The Importance of Chip Mounter Nozzles
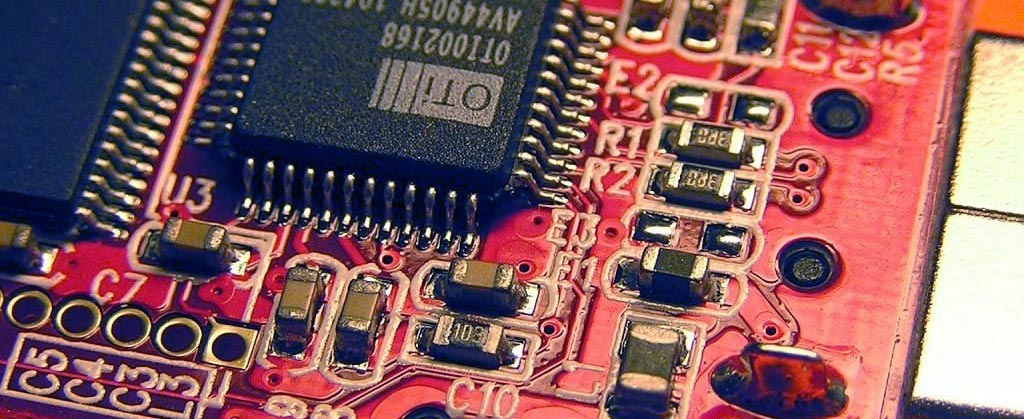
[Photo] Surface-mount components en:User:John Fader, CC BY-SA 3.0, via Wikimedia Commons
Many electronic components, or chips, are mounted onto the printed circuit boards that are used in almost all of today’s electronic devices. To be mounted, the chip must be positioned accurately onto the circuit board. During manufacture, machines called chip mounters are used to pick up and place such chips onto the printed circuit boards. Chip mounters that are able to securely pick up the tiny chips and quickly and accurately place them onto the circuit boards are indispensable for the mass production of consumer and other electronic devices.
Table of contents [close]
Chip mounters for surface mounting
Chip mounters, also called electronic component mounters, mainly use surface mount technology (SMT) to mount components onto circuit boards.
To manufacture printed circuit boards, first, solder cream or other adhesive is applied to the chip contact points using a dispenser or by an adhesive printing method. Next, the chip mounter picks up the chip and places it accurately in the required mounting position. Though the chips are now connected, the connection is not very strong and so, finally, heat is applied in a reflow oven to melt the solder cream or cure the adhesive bond to affix the components.
Chips have become extremely small in recent years. Some are just a few millimeters in size and manually mounting them onto circuit boards is exceedingly difficult. With a chip mounter, dozens or even hundreds of chips can be placed onto a circuit board quickly and accurately. Therefore, chip mounters play a vital role in the mass production of printed circuit boards.
Structure and operation of chip mounters
The main parts that make up chip mounters are: the head, which suctions and picks up the chips; the drive mechanism that moves the head into position; a chip feeder that supplies the required chips to the chip mounter; a position recognition system that can detect the precise locations of the chips; and the circuit board conveyance system.
The chips can be supplied to the chip mounter on reels of tape, or on trays. The feed system includes a reel feeder or tray feeder assembly. A drive unit equipped with an XY robotic arm moves the head into place for it to suction and pick up the parts, and then moves it to the required position for placement. Cameras with image recognition software or laser positioning systems are used to guide the head to the correct position for pick up and placement of the electronic components.
Chip mounters that use XY-axis robotic arms are also called modular mounters and are the most common type used today. Until recently, rotary mounters, which used rotaries with multiple heads arranged in a circle, were the norm. In this system, the chip supply unit moved into position to pick up the chips. After pickup, the rotary rotated, and the printed circuit board was moved into the correct position under the rotary for the component to be placed. Rotary mounters were able to pick up a large number of chips at one time and place them all very quickly. However, the machines were very large and complex, with limited versatility, and are therefore not in common use today.
Since modular mounters use an XY-axis robot arm to move the head sequentially for each electronic component, there is a limit to the production capacity. However, they are highly versatile and can easily manage low-volume production of highly variant products. In addition, high-speed mass production can be achieved with techniques such as using multiple heads and arranging multiple chip mounters in series.
Suction nozzles for high precision chip mounters
In order to support high-precision mass production of printed circuit boards, every component of the chip mounter must be high performance - for example, high-speed/high-accuracy image recognition cameras and XY robotic arms. And as electronic components continue to miniaturize, these performance requirements continue to increase.
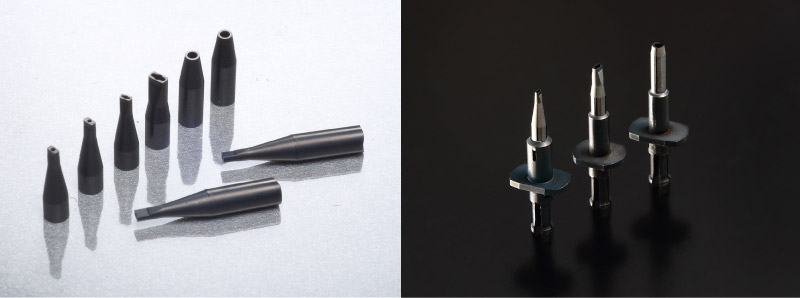
The increasing performance demands also apply to suction pick-up nozzles and pick-up collets, which must be able to handle a wide variety of shapes and sizes in order to support a wide variety of products. Since the pick-up nozzle and pick-up collet come into contact with electronic components thousands of times a day, it needs to be durable and have a long service life, with minimal wear and deformation. At the same time, the surface of pick-up nozzles and pick-up collets must be processed to a high degree of accuracy so that electronic components can be held securely and moved quickly into place. Materials with high wear resistance and durability are used for the precision nozzle tip, such as diamond, ruby, zirconia ceramics, hard metal, etc. These materials are difficult to process and require advanced techniques and know-how to properly handle high-precision processing of various shapes and sizes.
At Orbray, we use high quality black zirconia ceramics to produce pick-up nozzles and pick-up collets that are able to reduce diffuse reflection of light during the image recognition process. In addition, to accomodate ever-smaller products and components, Orbray pick-up nozzles and pick-up collets are capable of handling even the smallest 0201 (0.2 x 0.1) chips.
-
All About Lasers: How they work, their properties, and their uses
-
The Bright Future Being Created by Diamonds
-
100 times faster than 5G! What is possible with 6G?
-
Silicon Photonics: Why is it essential for 5G?
-
What are Audio isolation feet? Overview and Effects
-
First round of Space Delivery Project “RETURN to EARTH” The ceremony celebrating the return of the payload items was held