What are ceramics? From industrial products to wristwatches, the many applications of ceramics
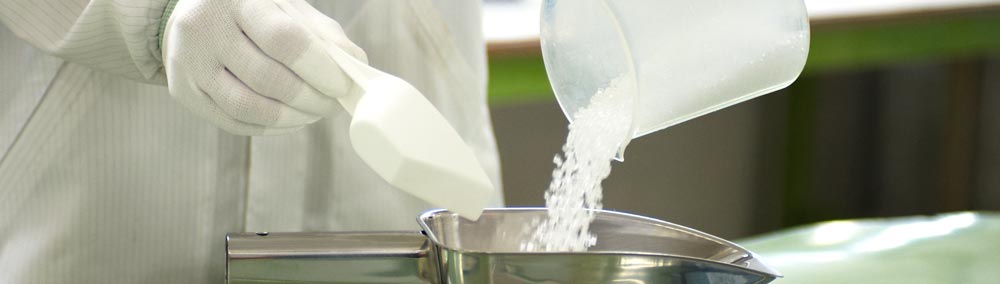
Ceramics are made by blending inorganic, nonferrous materials, molding them, and then firing them at high temperatures in a kiln. Ceramics have high chemical stability, heat and corrosion resistance, and electrical insulating properties. They are used in a wide range of applications from cooking utensils, watches, and jewelry, to parts for electrical equipment and medical products.
Table of contents [close]
High hardness, corrosion resistance, and heat resistance
The word “ceramic” comes from the ancient Greek “keramos” which means potter’s clay. All manner of pots and clay containers are examples of ceramics. However, modern ceramics are not just clay containers baked in an oven. For today’s sophisticated ceramics, a wide range of advanced additives, such as refined zirconia or alumina powders, are added to the mix before molding and firing to obtain the specific characteristics needed for each application. Such ceramics are known as “fine ceramics.”
Ceramics are recognized for their high density and hardness; corrosion, heat, and friction resistance; and great electrical insulating properties. Ceramics are almost as hard as diamonds and more rigid than tungsten, one of the most rigid metals on Earth. Ceramics are highly resistant to plastic deformation and resistant to friction, and they have a very low coefficient of thermal expansion. Their melting point is higher than that of many metals, and they are not only resistant to oxidation and rust, but are also very chemically stable.
Ceramics also have some disadvantages. Although they are very hard and resistant to scratches, they are brittle and thus prone to fractures and chipping. Moreover, due to their hardness, mechanical processing after firing is very difficult. Also, although they are heat resistant, they are susceptible to sudden changes in temperature, and can fracture if the thermal shock is great enough.
Several factors contribute to the ceramic materials’ high resistance to heat. Ceramics have a crystalline structure in which atoms and molecules are organized in a regular pattern, creating exceptionally strong bonds. This regular arrangement enhances thermal stability. Additionally, ceramic materials typically consist of fine grains, which can maintain stability at elevated temperatures. These characteristics enable ceramic materials to retain their structural integrity even when exposed to high heat.
Production methods
Ceramics are made by mixing the materials, molding, and firing. In the mixing step, raw materials such as zirconia, alumina, or reinforced alumina are kneaded together, along with binders and additives such as firing aids and strengthening agents, depending on the application. Binders are made of plastics and are vaporized during the firing process.
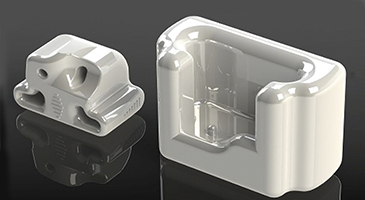
In the molding step, the prepared materials are formed into the required shape using a mold. Ceramics shrink during firing, so this shrinkage must be taken into account during the molding process. Molding is done by injection, extrusion, press, or CIP (cold isostatic pressing), depending on the final application and required performance of the ceramic. When press molding is used, the amount of binder used is typically small, and any excess material can simply be cut off after molding.
After molding, the ceramics are fired in a furnace. Electronic furnaces are often used to allow precise temperature control. After the ceramics are fired, cutting, polishing, surface grinding, and other secondary finishing processes are applied. Finally, the ceramics are inspected and cleaned to become the final product.
Since ceramics are molded, it is possible to mass-produce products with complex shapes, which are difficult to achieve with metals, while maintaining hardness and other properties. Ceramics have performance characteristics that often exceed those of comparable metals, while being lighter than most metals.
Materials used in ceramics
Alumina, zirconia, reinforced alumina (alumina with zirconia additives), silicon nitride (SiN), silicon carbide (SiC), and aluminum nitride (AlN) are some of the materials used in the manufacture of ceramics.
Alumina is the most commonly used material for the production of ceramics. It has high hardness and high heat, corrosion, and friction resistance.
Zirconia produces the hardest ceramics. Toughness is the capacity of a material to deform under an external force or load before fracturing. Toughness is the measure of energy of the mechanical deformation per unit volume prior to fracture and does not imply the returning of the material’s original form. This is an indicator of the material's durability and flexibility, which can undergo temporary deformation without breaking. Materials with high toughness are capable of withstanding substantial forces and impacts. Orbray’s zirconia ceramic ferrules used primarily in optical communication components are products that benefit from this critical property.
Reinforced alumina ceramics are made by adding zirconia to a high-purity alumina base. Beneficial properties of both ceramics are combined, creating ceramics with the high hardness of zirconia while keeping the characteristics of alumina ceramics. Silicon nitride ceramics have high hardness at high temperatures. They have high fracture resistance and are also very resistant to friction. SiN ceramics are very hard and rigid, and resistant to corrosion, even at high temperatures. They have high thermal conductivity but low electrical conductivity.
Ceramic watches are catching on
Since ceramics are harder than many metals and have many other favorable characteristics, they are being used in more and more industrial applications. Such applications include industrial uses such as tools for cutting, grinding, and polishing, and shaft bearings; IC applications such as electronic parts; optical communications applications such as ferrules and sleeves; and medical applications such as dentures and medical devices.
In addition to industrial uses, ceramics are being used to make parts for wristwatches, as well as fashion accessories and jewelry. Regarding use in wristwatches, ceramics have been used to make casings and bezels starting in the late 1980s. More watchmakers have been incorporating ceramics into their products starting in the 2000s. Some watchmakers even offer watches made entirely out of ceramics.
Conventionally, watches have been made of either stainless steel or tungsten carbide. Currently, watches made of zirconia fine ceramics are increasing in popularity. Foreign luxury fashion brands have offered zirconia cases and bands for their watches for many years. White zirconia is especially valued in luxury products, since it looks similar to pearl, distinguishing it from other brands.
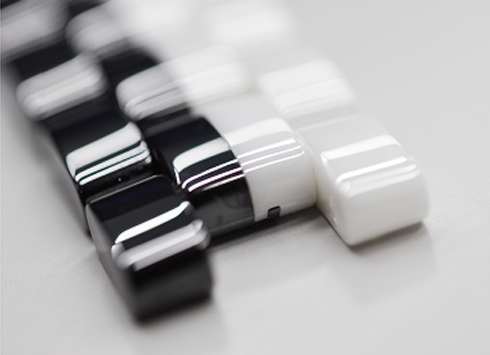
Ceramics are extremely hard and scratch-resistant, and they shine like jewels when polished. This makes them an ideal material for use in exterior parts of everyday products such as wristwatches. In addition, because they are resistant to oxidation and corrosion, ceramics do not rust or discolor. Also unlike some metals, they do not cause allergic reactions on contact with skin, and they feel much smoother than metal. Ceramics undergo no deterioration due to ultraviolet rays caused by long-term exposure to sunlight, and the effect of heat is extremely small, so ceramic parts are also useful for watches used in extreme environments. These characteristics mean that ceramic watches shine like new and continue to work well, even after many years of rugged use. Since ceramics are lighter than stainless steel, they can be used for lightweight models that maintain high strength.
One downside is ceramic’s tendency to chip and shatter. Therefore, it is necessary to carefully design the watch so that bending or twisting forces do not concentrate on a single point, such as the connection between the watch case and the wrist band. In addition, due to their hardness, processing of the ceramic parts can be a challenge, requiring advanced polishing and machining technologies.
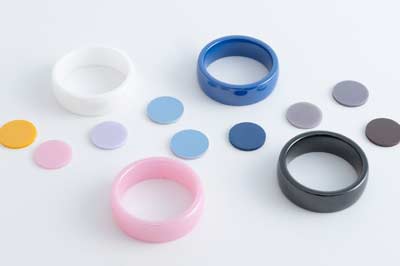
Until recently, most ceramic watches were black or white. However, new colored zirconia such as blue and red have been developed, and the choices continue to increase. Processing techniques have also improved. Through special polishing and machining techniques, a more beautiful luster can now be achieved. Matte finishes or partial hairline finishes are also possible. The design of the watch itself is also improving.
Orbray is a World leader producer of components and products in fine ceramic.
In our company, zirconia, alumina and zirconia-toughened alumina powder is prepared according to the product, and then cast and sintereds.
-
Introducing Bioceramics: Challenges, features, and applications
-
The advantages and characteristics of ceramic watches
-
What are Porous Ceramics and how are they different from regular ceramics?
-
All About Lasers: How they work, their properties, and their uses
-
Introduction to winding nozzles: an essential component of the motor coil winding process
-
Pioneering the Future of Multi-Core Optical Fiber Connections : Orbray's Optical Fiber Bundling and Light-Induced Self-Written Optical Waveguide Technology