What is LiDAR? How it works, technologies, and applications
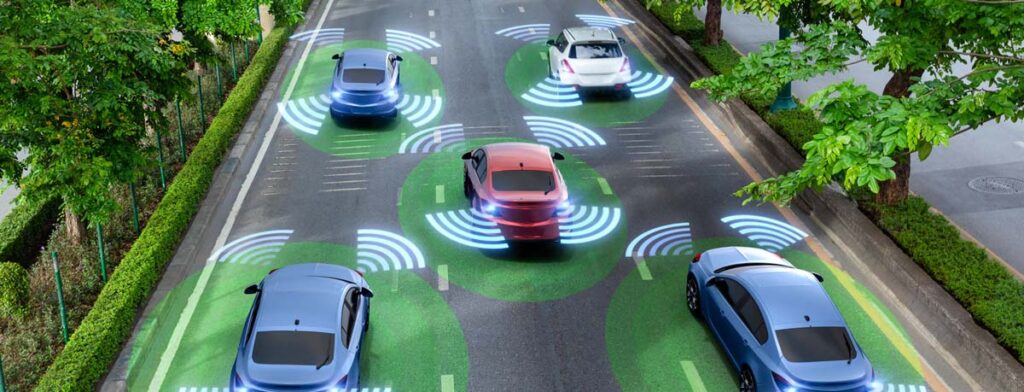
LiDAR is a technology that uses lasers to analyze the shape and distance of objects. It has long been used in meteorology and geology. In more recent years, this technology has been used in advanced driver assistance systems (ADAS) and automated guided vehicles, (AGV) as well as in robotics.
Table of contents [close]
LiDAR: Seeing by using laser light
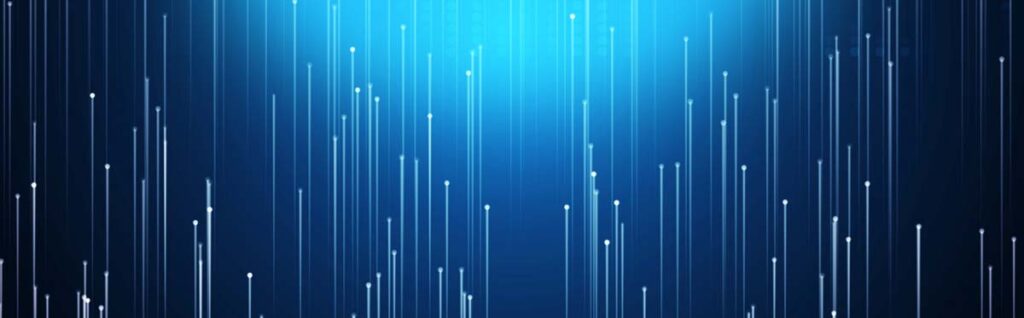
LiDAR is a modern light-sensing technology based on the advanced use of laser light. It is an acronym for “Light Detection and Ranging” or “Laser Imaging Detection and Ranging.” It is similar to radar (Radio Detection and Ranging), which works by sending out a pulse of radio waves and measuring the radio waves that get reflected back, helping it to ascertain and measure the position and distance of faraway objects. With LiDAR, the distance, direction, position, and shape of objects can be determined by measuring the time it takes for the laser light to be reflected and return to the source. While radar can only detect objects that easily reflect radio waves, such as metals, LiDAR can also detect nonmetallic objects.
Because LiDAR uses shorter wavelengths than radar, it is able to detect much smaller objects, such as cloud particles, and can measure distances and positions with much higher accuracy. Using these properties, LiDAR has been used in applications such as research on cloud movement, measurement of concentrations of atmospheric components, and measurement of tectonic deformation.
Miniaturization of LiDAR
LiDAR performs measurements by emitting and scanning for a wide range of laser light and measuring the time it takes for the light to be reflected and return to the source. The reflected laser light is detected as points by a sensor, allowing the simulation of a 3D image of the distance, position, shape, and surrounding conditions of the target object.

Dllu, CC BY-SA 4.0
https://creativecommons.org/licenses/by-sa/4.0,
via Wikimedia Commons
Conventionally, mechanical methods, such as motors, were used to point the laser light in different directions to cover a wide scanning area. One of the major issues with this mechanical method was the bulkiness and weight of the motor and laser combination, making it difficult to miniaturize the system. The moving parts were also susceptible to vibration and other mechanical interference. These drawbacks made LiDAR difficult to use in tight spaces and in places that could be subject to vibration and other stresses. For example, LiDAR units installed in vehicles for autonomous driving need to be compact, resistant to vibration, and durable. To achieve this, solid-state LiDAR, which eliminates the mechanical rotation mechanism and replaces it with semiconductor technology and optical technology, has been developed and is currently the mainstream for automotive use. The solid-state method has a narrower detection range, but can be easily miniaturized, giving it a high degree of flexibility in terms of installation location.
One of the solid-state technologies is MEMS (Micro Electromechanical Systems) LiDAR, which uses an electromagnetic mirror that is controlled using MEMS technology. Since the electromagnetic mirror is driven by magnetic force, it is resistant to vibration and can be pointed in different directions quickly and accurately. MEMS LiDAR comes in two main types: the raster scan type and the wobbling scan type. In the raster scan type, the laser is emitted in a horizontal pattern and is suitable for long distance measurement. In the wobble scan type, a mirror is used to scan the laser in a spiral pattern. The wobble scan type is best suited for short-range, wide-angle measurements.
Uses for LiDAR
LiDAR is used in a wide range of applications. For example, in meteorology and geology, LiDAR devices are installed in space satellites and aircraft, and emitted towards the Earth to make measurements. In recent years, compact and light-weight solid-state LiDAR devices have been mounted on drones to make low altitude measurements of surface features. This has been used to analyze roads and other infrastructure to measure changes in conditions and help make maintenance decisions. During natural disasters, similar LiDAR scans can quickly detect where landslides have occurred, aiding in planning rescue operations.
In more recent applications, LiDAR is used in ADAS, AGV, and robots to help detect people and other objects. Research related to the detection of obstacles in autonomous vehicle technology often focuses on systems that combine LiDAR with visual image recognition using cameras and millimeter-wave radar.
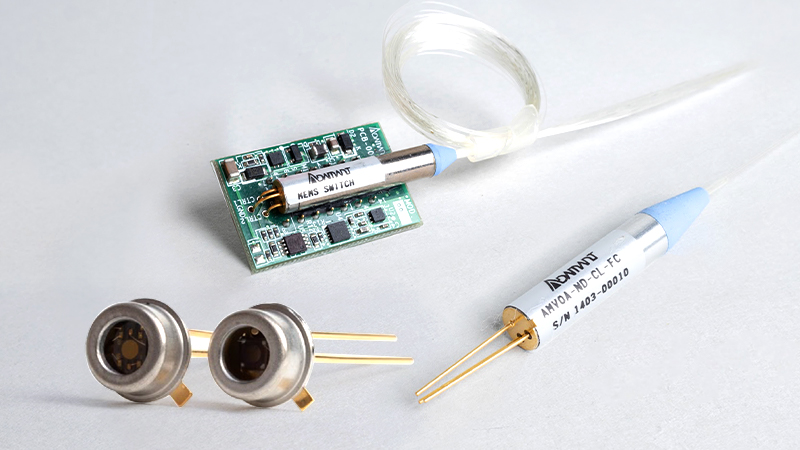
Similar to the human eye, image recognition using cameras is able to recognize obstacles. However, distances to the objects are difficult to determine by video images alone. Also like the human eye, image recognition using cameras is vulnerable to poor visibility during rain, in darkness, with back-lit objects, and in other poor conditions. Even a small amount of dirt on the lens can severely affect accuracy.
Millimeter-wave radar can pass through rain and fog and is therefore unaffected by weather and other poor visibility situations. However, directional accuracy is low. Radar is also not suitable for detecting objects with low reflectance to radio waves, such as trees or small objects.
LiDAR, which can measure position, distance, and 3D shape with high accuracy over a wide range, compensates for these shortcomings. By combining these three methods, it is possible to detect obstacles more accurately. Therefore, compact and lightweight LiDAR is a key component for ensuring the success of advanced autonomous driving technologies.
However, the current LiDAR technologies are very expensive. Cost reduction is an important issue for further adoption of the technology in the future. As one means of cost reduction, further utilization of MEMS optical device manufacturing technology, which enables mass production in a short period of time, is expected.
-
The Importance of Chip Mounter Nozzles
-
Precision Nozzles: Materials, Shapes, and Applications
-
Optical Mounting Technology ( Die bonding / Wire bonding)
-
Surface polishing technologies - Essential technologies for semiconductor, MEMS, and LED manufacturing
-
Novel Diamond Semiconductors Operate at Highest Power Ever
-
The Bright Future Being Created by Diamonds