Summary of “Grinding” and “Polishing”A brief introduction to these processing technologies and how they are used.
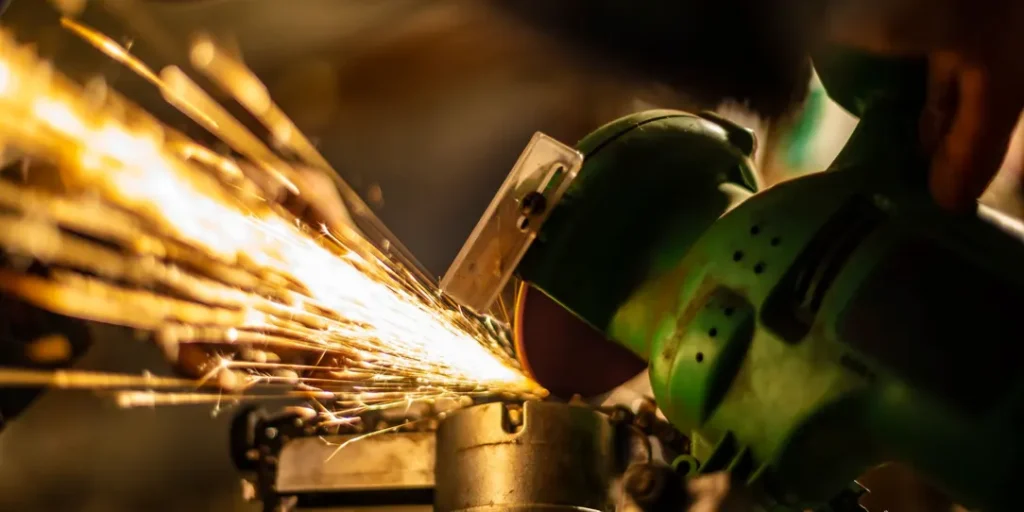
Grinding and polishing are processing techniques used in a wide range of fields and applications.
There are many different grinding and polishing methods. The correct method must be selected based on the application, and the required precision of the finished product. The main grinding and polishing methods are described below.
Table of contents [close]
Grinding and polishing
The terms “grinding” and “polishing” are often used interchangeably. Although definitions vary slightly from company to company, Orbray’s definitions are presented here.
Grinding
In the grinding process, abrasive grains are fixed to a tool (fixed abrasive grains) and used to scrape materials off of the surface of the product to obtain a desired shape.
Polishing
In the polishing process, abrasive grains are suspended evenly in a liquid medium (loose abrasive grains) and used to reduce the roughness of the surface of the product to achieve a mirror-like surface.
Grinding methods
Three major grinding methods are shown below.
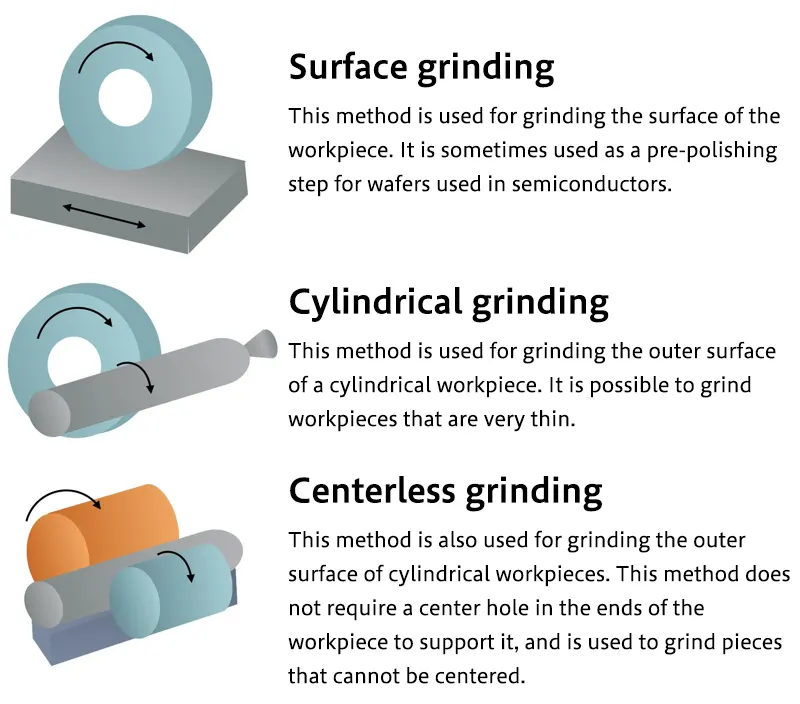
Polishing methods
Three major polishing methods are described below.
Lapping
Lapping is a rough polishing method. It uses a tool called a lapping surface plate and slurry containing abrasive material to create a flat and rough surface on the workpiece. Surface roughness (Ra) of micrometer order can be achieved.
Polishing
Also known as semipolishing, this process is similar to lapping except it uses softer tools and abrasive materials to create a smoother, flatter, mirror-like surface on the workpiece. Surface roughness (Ra) in the nanometer range can be achieved with this method. It is sometimes used in optical applications.
Chemical-mechanical polishing (CMP)
CMP is used for final polishing. It uses a fine balance of both mechanical polishing and chemical polishing to achieve surface roughness (Ra) of angstrom order.
Types of abrasive grains used in grinding and polishing
The abrasive grains used in grinding and polishing can be roughly divided into two categories: general abrasive grains and super-abrasive grains. Alumina and silicon carbide are examples of general abrasive grains, while diamond and cubic boron nitride (CBN) are examples of super-abrasive grains.
Diamond
Super-abrasive. Diamond is the hardest material found in nature. Diamond abrasive grains are able to process workpieces with high efficiency and accuracy.
Cubic boron nitride (CBN)
Super-abrasive. CBN is almost as hard as diamond. It has high thermal stability, so it can be used at very high temperatures. It is also ideal for processing steels that contain iron.
Silicon carbide (SiC)
General abrasive. SiC is mainly used to process difficult-to-cut materials and non-ferrous metals.
Alumina
General abrasive. Among the abrasive materials, alumina is relatively soft and inexpensive. It is commonly used for processing steel and soft materials. There are different types of alumina grains, such as A and WA types. The correct type must be selected depending on the workpiece and the desired results.
Applications and factors to consider for grinding and polishing
Fields and applications of grinding and polishing
Grinding and polishing are used in a wide range of fields and applications.
They play important roles in fields currently undergoing accelerated technological development, including Beyond 5G and 6G:
-Semiconductors
-Power semiconductors
-Dielectrics
-Industrial parts processing
-Optical equipment and precision equipment processing
-Jewelry processing
-Medicine
-Biomedicine
-Beyond 5G
-6G
Factors to consider when grinding and polishing
The following factors need to be taken into consideration when grinding and polishing.
-An accurate understanding of the characteristics of the workpiece, such as its crystal structure and orientation, is important.
-Heat generated by friction can damage the workpiece. Coolants and reduced tools speeds may be required.
-A smooth surface might not be achieved if shedding occurs.
-If high polishing accuracy is required, controlling the work environment is very important.
Orbray’s grinding and polishing technologies
Through our long history of manufacturing and processing sapphire products, Orbray has cultivated a wide breadth of processing and analysis technologies. This knowledge can also be applied to high-precision grinding and polishing of other single- and poly-crystalline materials.
Summary
This article introduced some methods and types of grinding and polishing processes, as well as some factors to consider. Whatever the material, shape, and processing accuracy desired, we have the optimum processing technology to meet your needs.
If you have any questions about what materials can be processed, our methods, or achievable polishing levels, please contact us. We will be glad to discuss the possibilities.
-
Precision Nozzles: Materials, Shapes, and Applications
-
Method for mass production of 2-inch diamond wafers developed - Expected to spur industrialization of power-semiconductor devices
-
Introduction to Power Semiconductors: From the basics to applications for each material
-
Cleavage of Jewel
-
The Importance of Chip Mounter Nozzles
-
Stylus in the Age of SP