Precision Nozzles: Materials, Shapes, and Applications
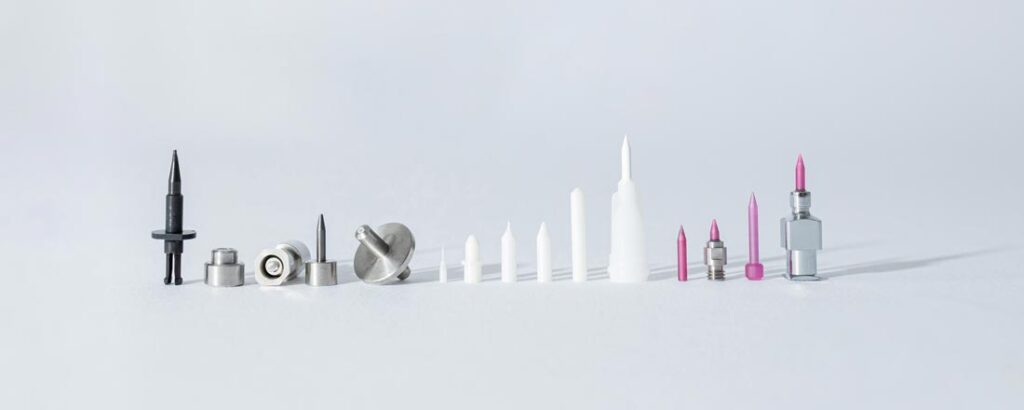
Precision nozzles are used to accurately apply very small amounts of liquids to precise locations, and also to pick up and transport minute components. They are often used in the manufacture of electronics equipment, medical equipment, and medical products.
Table of contents [close]
Characteristics of Precision Nozzles
Smartphones, tablets, and laptop computers continue to become smaller and thinner. In recent years, the semiconductors, electronic components, and optical components that go into making them have become so small that they cannot be manipulated by hand. The number of components in each device has also increased dramatically. Installing each component by hand is no longer feasible. Nowadays, these minute parts are set in place with machines and affixed by applying thermosetting resins and other adhesives. The application of these adhesives, the position, area, and amount must be controlled very precisely.
High-speed machines such as chip mounters are used to move a large number of parts quickly to the device being made. Chip mounters are also called electronic component mounters and are used for surface mounting electronic components onto printed circuit boards. Precision nozzles (suction nozzles/collets) are used in such equipment to pick up the components. The tips of the nozzles that pick up and transport the parts are engineered precisely to match the size and shape of each part. Since the nozzles come into contact with the parts, they are made of high-hardness materials that are durable and resistant to friction and bending.
The dispensers that are used to apply the adhesives have needle or precision dispenser nozzles. The diameter of the nozzle hole is precisely controlled down to the micron level. The inner surface of the nozzle is also polished smoothly. This makes it possible to accurately position the adhesive and apply the exact amount needed. When applying liquids that have low viscosity, the liquids tend to creep up the sides of the nozzle. This can be minimized by adjusting the shape and surface roughness of the nozzle tips.
https://creativecommons.org/licenses/by-sa/3.0,
via Wikimedia Commons
Modern electronics devices use many liquid crystal displays. When manufacturing liquid crystal displays, a very minute and accurate amount of liquid has to be applied to many locations across the entire area of the display. Furthermore, a single misapplication can ruin the entire display. An accurate and reliable precision nozzle is essential for the uniform and repeated application of liquids required in the manufacture of liquid crystal displays. Precision nozzles are also widely used in the medical field. Many pharmaceuticals are expensive, so inefficient application can lead to high costs. Precise volume control and application are required.
Shapes and Materials of Precision Nozzles
Hard metals (steel and carbide), super engineered plastics (e.g., Vespel), diamond, reinforced alumina (alumina zirconia), ceramics (zirconia), ruby, sapphire, and other materials can be used to make precision nozzles.
Unlike metal nozzles, nozzles made of ceramic, ruby, sapphire, and similar materials are resistant to corrosion and do not change the composition of the liquid being applied. Precision nozzles made of these materials play an active role in the medical field, where precise application of drugs and reagents is required. In addition, when light is shined onto single crystal ruby and sapphire nozzles, the silhouette of the liquid inside can be seen, allowing the flow condition to be verified visually.
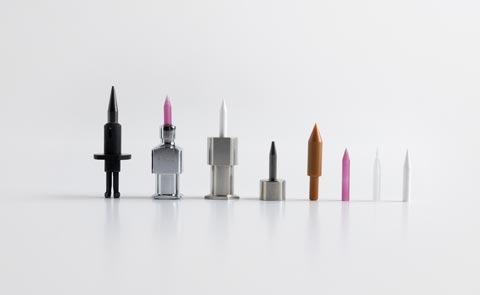
After repeated contact with the target objects, the tips of metal nozzles tend to bend and wear out over time. Precision nozzles made of wear-resistant ruby, sapphire, and ceramics sustain less of such deterioration. In addition, processing artifacts such as streaks and burrs are common in metal nozzles. In contrast, the high hardness (Hv 2000) of single crystal ruby and sapphire allows the drilling of straight holes, and the inner surface to be processed into a mirror-like smoothness. The wettability of these materials is also superior. The liquid flow out of the nozzle is very stable, and the discharge flow is very straight.
By making the tip of the nozzle as sharp as possible, it is possible to get close to the application point and apply with high precision, even in very small spaces. By processing the nozzle tip into a concave shape, it is possible to pick up components while contacting only the corners of the piece and avoiding contact with the rest of its surface. To make such nozzles with precision tips using ruby, sapphire, and ceramics, advanced micro-hole processing technology using lasers and drills is required.
Uses for Precision Nozzles
Precision nozzles are widely used in the electronics industry. They are used in chip mounters to pick up and transport electronic components during assembly and to dispense adhesives. They are also essential for liquid coating of liquid crystal display panels. Precision nozzles are also required for applying drugs and reagents in precise amounts for medical applications.
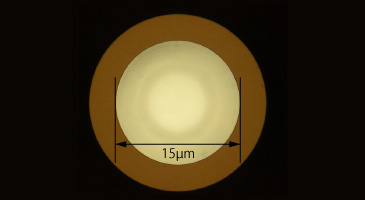
Dispenser nozzles are used not only for manufacturing electronics and other consumer products. They are also used, for example, when applying lubricants to equipment, and in manufacturing foods with viscous ingredients such as chocolate and cream. In such applications, there is a demand for precision nozzles that have good fluidity and can precisely control flow rates of the ingredients. Precision nozzles are also used for inkjet printer nozzles and in solder ball manufacturing.
At Adamant Namiki, we are able to manufacture precision nozzles from ruby, sapphire, and ceramics with tip inner diameters of 15 μm. Inner diameters can be processed down to the 1μm level with high reproducibility and stable production. The inner surface can be made smooth with a roughness Ra of only 0.010 μm or less by mirror polishing the inner surface. This allows for smoother fluid flows and reduced clogging, even in very fine diameter holes. Adamant Namiki precision nozzles can be used in a wide range of applications, from applying precise amounts of liquids to picking up small electronic components.
-
Introducing Bioceramics: Challenges, features, and applications
-
Introduction to suction nozzles and collets
-
Cut of Jewel
-
World's First Artificial Diamond Substrate Exposure Experiment in Space
-
What are ceramics? From industrial products to wristwatches, the many applications of ceramics
-
Lensed Fibers: Brief introduction to the functions and manufacturing methods