Metallic Glass Features and Applications of a New Type of Metallic Alloy
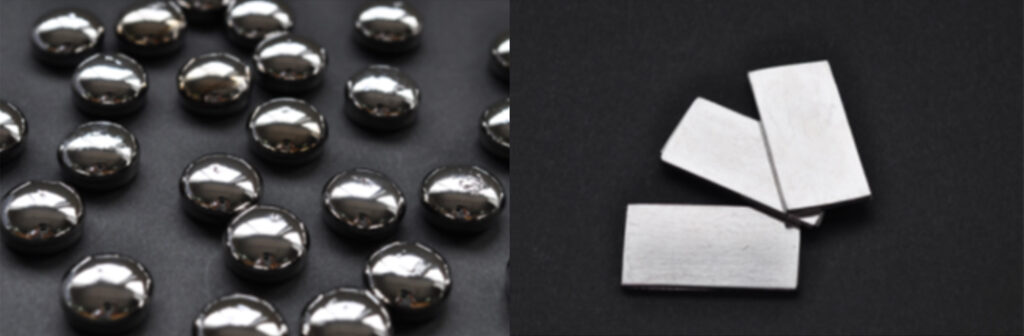
Metallic glass is a metallic alloy that has a unique set of characteristics, such as high strength, flexibility, and corrosion resistance. Having been commercialized in the 1980s, it has a relatively short history, and not many uses have been established. However, due to its desirable characteristics, expansion into industrial applications is expected in the near future.
Although the word “glass” is included in the name, metallic glass behaves very differently. Metallic glass is a solid metallic alloy that looks very similar to stainless steel. It is very hard, and unlike ceramics and other glass products, it will not shatter when dropped.
Here, we introduce two applications that benefit from the high strength of metallic glass.
Table of contents [close]
Better Gears with Metallic Glass
Gears have long been used as a mechanical method to transmit energy from one component to another. Gears can be found almost anywhere: from precision products such as cameras and watches to large machinery such as industrial machines, trains, and ships, and everywhere in between. Gears can also be made from a wide variety of materials such as metals, nonmetals, and plastics.
Metallic glass is not ideal in large applications, such as gears for ships. But it shines when applied to precision equipment. When large components are made with metallic glass, the cooling rate of the molten material slows down, allowing it to crystallize and become brittle. However, when the material is used for applications small enough to be cooled quickly, crystal formation is prevented, giving it the toughness, it is known for. Generally, metallic glass bars with a diameter of less than 5 mm and plates with a thickness of less than 3 mm can be made.
So, what is so great about metallic glass gears? First, metallic glass parts are very strong. The tensile strength of metallic glass is as high as 1600 Mpa. Even in its untreated state, metallic glass is as hard as heat-treated steel. High strength impedes failure of gears (breakage of gear teeth, etc.) under heavy loads.
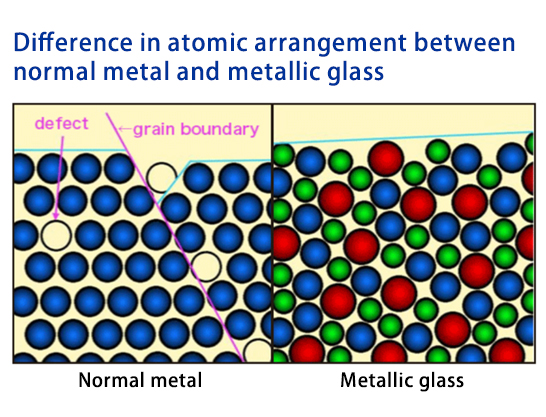
When a gear is loaded, the root of the gear experiences the greatest amount of bending stress. If the bending stress exceeds the allowable stress of the material, the tooth will crack or break off completely. Such failures can be prevented if the material strength is improved, allowing the product to withstand larger loads and a longer service life. This has added benefits of reduced maintenance frequency and costs. Also, the same strength can be achieved with smaller and thinner gears, allowing products to become smaller and lighter.
In addition, since metallic glass does not require heat treatment, there is no dimensional deformation, so high dimensional accuracy can be achieved.
In applications where high abrasion and high stress are present for extended periods, there are cases where metallic glass gears are superior, and others where steel gears are better. This depends on variables such as the design of the gear, the material of the mating gear, the operating mode such as load and rotation speed, and environmental conditions such as temperature and lubrication. Testing of metallic glass components should be done under conditions similar to those during actual use.
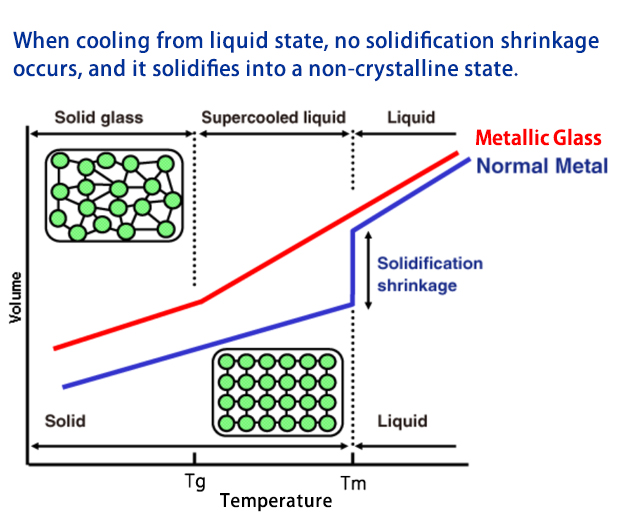
The second major advantage of metallic glass is that complex, high-precision parts can be produced using the injection molding method. Metallic glass does not shrink much during molding and has excellent transferability to molds.
For example, conventional parts made using the metal injection mold (MIM) method have shrinkage rates of 10% to 20%. The shrinkage rate of metallic glass is 0.2%, allowing high-precision parts to be made with conventional MIM methods.
High-precision gears can reduce backlash, improve efficiency, and reduce operational noise. Some examples of metallic glass gears manufactured by Orbray are shown below. Micro gears with a gear module of 22 μm and a diameter 182 μm have been achieved.
Although gears demonstrate the unique characteristics of metallic glass, the advantages of metallic glass are not limited to gears. Any part that requires precision and strength, especially mechanical parts and those that transmit energy mechanically, can benefit from metallic glass manufacturing technology.
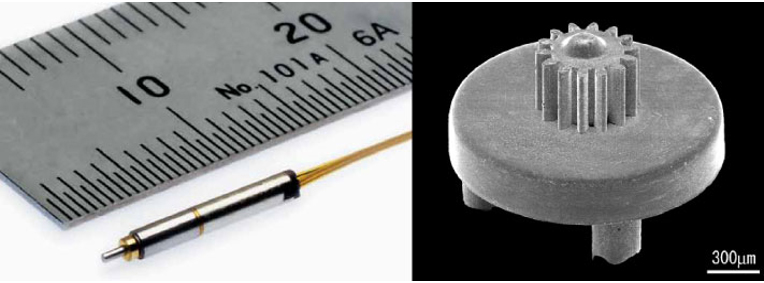
Wristwatch Components: Taking full advantage of metallic glass features
Stainless steel and titanium are often used in exterior components (such as cases and bezels) of conventional wristwatches. However, metallic glass has 3x to 5x the tensile strength of these materials. This means that even if the watch is accidentally dropped or is hit by a hard object, it will not break, deform, or scratch easily, allowing it to maintain its original luxurious appearance for many years. In addition, exteriors of high-end watches must be resistant to corrosion from sea water and sweat, and also be hypoallergenic for those with metal contact allergies.
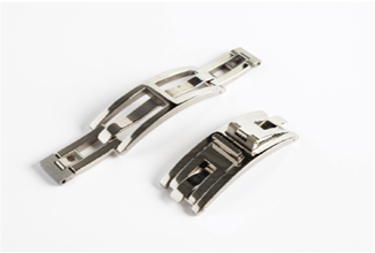
Metal allergies occur when nickel in the alloy leaches out in the presence of salt water or sweat and comes into contact with the skin. Metallic glass also contains some nickel, but the amount is minimal and not enough to cause allergic reactions. In addition, in corrosion tests, metallic glass has corrosion resistance equal to or greater than that of conventional stainless steel, titanium, and similar materials. Corrosion and deterioration of surfaces will not occur for many years.
Bringing a magnet close to a watch will cause the watch to stop or fail to keep correct time, because the casing and other components become magnetized, affecting the movements of the watch. However, watches made of metallic glass are resistant to magnets and magnetic fields. Even with the strongest magnets, metallic glass is difficult to magnetize.
Another advantage of metallic glass is that it can be formed with precision molds and injection molding. Since the desired shape is transferred to the finished product very precisely, it is possible to produce complex concave and convex shapes. Since the material becomes hard and vulnerable to temperatures above 400ºC, selection of the optimal processing conditions is essential. With careful attention, it is possible to create striking surface finishes such as mirrored surfaces, satin finishes, and hairline textures.
It is no surprise that Orbray’s metallic glass has been used in exterior components by high-end Swiss watchmakers.
Comparison of Properties
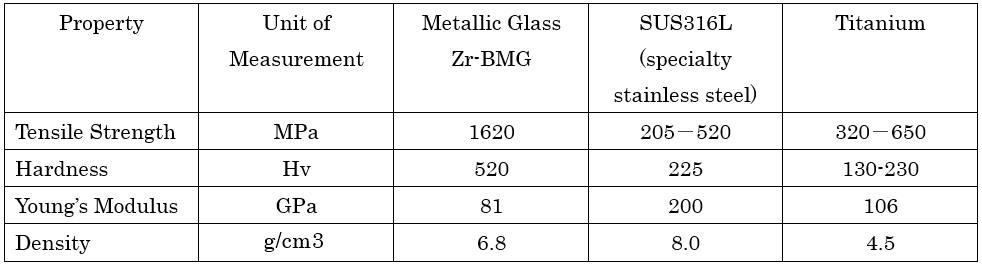
Metallic Glass Properties
・High mechanical strength, high hardness
・High mold transferability, capable of very precise molding and production
・Flexible
・High corrosion resistance
Two examples of applications that take advantage of the strength of metallic glass were introduced in this article.
In the next article, other applications that take advantage of other special properties of metallic glass will be introduced.
-
Crystal of Jewel
-
Jewel bearings: Orbray and the watch industry [Story of Watch 1]
-
The advantages and characteristics of ceramic watches
-
History of Orbray crystal glass [Story of Watch 3]
-
Watch Parts: Beautiful work of craftsmanship -the world's first artificial diamond parts-
-
Sapphire Glass [Story of Watch 4]