Pioneering the Future of Multi-Core Optical Fiber Connections : Orbray's Optical Fiber Bundling and Light-Induced Self-Written Optical Waveguide Technology
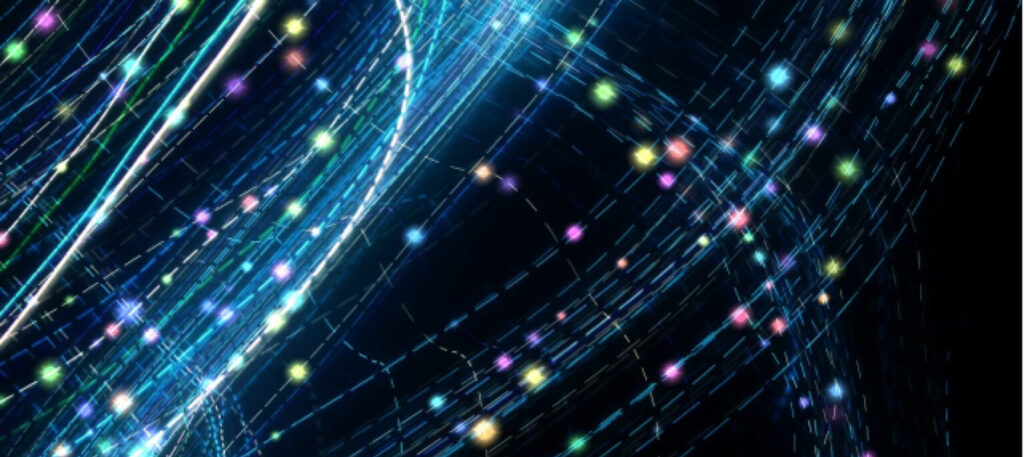
Table of contents [close]
Introduction
Due to recent technological developments, demand for Internet of Things (IoT) and information and communications technologies (ICT) continues to increase. Furthermore, demand for video communication services increased suddenly and significantly due to changes in people's work and lifestyles brought on by the global coronavirus pandemic. As a result, digital data is being generated, distributed, and stored like never before, and communications traffic is at an unprecedented high. With the ever-increasing communications volumes, existing information and communication systems are expected to reach their limits in both transmission and processing capacities in the near future1). Multi-core optical fiber (MCF) is a promising candidate to solve this issue. However, compared to general single-core optical fiber, MCF still has alignment challenges that need to be overcome for wide-spread adoption. This article describes Orbray’s efforts in developing effective MCF.
About Multi-core Optical Fiber
Multi-core optical fiber
MCF is a single strand of optical fiber that contains multiple cores that can each transmit separate light signals. Since different data signals can be sent through each core, large-capacity information communications becomes possible with a single optical fiber. This method of bundling and transmitting information through multiple paths, called space division multiplexing (SDM)2), is under development as a way to meet the high-volume requirements of next-generation long-distance and short-distance communications. MCF is showing promise as an effective method of achieving optical interconnects using SDM.
Challenges facing MCF connections
Conventional optical fiber has one core located through the center of the fiber. When connecting single-core optical fiber, the cores can be aligned highly accurately by precisely aligning the outer diameters of the fibers. In MCF, each core is offset from the center of the fiber. Therefore, when connecting MCF, aligning the outside diameter of the fiber does not guarantee that the cores inside the fiber will align appropriately, making precise connections more difficult. This is the major challenge of MCF. The cost of MCF alignment and connections is thus expected to be higher than for conventional connections. Technology to perform highly accurate alignment with high efficiency needs to be developed.
Connecting single-core and multi-core optical fiber (fan-in/fan-out devices)
To fully implement MCF technology, it is necessary to perfect not only the connections between MCFs but also the connections between MCFs and single-mode fibers (SMF). Optical devices cannot connect directly to MCF. Instead, SMF must be connected to each core of the MCF and then to each device. Fan-in/fan-out (FIFO) devices are used for this purpose. In a FIFO device, SMFs are bundled and arranged to match the pitch of the MCF and then connected to the MCF. The outer diameter of a typical SMF is 125 µm. Cores within MCF are often arranged several tens of µm apart. Therefore, simply bundling SMFs will not bring the cores into alignment with the MCF cores. The SMFs must be etched precisely so that they align accurately with the cores of the MCF. One important parameter for FIFO accuracy is the arrangement of the etched SMFs so that they align precisely with the cores of the MCF.
Fan-in/Fan-out Optical Fiber Bundles
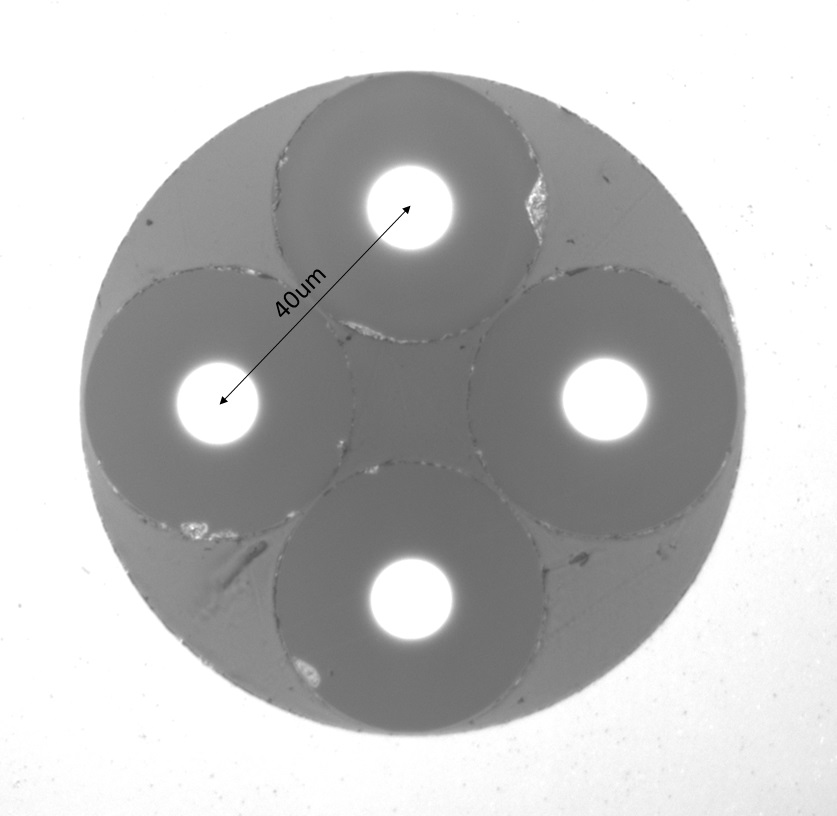
Orbray offers bundled optical fibers for FIFOs based on the zirconia ceramic ferrule manufacturing technology that we have cultivated for over 40 years. In addition, Orbray’s capability for precision processing of optical fibers is demonstrated by its lensed fiber processing technology (Figure 1). Orbray can precisely etch the SMFs to match the pitch of the MCF cores. This enables a precise connection using our custom ferrules, which have very accurate inner diameters and concentricity. The resulting bundle cores have alignment accuracy of±0.5um, both laterally and to the connecting cores. Our terminals are compatible with SC- and LC-type connectors for direct connections, and metal ferrules are available for spatial coupling.
Light-Induced Self-Written Optical Waveguide
What is light-induced self-written optical waveguide?
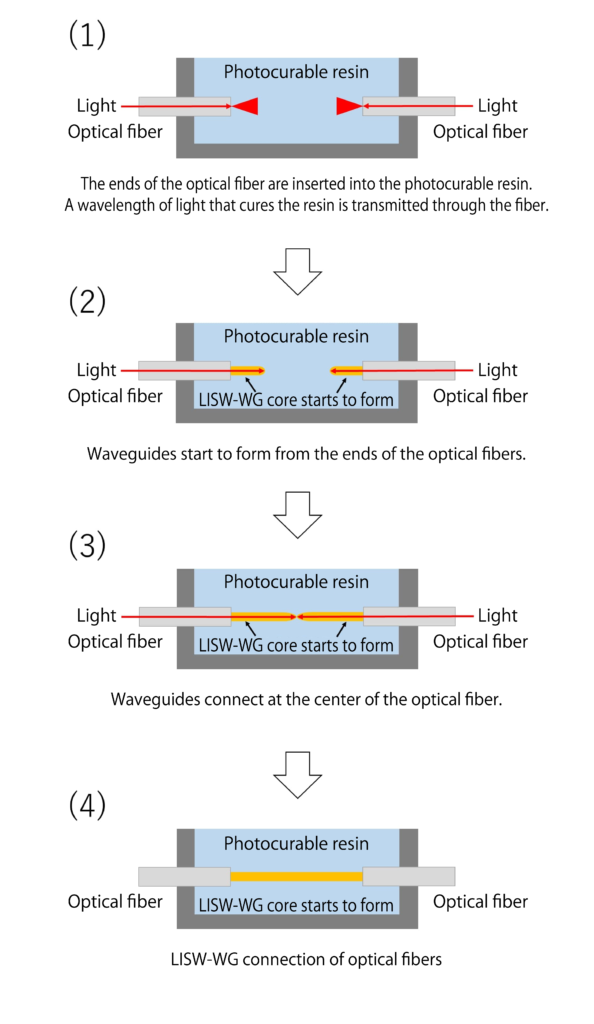
Light-induced self-written optical waveguide (LISW-WG) uses photocurable resin to create highly accurate connections between optical waveguides. In this process, light is emitted from an optical fiber into a photocurable resin; the resin hardens in the beam propagation direction, creating an optical waveguide. This LISW-WG core connection between optical fibers is performed using the process shown in Figure 2.
- (1)A pair of opposing optical fibers is placed in a photocurable resin, and both optical fibers are irradiated with light of a wavelength capable of curing the resin.
- (2)The resin cures sequentially from the core of the optical fiber due to the irradiated light.
- (3)The cured resin is connected where the output light beams of the opposing optical fibers overlap.
- (4)Stopping the light irradiation completes the polymerization reaction, and a core of LISW-WG is obtained.
The above process, also called the optical soldering phenomenon, enables connections between optical waveguides3). LISW-WG is expected to provide highly efficient optical connections between MCFs, under optical connection conditions where fusion splicing is difficult, and for connections between silicon optical waveguides and optical fibers.
Easing alignment tolerances and enabling batch connection of multiple channels
Making MCF connections using LISW-WG technology has two distinct advantages: Easing of fiber alignment tolerances, and enabling batch connection of multiple channels. Here, easing of alignment tolerances is described. In Figure 2, illustrating the LISW-WG connection process, steps (2) and (3) show that the growth of the LISW-WG core starts from the end face of the optical fiber, and opposing cores are created where the beams emitted from each side overlap. If the light beams emitted from opposing optical fibers overlap, the LISW-WGs that are facing each other will become connected to each other even if the fibers themselves are misaligned. This self-alignment process thus reduces the required alignment accuracy of the optical fibers.
Regarding batch connection of multiple channels, MCFs become more difficult to align mechanically as the number of cores increases. In contrast, by employing an optical system that can irradiate each MCF core, the cores can be aligned optically using LISW-WG, so alignment can be achieved regardless of the number of cores. LISW-WG connection is therefore a promising technology for solving the alignment challenges presented by the increasing number of cores.
Batch connection of 4-core MCF
The results of a 4-core MCF connection made using LISW-WG is described in this section. In this experiment, four cores were created in a fiber in a square configuration, arranged 50 µm apart. Pairs of MCFs were prepared and placed facing each other with a 100 µm space between them on a v-groove substrate. The gap was then filled with photocurable resin that was cured using near-infrared wavelengths4). A laser diode (LD) with a wavelength of 1310 nm was used as the light source to cure the core of the LISW-WG. The opposite end of the MCF was terminated with a FIFO, and the LD light was fanned out using an optical coupler that was connected to each channel of the 4-core MCF. Figure 3 shows a schematic diagram of the core fabrication system for the self-forming optical waveguides. By simultaneously emitting light from two LD light sources, 4-core MCFs can be connected all at once. The cores were irradiated for 10 seconds with a light intensity of 400 µW for each channel. Figure 4 shows a photograph of the LISW-WG core fabrication. Measurements confirmed that the core obtained using 1310 nm wavelength light was straight. The core fabrication time was 10 s, and simultaneous connection of the 4 cores in that short time was achieved. After creating the core of LISW-WG, the cladding was created by curing the resin around it.
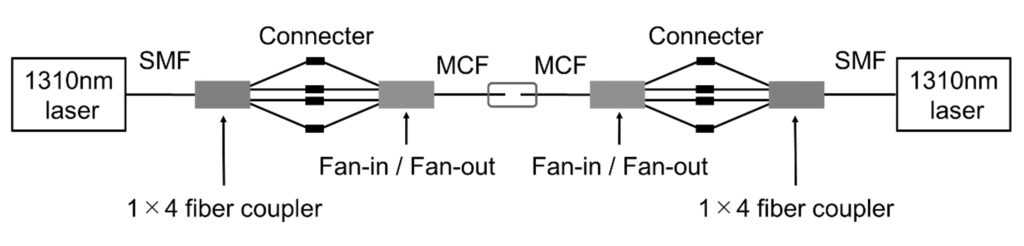
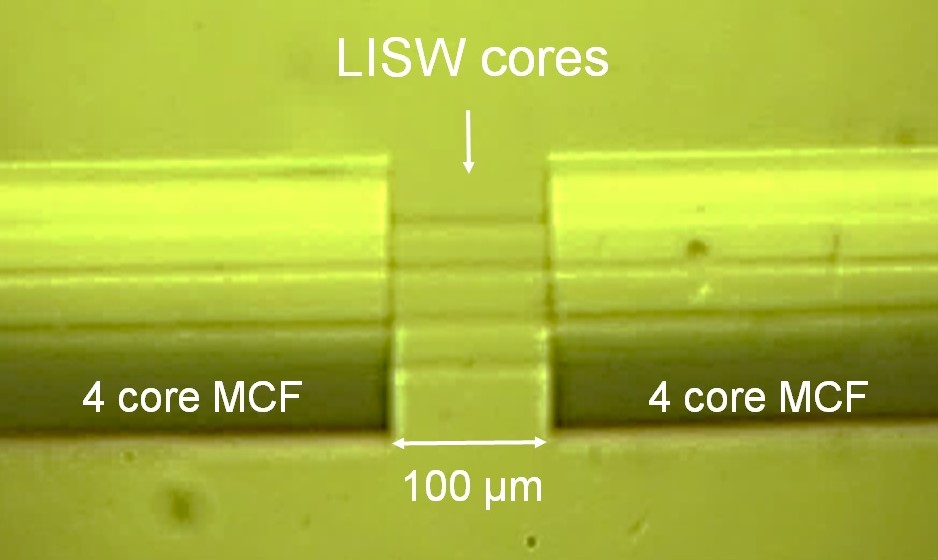
LISW-WG insertion loss measurements
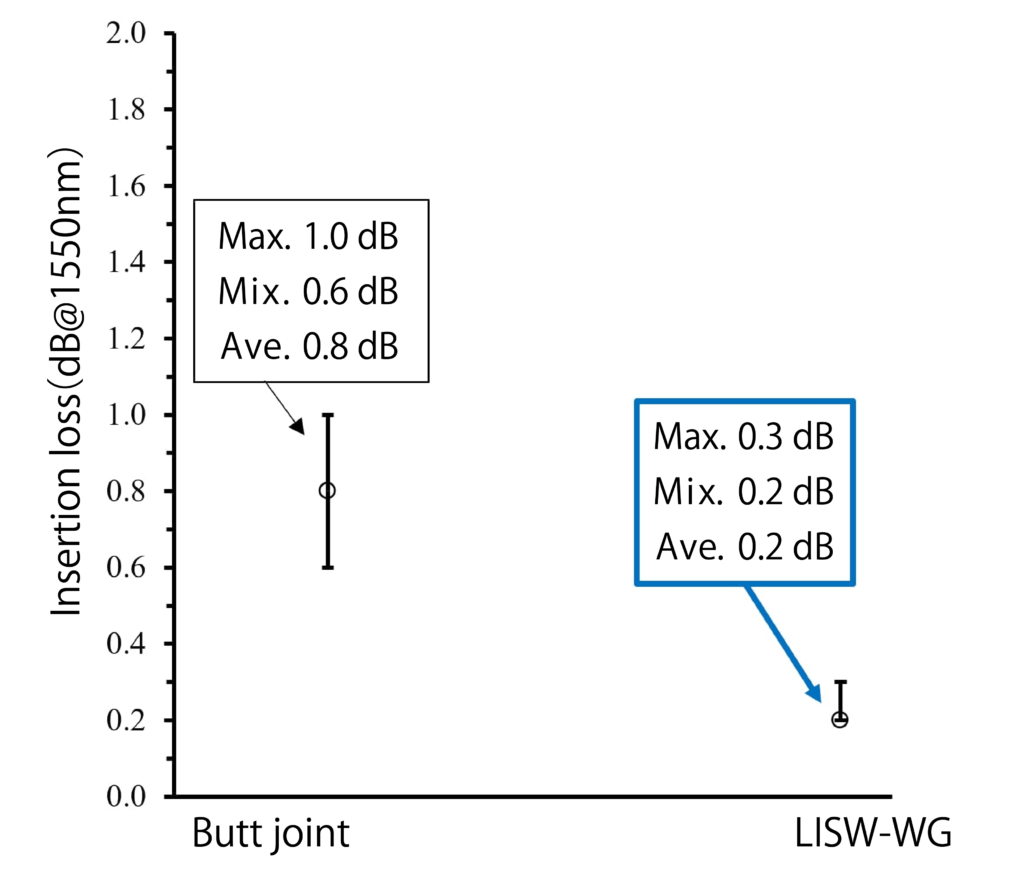
Insertion loss (IL) was measured for the MCFs that were brought together and aligned in the rotational axis to align the cores (butt joints) and for the MCFs that were connected with LISW-WG. 1550 nm wavelength light was used for the measurements. IL measurement was performed on each MCF channel. The results are shown in Figure 5. The average IL through the butt joints was 0.8 dB. The loss here came from misalignment between the MCFs. The average IL of the LISW-WG connections was 0.2 dB. Compared to the butt joints, the LISW connections had significantly lower loss. Variability in IL between channels was also examined. In the butt joints, the difference between the maximum loss and the minimum loss was 0.4 dB. In the LISW-WG connections, it was 0.1 dB, confirming an improvement in the variability of the connections. The reduction in loss and improvement in variability mean that the loss caused by the misalignment that occurred at the butt joints was improved by self-aligning and connecting the MCFs using LISW-WG. These results revealed that LISW-WG connections are an effective way to solve the increasingly difficult alignment problem for optical connections between MCFs and bundled optical fibers.
Conclusion
This paper explored Orbray’s bundled optical fibers for FIFO connections and LISW-WG as contributions towards practical use of MCF. Orbray can manufacture bundled fibers with an accuracy of ±0.5 µm from the ideal value by employing our zirconia ceramic ferrule manufacturing technology and optical fiber etching technology. Various custom ferrules can be selected to effectively utilize MCFs with differing core-to-core pitches. Orbray achieved a LISW-WG batch connection of 4-core MCFs with an average IL of 0.2 dB by using a photocurable resin that was cured with near-infrared light. The improvement in IL before and after achieving the LISW-WG connection confirmed that alignment tolerances can be eased from those currently required.
In addition to these technologies, Orbray is developing SC-type and LC-type optical connectors for MCF connections with the aim of developing optical connectors that can be used in the same way single-core optical fibers are currently used, and that can be handled in the same way as conventional products.
In the MCF optical communications field, where demand is expected to increase in the future, Orbray will continue to focus on connection technologies and develop products that meet customer needs.
Acknowledgement : The LISW-WG research results described in this article were obtained from the Beyond 5G R&D Promotion Project, research commissioned (03301) by Japan’s National Institute of Information and Communications Technology (NICT).
...................................................................................................................................................................................
References:
- White Paper on Information and Communications, 2020. Japanese Ministry of Internal Affairs and Communications.
- Y. Awaji, “Review of Space-Division Multiplexing Technologies in Optical Communications,” IEICE Trans. Commun., vol. E102-B, no. 1, pp. 1-16, 2019.
- T. Yamashita, M. Kagami, H. Ito, “Waveguide shape control and loss properties of light-induced self-written (LISW) optical waveguides,” J. Light. Technol., vol. 20, no. 8, pp. 1556–1562, 2002.
- H. Terasawa, O. Sugihara, “Near-Infrared Self-Written Optical Waveguides for Fiber-to-Chip Self-Coupling,” J. Light. Technol., vol. 39, no. 23, pp. 7472–7478, 2021.
-
“Physical Contact Push-Pull Technology for Fiber Optic Connectors” recognized as IEEE milestone. Promoting ferrules around the world through manufacturing.
-
MEMS technology: Backbone of smartphone and optical communications technology
-
High Flatness Polishing Processing
-
Silicon Photonics: Why is it essential for 5G?
-
What are ceramics? From industrial products to wristwatches, the many applications of ceramics
-
Dispenser Nozzles: Applications for dispensing liquids and selecting the right one