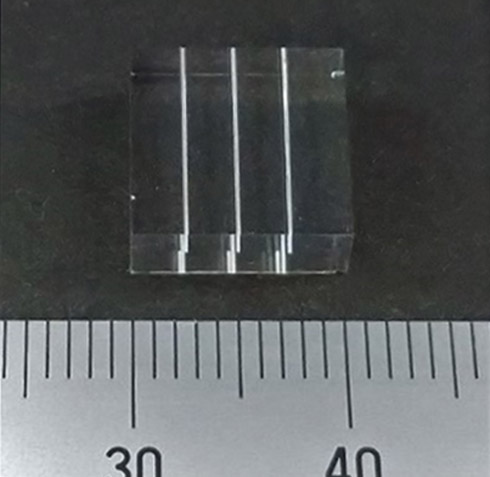
- 素材:石英ガラス
- 仕様:φ0.15mm, L10mm,アスペクト比67, 3穴
連続多穴加工
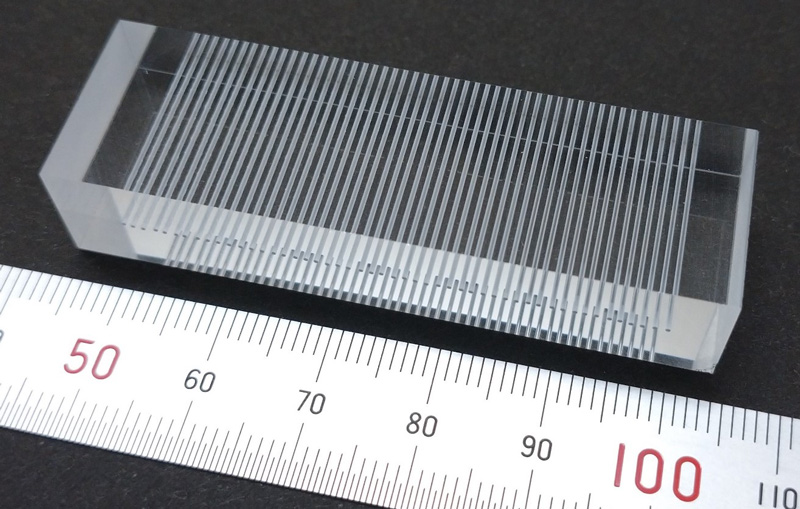
- 素材:石英ガラス
- 仕様:φ0.46mm L18mm 50穴の連続加工
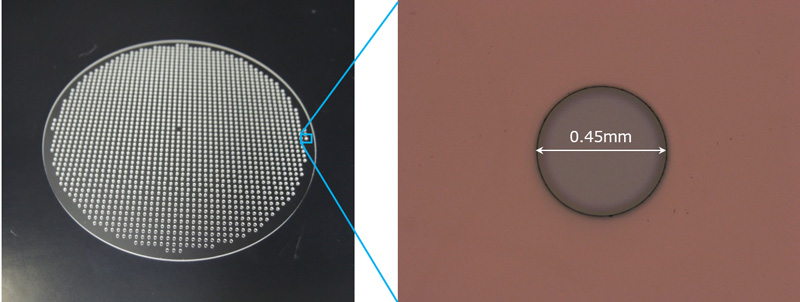
- 素材:サファイア(φ2”基板)
- 仕様:φ0.45mm 1800穴の連続加工
- 非常に硬いサファイアに対しても、ダイヤモンドで加工しますので連続加工が可能です。
内面鏡面加工
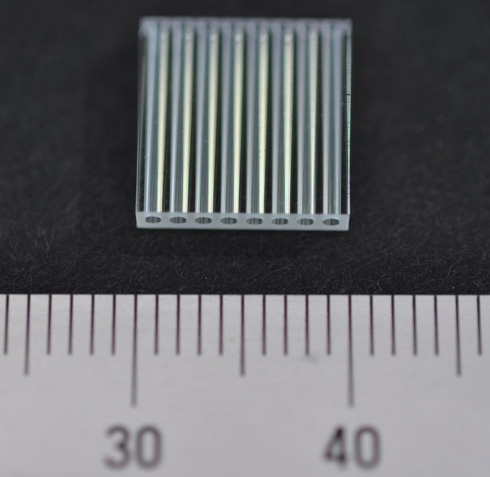
- 素材:石英ガラス
- 仕様:φ0.8mm L10mm
- 用途:微細流路として用いられています。
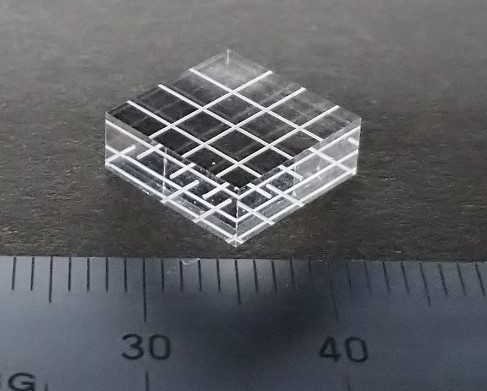
- 素材:石英ガラス
- 仕様:φ0.2mm L10mm 3行3列直交配列
- 用途:微細流路として用いられています。
- 穴が直角に交わる加工も可能です。
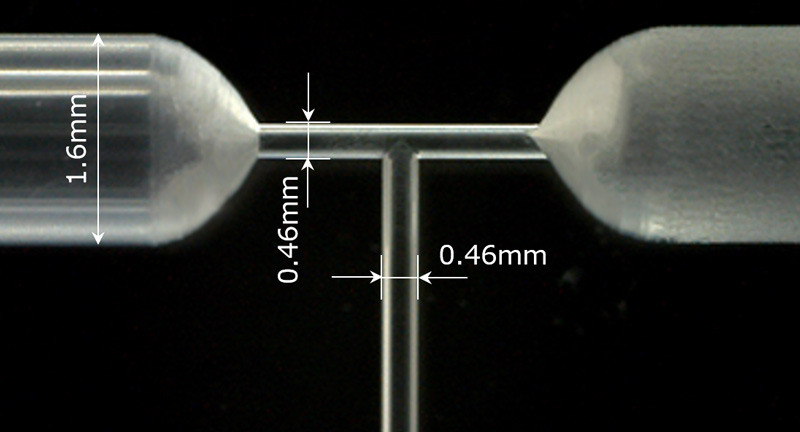
- 素材:石英ガラス
- 仕様:φ0.46mmとφ1.6mmによるT字流路加工
- 用途:微細流路として用いられています。
- 異なる径の穴をつなげたりT字型に加工することも可能です。
ダイヤモンドマイクロドリルとフェムト秒レーザーの複合加工
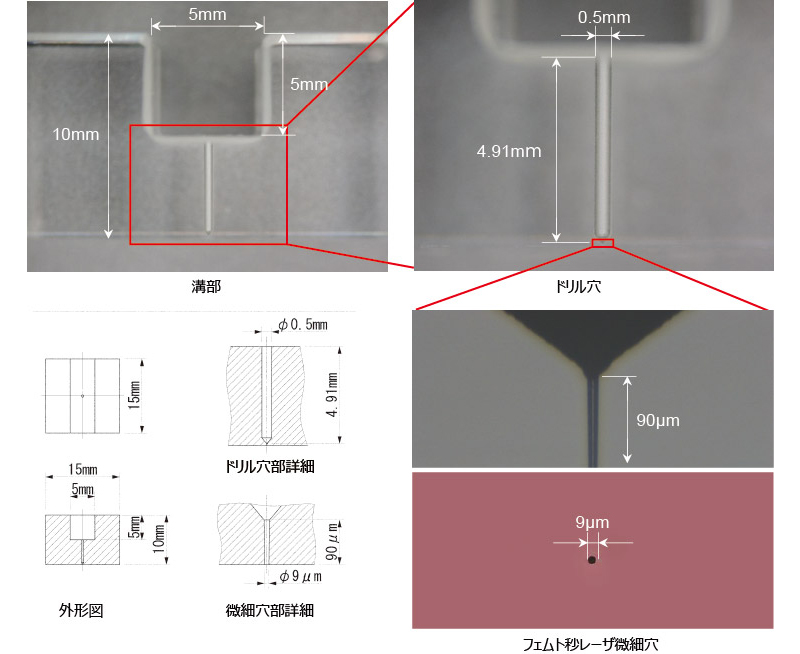
- 素材:石英ガラス
- 仕様:溝幅5mm 深さ5mm
マイクロドリル穴φ0.5mm L4.91mm
フェムト秒レーザー微細穴φ9μm L90μm - 用途:高圧の液体を流すのに利用されています。