フェルールとは ~高精度・低損失のフェルール製造を追求し続ける開発の歴史~
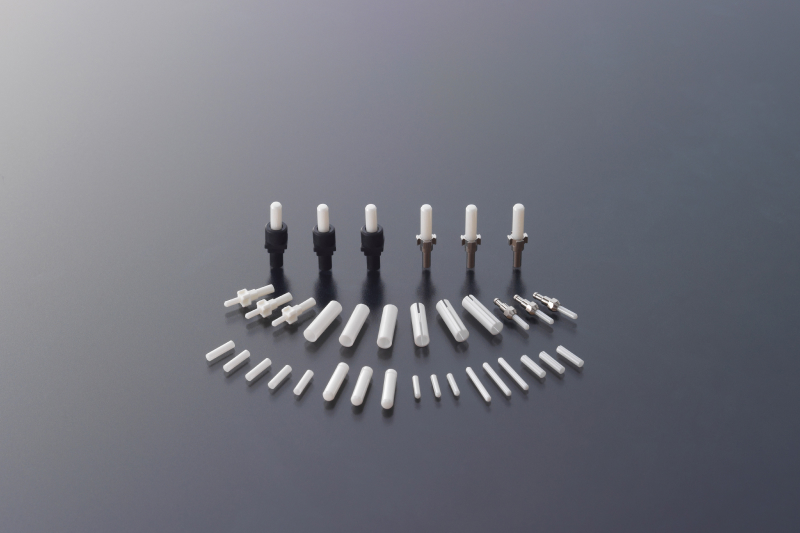
フェルールは、光通信を支える部品として広く世界で使用されています。Orbrayは、光通信がまだ開発途上であった、1980年からフェルールの製造を開始しました。生産技術の改善による高精度化やコスト削減対応など、多くの課題をオーダーメイドの技術対応と匠の技で解決してきました。Orbrayのフェルールは、今も世界で高いシェアを維持しています。
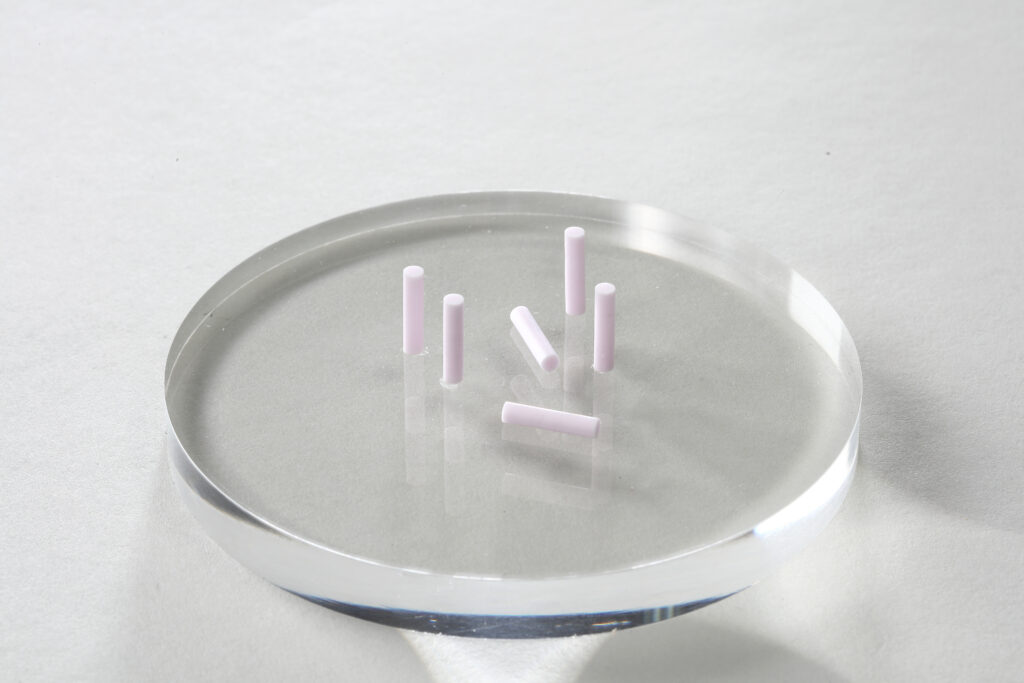
目次 [閉じる]
時計用軸受宝石の加工技術から生まれた光通信用部品
光通信は、1970年に実用化レベルの光ファイバー製造技術が米国で開発され、普及に向けた研究が本格化します。研究が進むなかで、光ファイバーを簡単に接続し、つなぎ変えができるようにする、コネクターが必要になりました。その際に用いられたのが、円柱状の外径を持ち、中心に光ファイバーを通す穴が正確に開けられたフェルールです。
光ファイバーは直径が百数十μmと非常に細く、光が通るコア部分の径は、10~数十μmと非常に小さなものです。光コネクターでは、接続時の光の損失を防ぐため、1μm以下の精度でファイバー端面を突き合わせて接続しなければなりません。フェルールには、穴のサイズや同心度、外径の円筒度などに厳しい精度が要求されます。光通信の研究を進めていた通信、電気などの研究開発機関や企業は、基準を満たす精度のフェルールを作ることが課題となっていました。
Orbrayは、1939年に人工サファイアを使った電気計測器用軸受宝石の製造で創業しました。その後時計用ルビー軸受宝石、ダイヤモンドレコード針の製造などにも着手します。創業時から、非常に硬い素材を精密に加工することを得意としていました。70年代後半、この時計用軸受宝石の加工技術を使って、フェルールの製造ができないか相談を受けます。開発に着手し、加工機、検査機、加工方法に工夫を重ね、精度を高めることを繰り返します。そして、試行錯誤の結果、1980年には、要求精度を満たすことができる、押出成形によるアルミナフェルールの製造を開始することとなります。
高精度かつ、より低コストで大量生産
日本国内では、80年代中頃に基幹となる光ファイバーケーブル網が整備され、光通信の普及が進みます。普及が進むにつれ、伝送容量が大きくなり、より接続時の損失が少ない光コネクターが求められるようになります。それまでの光コネクターでは、フェルールの端面は平面に研磨されていました。そのため、コネクターで接続した光ファイバー端面の間に、隙間が発生することがありました。隙間による、反射の戻り光を抑制するためには、コネクター接続時に端面へ屈折率整合剤を塗布する必要があります。これを無くし、より反射や損失の少ない接続方法として、フェルール端面を凸球面状に研磨して、頂点どうしを押し当てることで光ファイバーを接続する、PC(Physical Contact)接続が開発されます。
しかし、PC接続を行う際、アルミナセラミックスのフェルールでは問題が発生しました。靭性が低く、押し当てた際に光ファイバーを通す穴の縁が欠けることがあったのです。これに対応するため、フェルールの素材はアルミナセラミックスから、より靭性の高いジルコニアセラミックスに変わっていきます。そして、Orbrayでは、加工機、加工方法の更なる改善、改良を重ね、1987年に押出成形によるジルコニアフェルール製造を開始しました。
しかし、この頃からまた新たな課題が出てきます。需要の増加と共に、顧客からの価格に対する要求が高まってきたのです。精度を落とすことなく、より低コストで、大量にフェルールを作ることが求められるようになりました。
顧客の要望に応えるための新たな挑戦
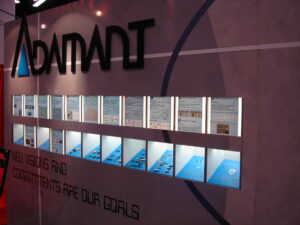
セラミックスの押出成形によるフェルールの製造では、原料となるセラミックパウダーとバインダーを混合した後、押出用金型から押し出すことで、長い1本の成形体を作ります。これを適切な長さに切って焼成後、内径加工や外径加工、穴の入り口のV字テーパー加工、端面加工を行い、フェルールへ加工していきます。
しかし、当時の押出成形では歩留まりが悪く、押し出した際の素材精度にもバラツキが出やすいという問題がありました。要求サイズとするには、大きめに押出成形した素材を、研磨等で目標寸法まで加工する必要があります。そのため、工数が増えてコストがかかっていました。また、V字テーパー加工を焼成後にドリルを押し当てて行うので、テーパー面が荒くなりやすく、光ファイバー挿入時に傷をつけてしまう懸念がありました。
これらの問題を解決する方法として、Orbrayでは、射出成形によるジルコニアセラミックスの製造に挑むことを決めます。射出成形によるフェルールの製造は、コスト的にも、精度的にも不利というのが当時の常識でした。コンパウンドのロスが出やすく、中心に内径となる細長いコアピンを立てた射出成形用金型へ、コンパウンドをムラなく均一に流し込むことは、高い技術が必要になります。しかし、射出成形ならば、V字テーパーの加工にドリルを使うこともなく、完成形状に近い形を作れるので、素材精度を上げることができれば工数を大幅に減らせます。大きなコスト削減となるのです。
技術と経験を活かし、フェルール製造の更なる改善を目指す
射出成形によるジルコニアフェルールの製造を検討する前年。Orbrayでは、別製品において、顧客の要望する形状に対応するため、特殊形状の射出成形の製品製造に着手していました。このオーダーメイドの技術をフェルールの製造に適用できないか検討を開始します。こうして1989年、射出成形によるジルコニアフェルールの製造が開始されます。射出成形技術もさらに向上させることで素材精度も上がり、工数の大幅削減も実現することができました。
そして、1990年代に入り、フェルールの製造数は更に増大していきます。1995年頃よりITバブルの影響で生産数が増大。これに対応するため、射出成形によりできた脆い成形体をつかめるように社内で改良を行ったロボットを、射出成形工程に導入。さらなる製造の省力化、コスト削減を進めていきました。加工機の改善による歩留まりの向上も同時に進めていきます。
1993年には、ジルコニアコンパウンドの内製化を実施。1999年には、射出成形金型の消耗品となる、コアピンの内製化を行うことで、コスト削減を推し進めていきます。また、フェルールはシングルモード用とマルチモード用があり、当時海外ではマルチモードの需要が多くありました。当時のマルチモード用フェルールはシングルモード用の規格外品が当てられることが多く、安定供給に問題がありました。これに対し、素材、製造方法を改善してマルチモード対応を行い、マルチモード用フェルールの生産性をアップさせます。2000年代に入り、フェルールの需要が落ち着いてからは、さらなる素材精度アップを行い、加工合理化を図っています。
Orbrayのフェルールは、常に顧客の要望に耳を傾け、オーダーメイドの技術対応と匠の技で対応してまいりました。通信関係に限らず、光ファイバーは様々な分野で使用され、フェルール コネクタも多種多様なものが使用されています。 今後も技術と経験を活かし、通信規格に準拠する製品、精度の厳しい低損失品、カスタム品まで各種製品を強化していきます。

Orbrayではシングルモードフェルール、マルチモードフェルール、ローロスフェルール、フェルール コネクタなど、各種ファイバ、デバイスごとに最適な高品質のフェルールを提供しています。
お問い合わせは下記フォームに入力し、確認ボタンを押して下さい。
※お問い合わせフォームからのセールス等はお断りいたします。送信いただいても対応いたしかねます。