The technology to make a hole 0.01mm or smaller in synthetic jewels – how is this useful?
Orbray's Future, Vol. 4
On January 1, 2023, we changed the name of our company,
Adamant Namiki Precision Jewel Co., Ltd., to Orbray Co., Ltd.
Precision jewel. We added these words to our company name in 1953. At the time, we specialized in making precision parts out of industrial jewels for use in electric meters and luxury watches. Today, we are the world’s leader in the manufacture of precision components for a wide range of electronic, optical communications, and medical devices around the globe. We are proud to continue to demonstrate the meaning of “precision jewel” through our technologies and products.
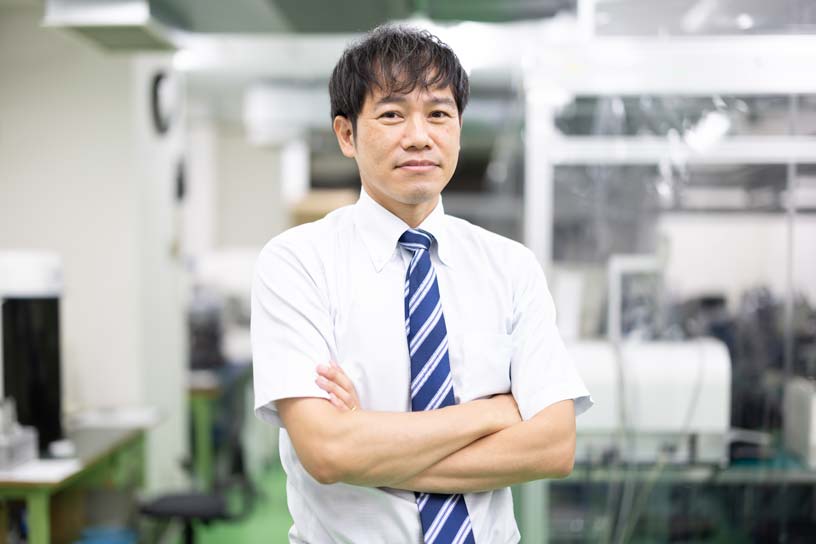
Industrial jewels are used in a variety of applications, from watch bearings to the medical field
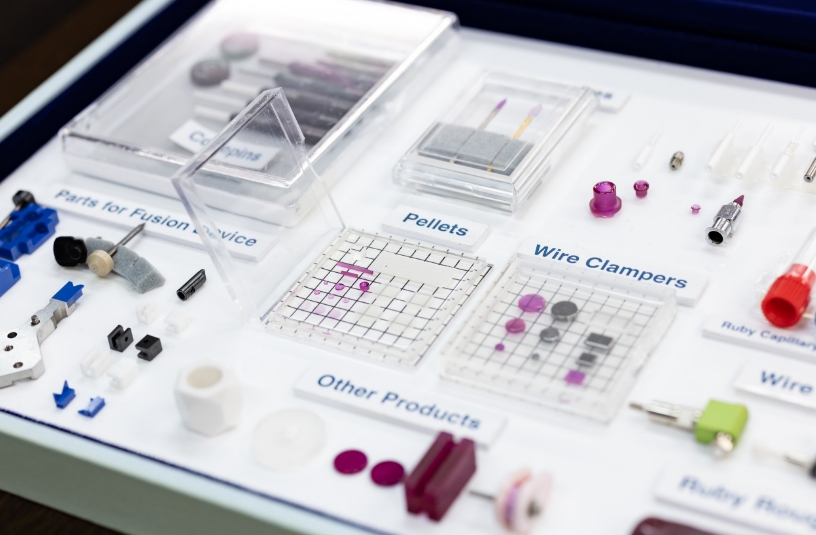
Our founder, Kazu Namiki, acquired the technology for processing gemstones and founded Namiki Seisakusho (Namiki Manufacturing) in 1939. Since then, we have capitalized on our three core technologies of “cutting, grinding, and polishing” to manufacture components that play important roles in our daily lives out of difficult-to-process materials, like jewels and ceramics. We are one of very few companies in the world that are able to produce synthetic diamond and sapphire materials, and have a high capacity for processing these materials.
Jewels and crystals found in nature are rare and expensive. Before synthetic production of sapphire was developed about 100 years ago, such materials could only be used in a limited number of fields, such as in luxury watch bearings. With advances in crystal growth technologies, the cost of synthetic diamond, sapphire, and ruby crystals has decreased dramatically, such that these materials are finding many uses in everyday applications.
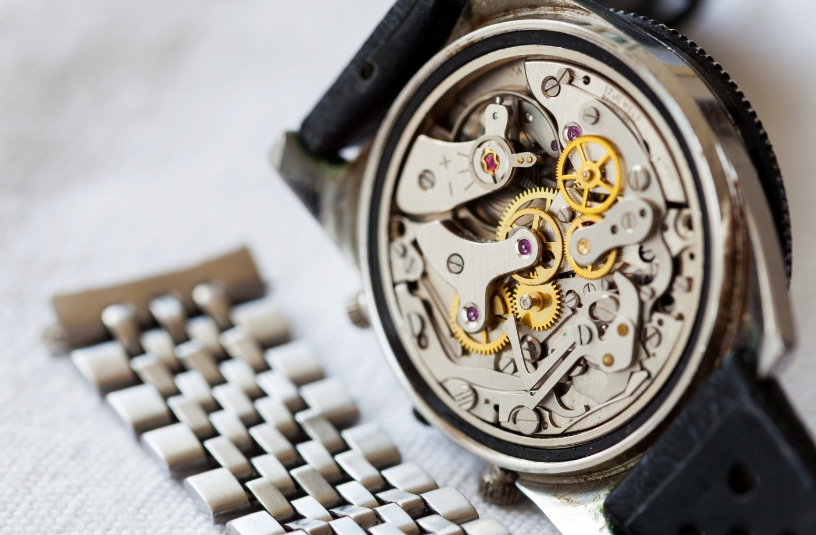
Jewels are harder and more resistant to chemicals and temperature extremes than metals, and have been used since antiquity. Their use continues to expand, with new applications in medical, semiconductor, and other advanced fields. Clients pursuing the cutting-edge have always relied on us to create products that are ahead of their time. We have continued to meet their needs by developing state-of-the-art products.
Technology to drill holes in the hardest materials
There is a curious paradox. If diamonds are the hardest material on Earth, what can be used to cut, grind, and polish them? The answer is diamonds themselves. Tools that contain tiny grains of diamond are used to cut, grind, and polish larger pieces of diamond. The size of the grains and the particular processing methods are carefully selected to achieve the desired results. Laser processing using the power of light to cut diamonds has also become popular in recent years.
In this article, we will introduce technology for drilling very precise holes in hard, difficult to process materials. Recently, there has been new demand for precision holes for life science research, such as for microflow path instruments used in pharmaceutical research and devices for observing individual cell membranes.
It is very difficult to make deep, thin holes in cemented carbide, zirconia, monocrystalline rubies, and other hard materials. To meet clients’ exact needs and be cost effective, the drilling technology must have high precision and fast through-put. By combining the diamond microdrills we have developed with heat-resistant lasers called femtosecond lasers, we have pioneered a technology that drills nanometer diameter holes with accuracy, speed, and reliability.
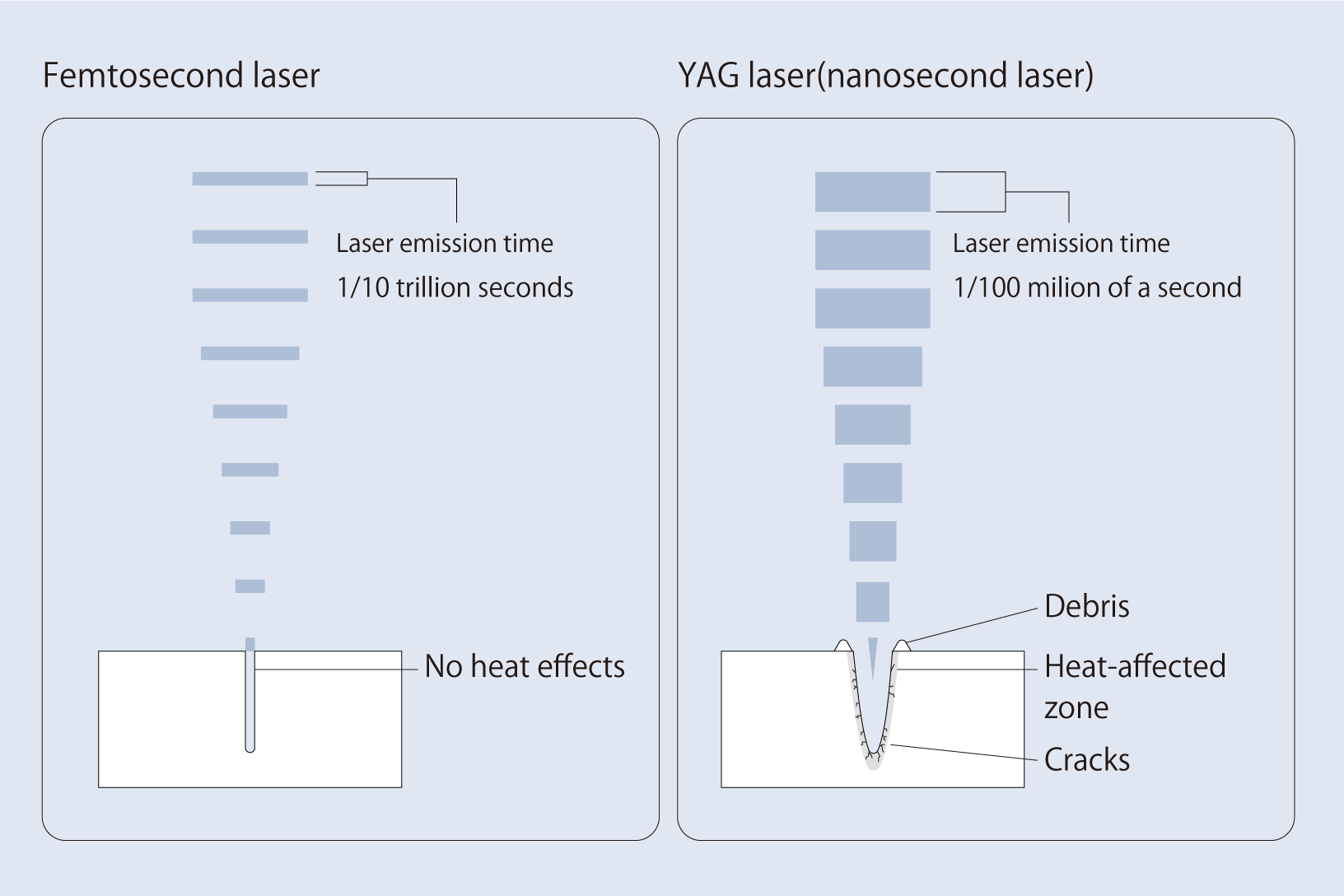
Our diamond microdrills were developed based on our knowledge and experience with manufacturing diamond phonograph styli. We are able to create 0.1 mm diameter holes with an aspect ratio of >60 (aspect ratio = hole depth / hole diameter). The thinner the drill, the weaker it is, and the more susceptible it is to vibration of the equipment. This must be compensated for by modifying the drill chucks and tooling. Drill speed and processing time also need to be selected carefully. With so many variables that must be precisely controlled, drilling such iny holes truly a true feat of craftsmanship.
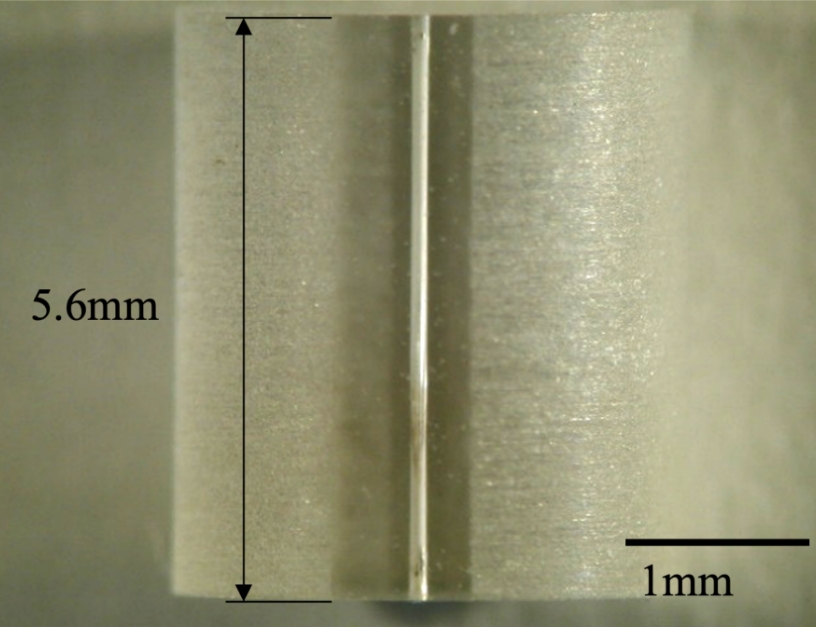
Our diamond microdrills are also capable of polishing the inside of the holes without the need for a separate polishing step. Since we manufacture the drills and use them to process diamond materials, we are very familiar with every characteristic of the drills, the drilling equipment, and the substrate materials. This allows us to produce components to the exact requirements of our customers.
Adamant Namiki also excels at drilling holes in curved surfaces, such as grooves, tubes, bottles, and thick materials. For holes in curved surfaces, we are able to precisely align the laser with the material to be processed, using a CCD monitor. For thick materials, Adamant Namiki’s femtosecond laser micromachining system uses a microdrill to start a hole with a larger diameter than the target diameter. The drill is stopped just before the hole is completed, and a femtosecond laser is used to finish the hole with the desired diameter. Although many manufacturers struggle with this multi-step process, Adamant Namiki can reliably create such holes using its proprietary high-value-added technology.
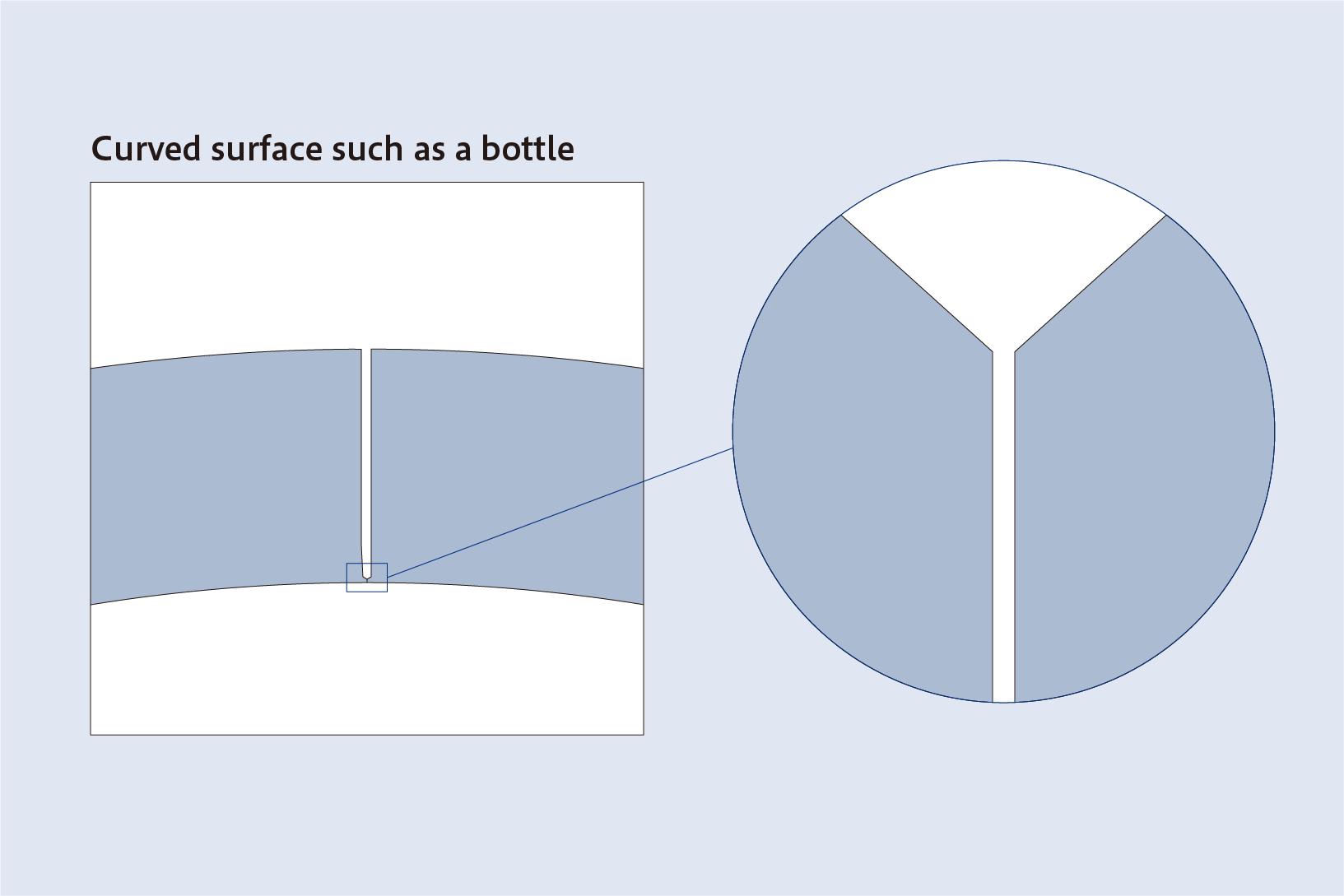
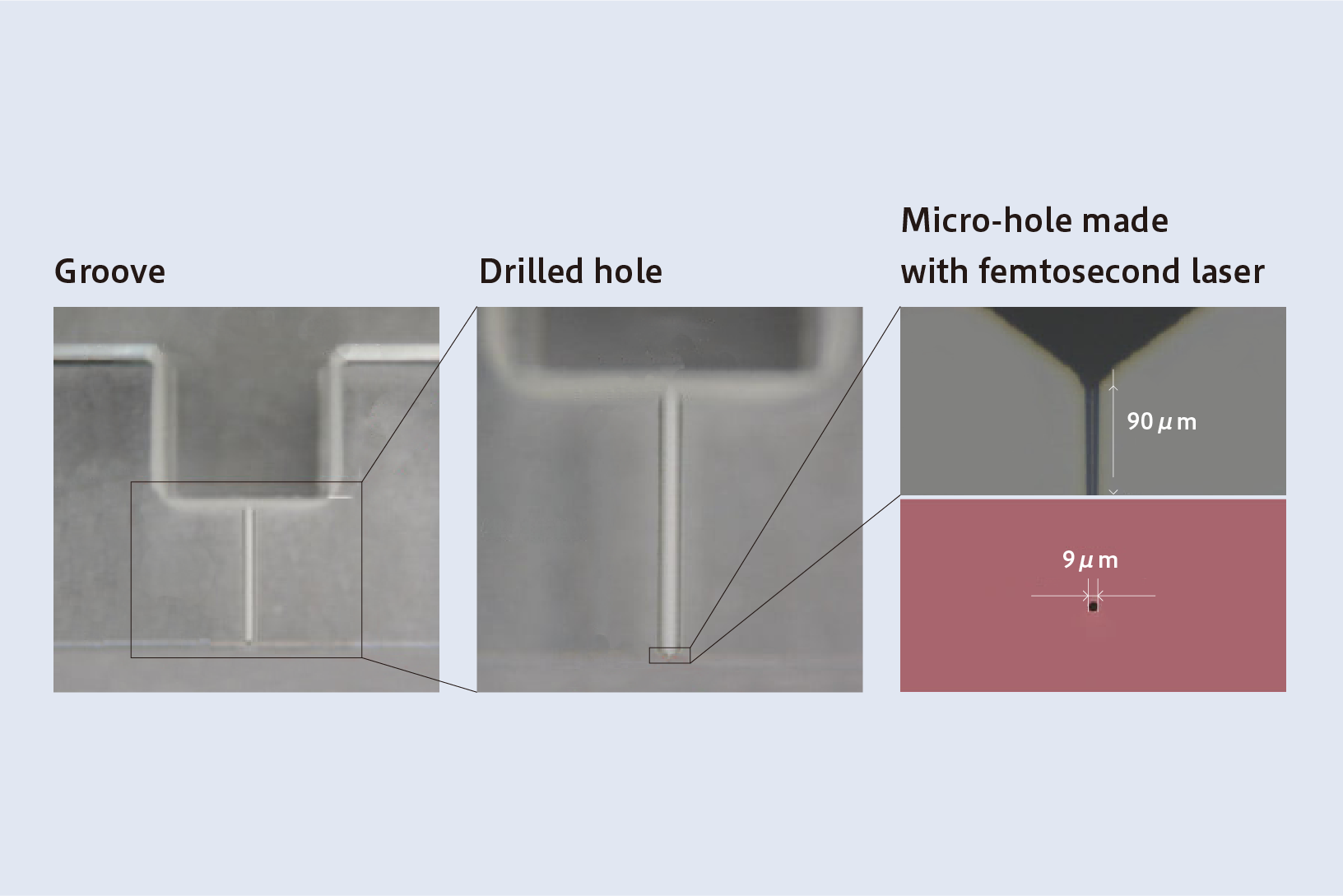
R&D products that utilize the chemical resistance of industrial jewels
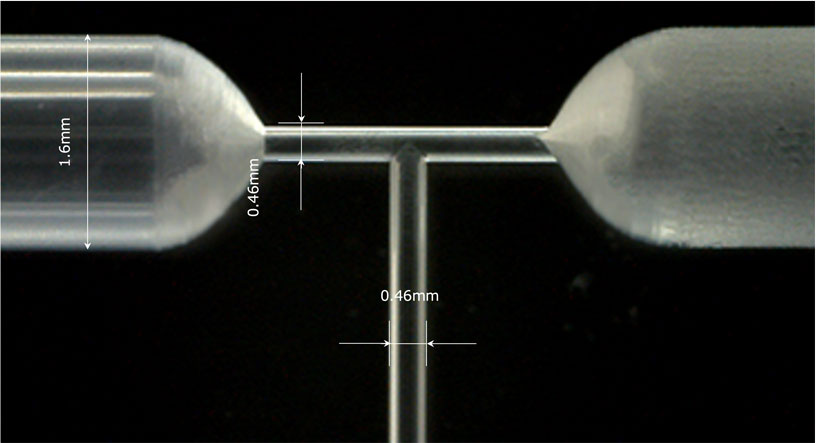
This photo shows a microflow path instrument. Reactants, such as pharmaceuticals, are loaded into the cylinders on either side. The reactants flow through thin 0.46 mm tubes to the reaction chamber. These instruments can be made of resin, but if chemical resistance and durability are required, they must be made of quartz or sapphire.
Adamant Namiki custom makes these instruments based on specifications we receive from research facilities and other clients. In cutting-edge research, advanced chemicals can cost several million Japanese yen (tens of thousands of US dollars) per gram. If the tubes can be made very thin, experiments can be conducted using very small volumes of chemicals, allowing many more trials to be done with a given volume of chemicals. Some reactions can take days to complete at bench-top scale. However, if micro volumes are used, they can be completed in seconds, allowing results of even very slow reactions to be seen quickly.
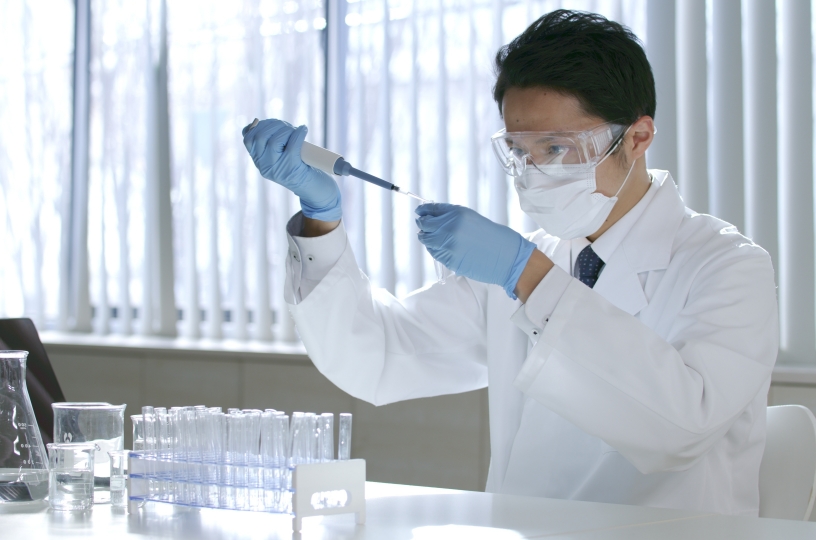
A hole small enough to trap a single cell, used in cutting-edge research
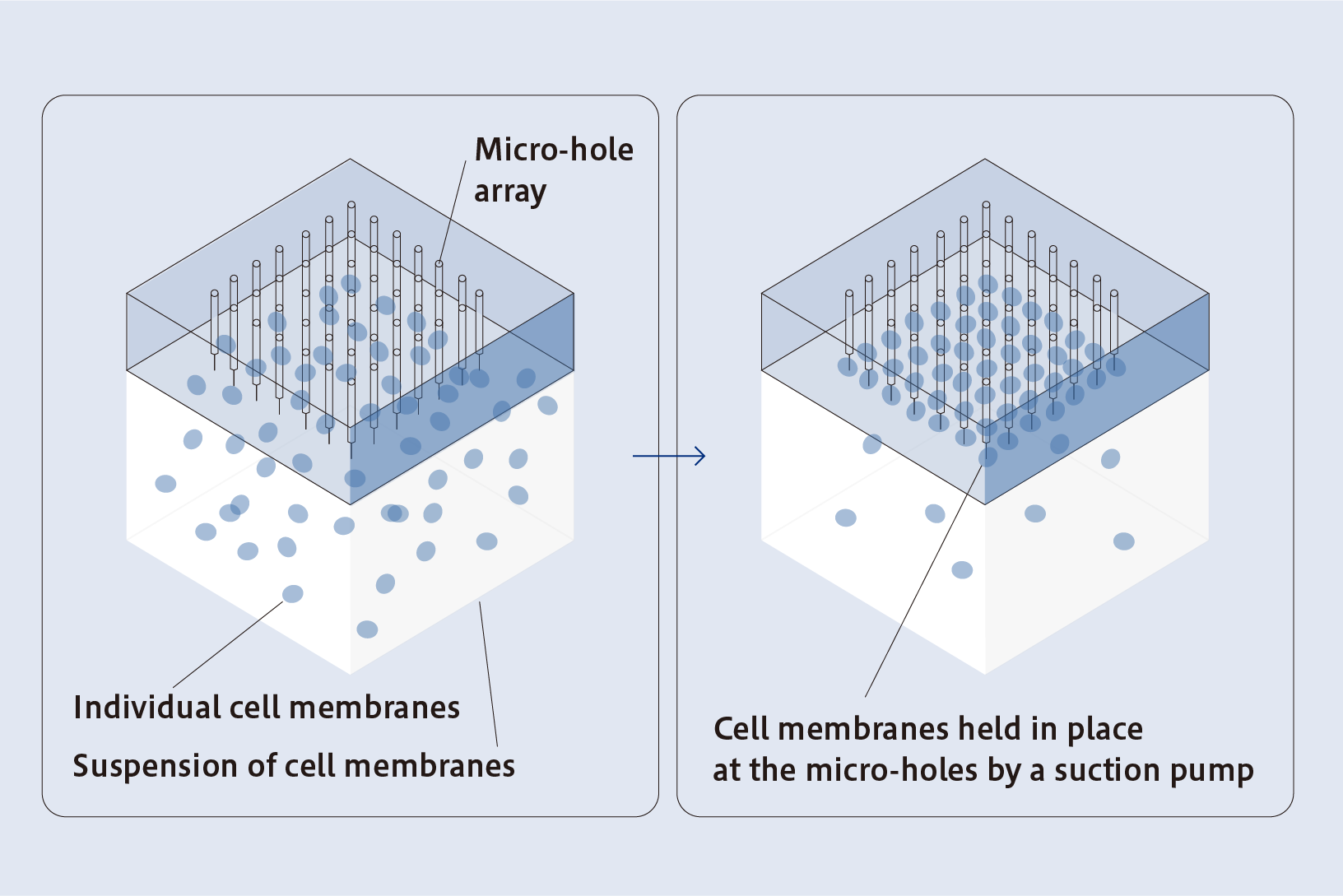
Our jewel processing capabilities are also used in cutting-edge life science research. For example, to observe and manipulate individual cell membranes, researchers use a quartz substrate into which Adamant Namiki has drilled dozens of tiny holes, which are connected to a suction pump. Chemicals are used to break the cell membranes apart from each other, and the individual cell membranes are held in place by the suction coming through the holes. To be effective, the holes must be slightly smaller than the cell membranes, or about 6 ~ 25 microns in diameter.
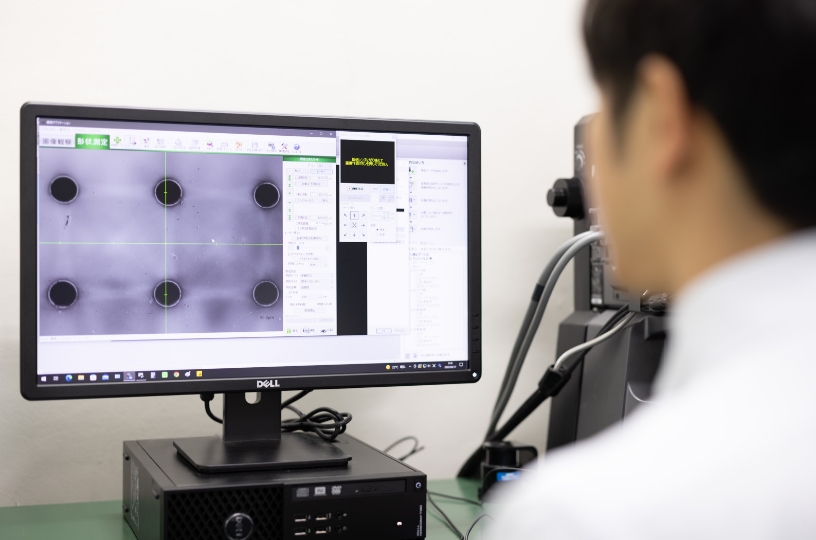
This example of synthetic jewels being used in research to improve or prolong human life is only one of many examples of the ever-expanding set of applications for synthetic jewels, and Adamant Namiki’s leadership in development of new products.
Adamant Namiki has achieved the highest levels of technology in precision jewel processing. In both established and emerging fields, our achievements are difficult for other companies to replicate, and we intend to continue to lead in product development as further new fields emerge.