Drilling methods for micrometer to nanometer sized holes and their applications
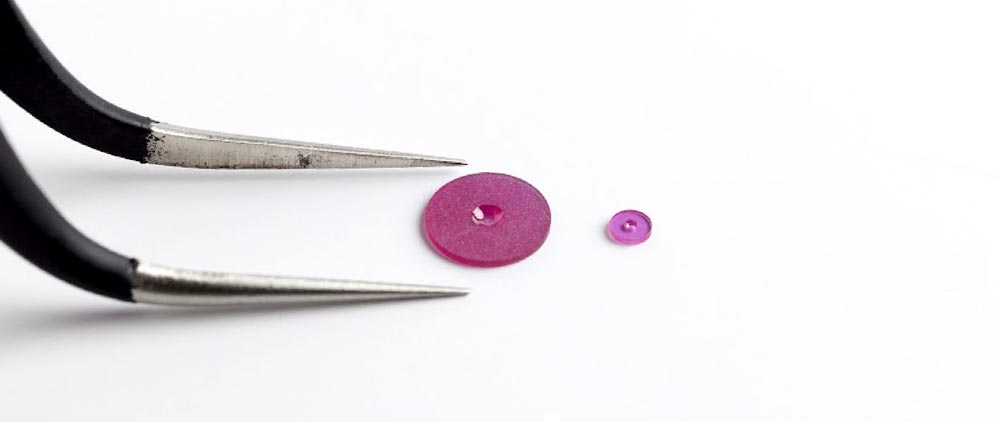
Fine hole drilling is an important process in the manufacture of various precision instruments and electronic components, such as watches, electronic devices, medical devices, and semiconductor products. Tiny holes can be drilled using many different methods, including small diameter drills and lasers. By selecting the appropriate drilling method, holes with micrometer to nanometer diameters can be created.
Table of contents [close]
Applications for precision instruments and biomedical devices
Drilling is used in the manufacture of a wide variety of products. In manufacturing precision instruments, the ability to create fine holes with high precision is especially important. Holes with diameters of a few millimeters are common. Micrometer and nanometer diameter holes are sometimes required, and the demand for such processing is increasing year by year.
For example, fine hole drilling is commonly required in making watches. In this case, a 70 μm hole is drilled in a ruby and polished to create a shaft bearing to support watch components. Fine holes are also used for manufacturing ultrafine synthetic fibers for high-performance fabrics. Micron-order diameter holes are drilled into high-hardness metals to create tiny nozzles, which extrude the fibers. In the biomedical field, fine hole technology is used to observe and manipulate individual cells. In addition, fine hole technology is used to create nozzles for microfluid devices that control the flow of minute amounts of liquids and gasses. For zirconia ceramic ferrules used in optical communications components, fine hole drilling technology is employed to make holes that are just a few microns in diameter.
Demand continues to increase for fine hole drilling of hard metals and brittle materials.
Various methods for drilling fine holes have been developed, such as mechanical drilling, laser drilling, electric sputtering, and etching. For drilling holes in high-hardness metals and brittle materials, such as glass, alumina, sapphire, and ruby, advanced processing technologies suitable for each material must be selected carefully. Demand for drilling holes in such materials has been increasing in recent years.
For example, very fine drills with diameters of less than 1 mm can be used to drill precision holes. Such mechanical methods often use carbide or diamond-coated drills. However, the smaller the drill diameter, the weaker the drill, and the greater the potential for bending or breaking during the drilling process, making high-precision drilling extremely difficult. In addition, the coating can wear off over time, leading to deterioration in performance when drilling holes in hard materials, thereby limiting the number of holes that can be drilled continuously.

Alternatively, drills made entirely of diamond can be used to drill fine holes. Diamond does not bend or break easily, so holes with high aspect ratios (depth/diameter) can be created. Because diamonds are wear resistant, a large number of holes can continuously be created without loss of production capacity. By adjusting the processing conditions, a polished surface can be achieved on the inside of the hole.
Short wavelength UV lasers and femtosecond lasers can be used to drill even smaller diameter holes in glass, alumina, sapphire, ruby, and other materials. In this process, high-energy laser light precisely focused by a lens is used to drill very minute holes. This can result in hole diameters as small as the wavelength of the laser beam. While lasers generally use the heat generated by light, UV lasers and femtosecond lasers drill directly with the light energy. Even diamond and sapphire can be drilled using this method.
Etching is another method that is often used to create very fine holes. In this process, a hole pattern is created using photomask and photoresist, then applied to a substrate. When the surface is treated with an etching solution or gas, areas not covered by the photomask are etched, creating holes. This method is commonly used in semiconductor manufacturing. The types of materials that can be processed by this method are limited by the etching capacity of the solution or gas. This method also cannot create holes with high aspect ratios.
Various processing methods for a wide range of applications
The hole diameter, aspect ratio, and inside surface texture depend on the drilling method used. Compared to sand blasting and ultrasonic methods, mechanical drilling can create much smaller, deeper, smoother holes.
For example, the minimum hole diameter that can be achieved in quartz using mechanical drilling is 100 μm, and the maximum aspect ratio is 60.
In contrast, UV lasers can create holes in quartz that are as small as 25 μm in diameter, with aspect ratios as high as 20 and a slightly rough inside surface texture. Femtosecond lasers can create holes as small as 0.5 μm in diameter, with aspect ratios as high as 100 and very smooth inside surfaces.
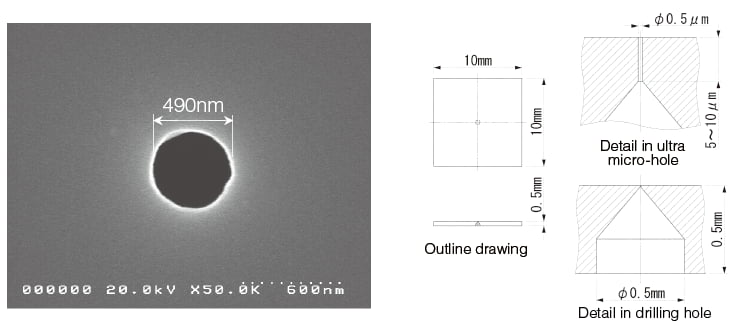
The processing method can be chosen to accommodate various materials and applications. It is also possible to use more than one method to achieve the desired results. For example, a hole could be drilled partway with a diamond drill and then tapered to a micrometer diameter at the end with a femtosecond laser. By also using the appropriate polishing technology, the hole could be formed into, for example, a tapered tip, a cylinder, or a bottle shape.
We can respond to a variety of requests, such as the development of parts for industrial and laboratory analysis equipment that require micro-holes.
-
What is LiDAR? How it works, technologies, and applications
-
Introduction to winding nozzles: an essential component of the motor coil winding process
-
Color of Jewel
-
Industrial applications of sapphire
-
Dispenser Nozzles: Applications for dispensing liquids and selecting the right one
-
Production of Sapphire