Hard materials and cemented carbides: Characteristics and processing methods
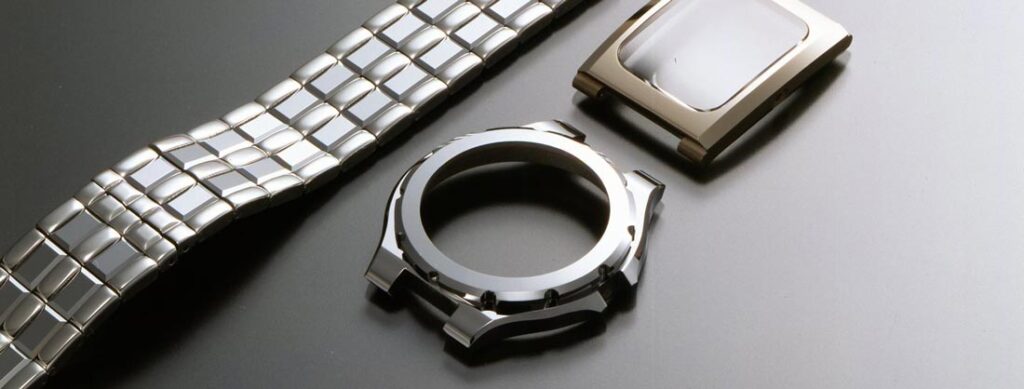
Hard materials (such as diamonds) and cemented carbides (such as tungsten carbide: WC) are used in various industrial applications. In order to use these materials industrially, they must be processed into the required shape for each application. However, because they are very hard, processing requires special technology and expertise.
Table of contents [close]
Characteristics and applications of hard materials and cemented carbides
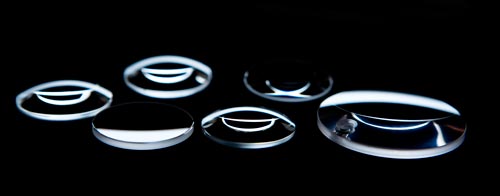
Diamond is the hardest material on Earth. Sapphire and ceramics are the second hardest. High hardness is a desirable property in many industrial applications, such as in cutting and grinding tools, bearings, and machine parts. As hard materials can be polished to a beautiful luster, they are also used in watches and jewelry. Sapphire and ceramics are also used to make crucibles, components for heaters, medical equipment, and similar products due to their excellent heat and corrosion resistance. Sapphire, which is strong, highly resistant to heat, and also transparent, is used to make observation windows in industrial furnaces.
Cemented carbides typically refer to nine types of metal carbides – tungsten (W), chromium (Cr), molybdenum (Mo), titanium (Ti), zirconium (Zr), hafnium (Hf), vanadium (V), niobium (Nb), and tantalum (Ta) – bonded (sintered) with metals such as iron (Fe), cobalt (Co), and nickel (Ni). They have a similar high degree of hardness as hard materials, and in addition have excellent wear resistance, strength, and elasticity. They also have small coefficients of thermal expansion and remain hard even at high temperatures. Because of these characteristics, they are often used in cutting tools and drill bits, as well as for press molds. In addition, they are similar to gold in being very dense with a high specific gravity.
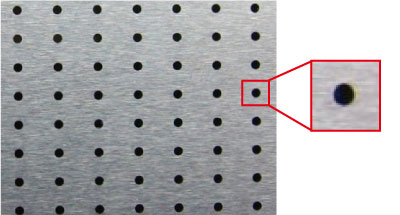
Tungsten carbide is a common type of cemented carbide. Tungsten is sintered with cobalt as the binder. Since tungsten carbide has a melting point as high as 2900 degrees Celsius, it is difficult to produce by melting, so the powder metallurgy method is often used. In powder metallurgy, metal powders are mixed and pressed into the desired shape before being sintered. The combinations of metal powders are selected according to the application. For example, titanium carbide (TiC) with its high specific gravity and tantalum carbide (TaC) with its amber color can be selected to produce cemented carbide with a combination of these characteristics.
Although high-speed tool steel can also be used to make cutting tools, cemented carbides are harder and maintain their hardness at high temperatures, resulting in better cutting performance. However, cemented carbides are not as tough, and they are prone to chipping of the cutting edge.
Difficult to process hard materials and cemented carbides
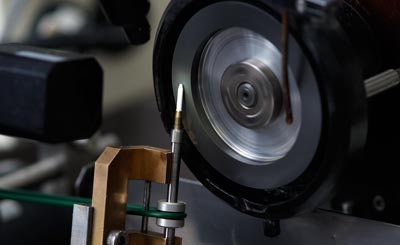
Ceramics, which are classified as a hard material, are molded into the desired shape and sintered. Cemented carbides are also made into the desired shape, using powder metallurgy. However, for ceramics and cemented carbides to be used in industrial applications, such as blades, cutting tools, molds, and substrates, they must go through a series of finishing processes, such as cutting, drilling, tapering, grooving, and polishing, according to their intended applications. Likewise, sapphire, which is manufactured using methods such as the edge-defined film-fed growth (EFG) method, also must also be processed according to each application. All of these high-hardness materials are difficult to process using cutting, grinding, and polishing.
There is another problem in the machining of hard materials and cemented carbides. The harder the material, the lower the toughness, making such materials prone to chipping and cracking. For example, to machine the item, a harder material must be used. Impact by the harder material could cause the edge of the item to chip, or the force applied could cause a thin item to crack. As hard materials and cemented carbides are very difficult to machine, high technology and expertise are required, in addition to special equipment and materials.
Methods for cutting, drilling, polishing, etc.
Hard materials and cemented carbides are processed using blades and slurries that have diamond abrasive particles with high hardness. Laser cutting and other methods are also used.
Polishing with a diamond abrasive slurry uses a polishing pad made of a material such as urethane to apply the slurry to the item being polished. Adjustment of the pressure, rotation speed, distribution of the diamond slurry, and other factors can achieve the desired polishing without cracks or chips.
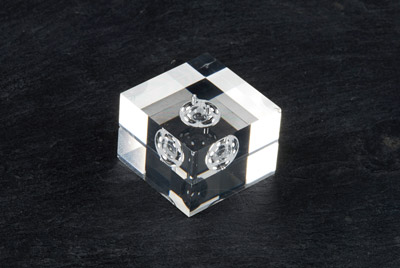
For high-hardness materials such as sapphire, polishing with diamond abrasive alone does not yield a smooth enough surface, so CMP (chemical mechanical polishing) is used for finish polishing. First, chemicals are used to soften the surface of the substrate, and then mechanical polishing is applied to achieve a highly polished surface, with a step only one atom high possible.
To cut diamonds and create grooves in cemented carbides, lasers are often used. Ultraviolet lasers with short wavelengths and high light energy, and femtosecond lasers with short pulses of energy and low thermal effects are used to create micrometer- to nanometer-level ultrafine holes in hard materials such as alumina, zirconia, single crystal rubies, and cemented carbides.
Adamant Namiki’s strength is that we have established high production expertise, from materials to in-house processing. Even for hard materials and cemented carbide, precision processing is possible.