Dispenser Nozzles: Applications for dispensing liquids and selecting the right one
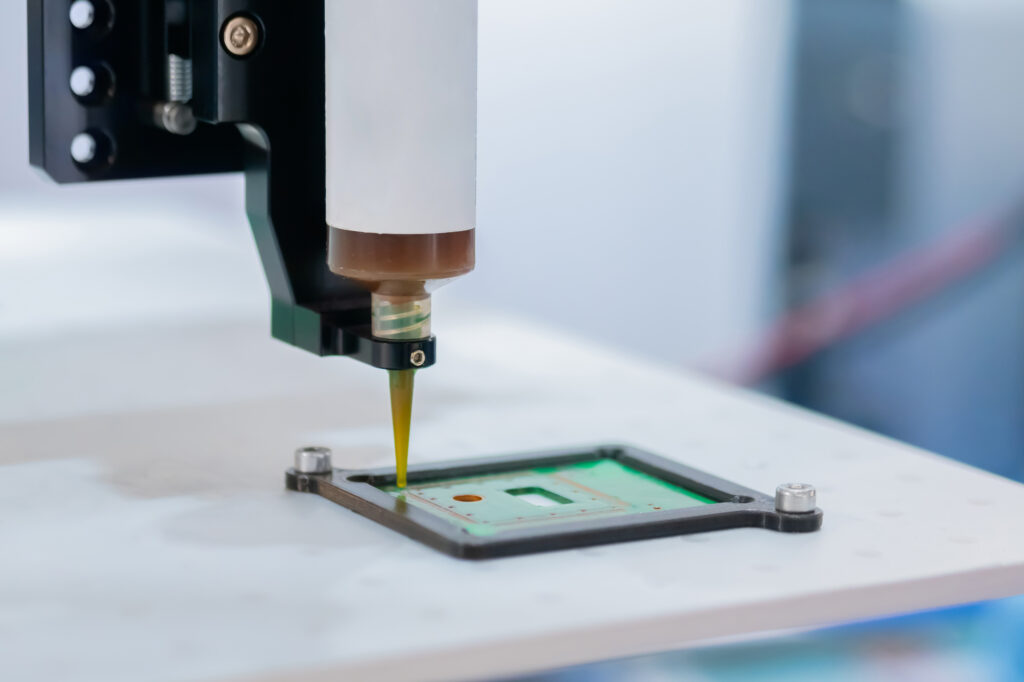
Dispensers are devices that deliver a fixed amount of liquid, such as paints and coatings, and are widely used in the manufacturing industry. Dispenser nozzles are essential parts of dispensers, allowing them to apply the liquids precisely, thereby greatly enhancing the accuracy of the dispenser.
This article describes how dispensers and dispenser nozzles are used, and important points to consider when selecting them for your processes.
Table of contents [close]
What are dispensers?
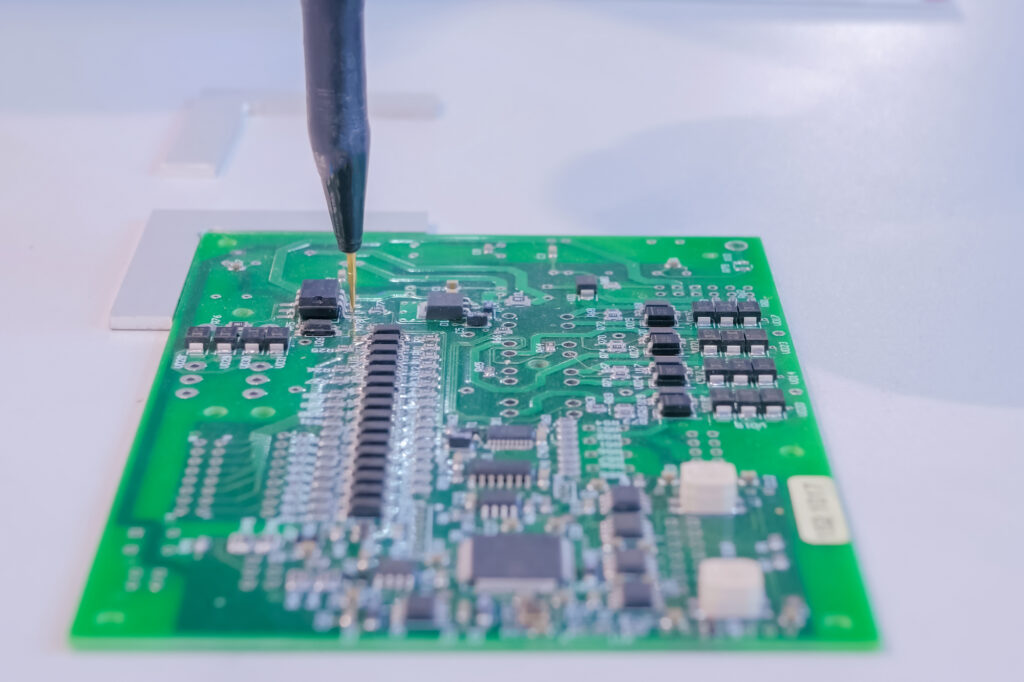
Dispensers are devices that discharge a fixed amount of a substance. In everyday life, we encounter dispensers for things like drinks, hand soap, cash, and other common items. In manufacturing, dispensers are devices that measure out and deliver a fixed amount of a liquid.
Applications for dispensers
Dispensers are used in many industries. The electronics and automotive industries rely on them heavily.
Electronics
・ Cementing lenses to camera modules
Miniaturization and other advancements have allowed parts such as camera modules to become very small. Adhesives are applied to their tiny parts by dispensers, without the need for brushes or other tools.
Automobiles
・ Applying grease to internal parts
By using non-contact dispensers and a multi-axis robot, grease can be applied to precise locations from many angles. This makes it possible to apply grease in small spaces such as door parts and instrument panels.
Displays
・ Assembling smartphones and tablets
Smartphones and tablets are made up of many small parts, such as touch panels, OLED or LCD displays, flexible circuit boards, small cameras, various sensors, batteries, and other components. In the assembly process, dispensers are used to apply minute amounts of adhesives in very precise locations to assemble the final product.
Dispensers are also used in a wide range of other fields, including chemicals, medical equipment, pharmaceuticals, cosmetics, and food.
Discharge methods of dispensers
There are several ways dispensers discharge their products, including the pneumatic method, the tube method, and the volumetric measurement method. Their major characteristics are described below.
・ Pneumatic method
The pneumatic method includes the syringe method, the contact-type metering valve method, and the non-contact-type metering valve method. The differences between each method are as follows.
In the syringe method, the liquid in the syringe is discharged under pressure. The syringe is disposable and does not require cleaning, so this is a relatively inexpensive method. However, if the amount of liquid in the syringe is not accurate, the discharge amount will also be inaccurate.
In the contact-type metering valve method, a tank containing a liquid agent is constantly pressurized. The valve is opened and closed using a controller to dispense the liquid as needed. This method is useful when dispensing large amounts of liquid or when high dispensing accuracy is required.
In the non-contact-type metering valve method, the liquid is ejected from the dispenser at high speed, so there is no contact with the workpiece. It is an effective method for applying minute amounts of liquid to intricate areas and dispensing fixed amounts at high speed.
・ Tube method
In the tube method, a tube containing the liquid is pressurized to discharge the liquid. This method is used to apply fast-drying adhesives. The tube is the only part that comes into contact with the work pieces. Therefore, no maintenance of the main unit is required.
・ Volumetric measurement method
This method uses volumetric measurement and a motor drive to extrude liquid without using air or pressure. Since it is a mechanical action that supplies the predetermined amount of material, it is not affected by changes in the material's own weight or viscosity. This method is highly accurate, especially for intermittent filling (such as packing bags with liquid). However, continuous supply and discharge is not possible, and if solids are mixed into the material, the discharge rate may be affected.
Each dispensing method has different strengths and weaknesses. Selecting the appropriate dispenser for the application is essential.
Benefits of using a dispenser
Some benefits of using a dispenser are as follows.
・ Since the discharge amount can always be controlled accurately, highly precise work can be performed consistently. This contributes to improved productivity and consistent quality.
・ Also, since the required discharge amount can be precisely controlled, no liquid is wasted, so costs can be reduced.
Manual application tends to have the problem of deviations in work accuracy, depending on the skill and experience of the worker. However, if dispensers are used, the work can be done without skilled technicians, resulting in consistency and accuracy in the application.
Introducing dispenser nozzles
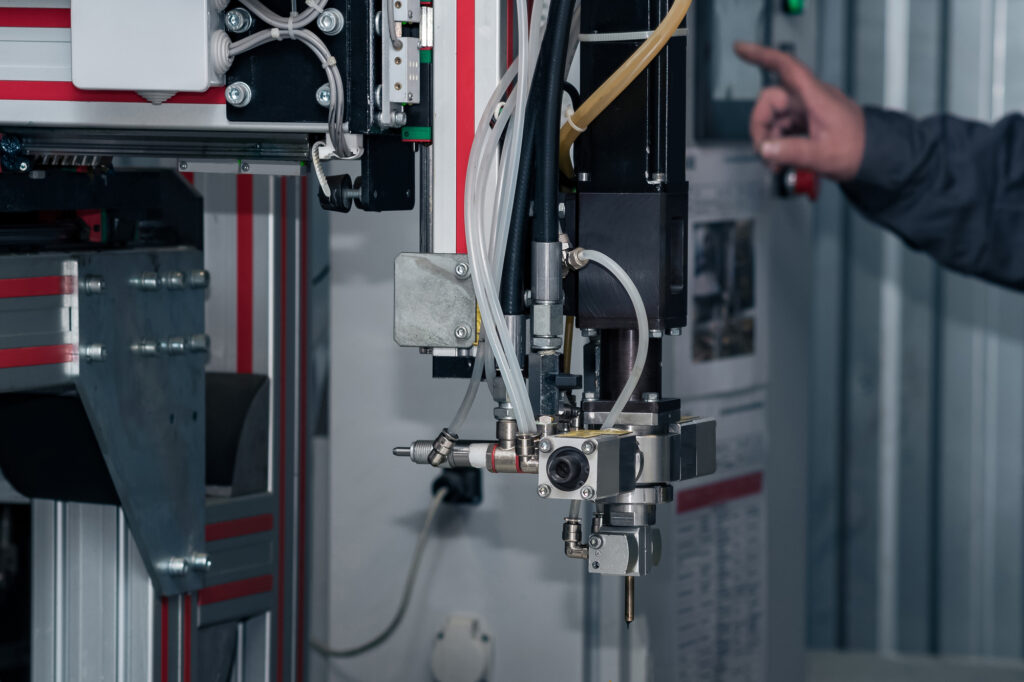
Dispenser nozzles are attached to the dispensers. Nozzles have many different features that can improve the dispensing process, depending on the application. Therefore, it is important to understand the different types of nozzles and how they apply liquid.
Types of dispenser nozzles
Including stainless steel (SUS), carbide, resin, ruby, and ceramic, there are many different types of dispenser nozzles. Since SUS and carbide are metals, they are highly durable. However, the tips of metal nozzles can wear and bend.
If the product has a resin nozzle that is compatible with anaerobic liquids, the problem of the anaerobic liquid solidifying inside the needle can be avoided. In addition, since resin is soft, it can be used to dispense into narrow areas without sustaining any damage.
Because ruby and ceramic nozzles are resistant to corrosion, they are used in the medical field to dispense medicines and reagents. Because these materials are highly wear-resistant, they have a long service life.
To create precision nozzles with finely shaped tips using ruby or ceramic, advanced micro-hole machining technology is required. The number of manufacturers that can perform such work is limited. At Orbray, we have the requisite technology for such high-precision processing.
Application methods
Typical application methods used by dispensers are as follows.
・ Molding
In manufacturing electronics, resin is applied to small devices. such as modules, in order to attach and protect the device. When the resin hardens, the device becomes permanently dust-proof, waterproof, and moisture-proof.
・ Coating
This is a method of applying a liquid agent that acts as a protective film to the surfaces of motherboards and electronic components of smartphones, computers, etc.
・ Surface coating
This is a method for applying a liquid over a wide area of a surface. Special nozzles are required for surface coating.
・ Dot application
Liquid can be applied in a dot-like pattern. The discharge amount is controlled by adjusting the discharge interval and the nozzle diameter. By using multiple nozzles and discharging liquid to multiple locations at once based on the shape of the object to be coated, work time can be shortened, and productivity can be improved.
・ Line-drawn coating
This is a method of applying liquid to an object in a straight or curved line. For line drawing, the use of multiple nozzles instead of a single nozzle can reduce work time and improve productivity.
When applying liquids with dispensers, it is important to choose a nozzle that is appropriate for the work at hand.
Difficulties related to performing application work with dispenser nozzles
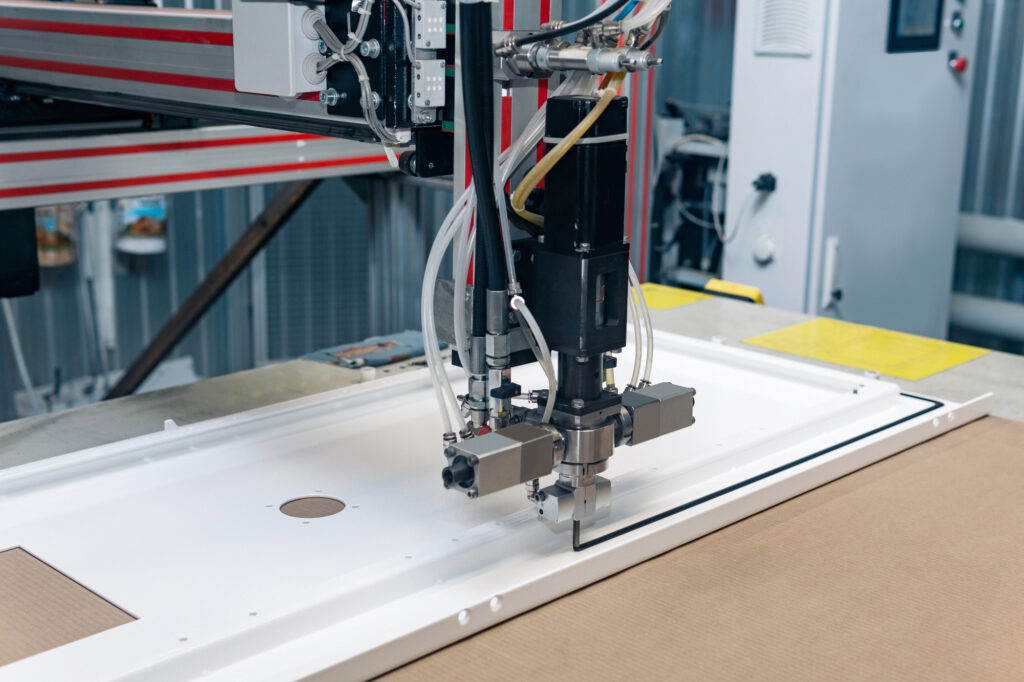
Manually dispensing liquids using dispenser nozzles is difficult to do with high accuracy and consistency. The speed of the work is also limited.
However, if dispensers and dispenser nozzles are used, it is possible to accurately apply the correct amount of liquid to a precise spot, in the correct size, over and over again with very high consistency. Production efficiency can be greatly increased. Dispensers are essential in the manufacturing industry, which requires mass production, low prices, and cost control.
Tips for selecting the right dispenser nozzle
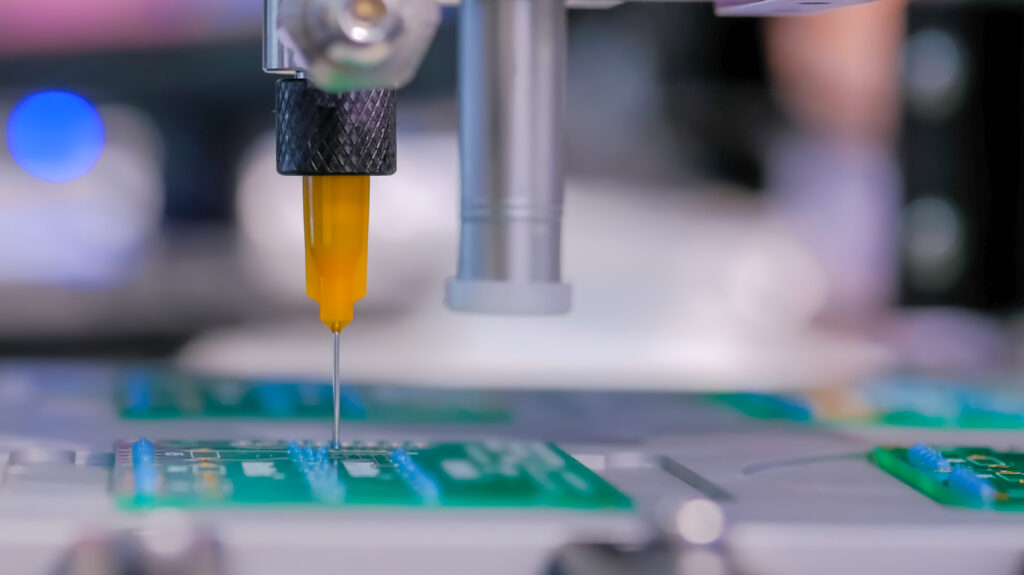
The type of liquid being dispensed is an important consideration when selecting a dispenser nozzle. There are two main categories: single-component liquids and two-component liquids.
・ Single-component liquids
These are divided into the following types, depending on the type of chemical reactions they undergo.
・ Solvent-volatile type: The solvent contained in the liquid evaporates and the remaining material hardens.
・ Water-volatile type: The water contained in the liquid evaporates and the remaining material hardens.
・ Water-reactive type: The liquid reacts with moisture in the atmosphere and hardens.
・ Thermosetting type: When heat is applied, a chemical reaction occurs in the liquid, causing the liquid to harden. The temperature of the heat applied varies, depending on the material.
・ UV curing type: The liquid hardens due to chemical reactions when exposed to UV light.
・ Anaerobic type: This has the unique characteristic of solidifying when contact with the atmosphere is blocked.
・ Two-component liquids
These are composed of a main agent and a hardener. When they are mixed together, a chemical reaction causes the liquid to harden.
Viscosity is another important consideration when selecting a dispenser nozzle. Viscosity is a measure of a liquid’s resistance to flow. The viscosity of liquids is roughly categorized as one of three levels: low, medium, or high viscosity. The higher the temperature of a liquid, the lower the viscosity tends to be. For manufacturing processes, large amounts of liquid must be dispensed quickly at high speeds. Selecting the correct nozzle is important to ensure accurate application with minimal losses due to splashing or flowing caused by high-speed and low-viscosity conditions.
Depending on the industry and the applications, custom nozzles may be necessary. When requesting a custom nozzle, it is important to specify the liquid that will be used, the details of the application, and the budget. Another important factor is the selection of a reputable manufacturer with the technology and experience to create a custom nozzle with the accuracy and stability required for the process.
Orbray’s dispenser nozzles
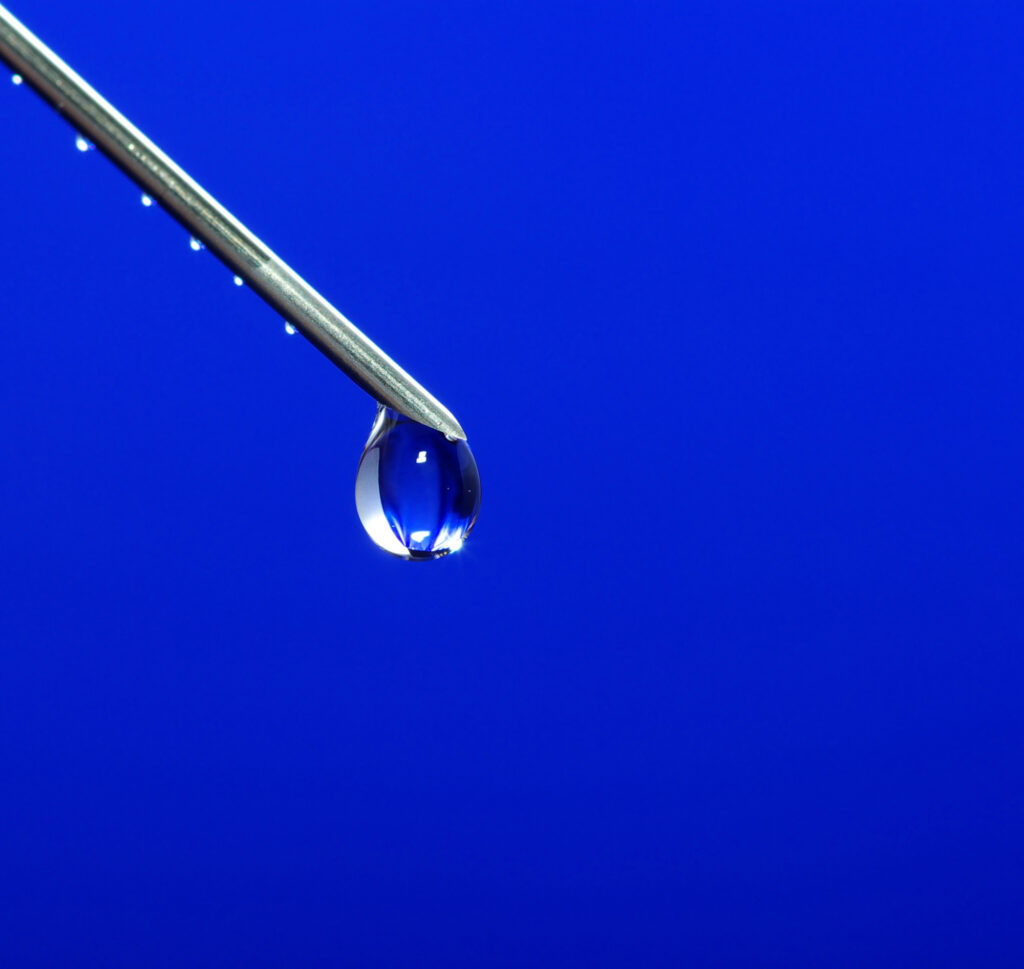
At Orbray, our deep knowledge of and experience with grinding and polishing techniques allow us to create very precise dispenser nozzles that provide accurate application results. We have incorporated many innovations to improve the fluid flow of our nozzles, thereby minimizing clogging or distortion of the nozzles, allowing highly accurate and consistent application. Even for applications in very small spaces, Orbray is able to produce nozzles that can be maneuvered as close to the application point as possible, allowing for highly accurate application.
Orbray can manufacture dispenser nozzles using various materials, such as 1) single-crystal ruby, 2) ceramic, 3) translucent ceramic, 4) carbide (tungsten), and 5) heat-resistant resin (Vespel®). With our expertise, Orbray can custom make nozzles using the most suitable material for the equipment and the liquid being applied.
Summary of dispenser nozzles
Dispensers are used in a wide variety of applications. They are essential tools for improving productivity, achieving consistent quality, and controlling costs. However, many factors – such as the type of nozzle, the application method, and the type and viscosity of the liquid being applied – must be considered carefully in order to select the most appropriate nozzle for the job.
Orbray can help you choose a dispenser and a dispenser nozzle that best fits your needs.
-
Introducing Bioceramics: Challenges, features, and applications
-
Ultra-Polishing of Sapphire along the c-Plane
-
Pioneering the Future of Multi-Core Optical Fiber Connections : Orbray's Optical Fiber Bundling and Light-Induced Self-Written Optical Waveguide Technology
-
What is a Ferrule? : The history and development of the ferrule continues today with its ever pursuit of high accuracy of 1um or less at reduced costs
-
What are Porous Ceramics and how are they different from regular ceramics?
-
Production of Sapphire