The basics of laser processing technology and its advantages over other methods
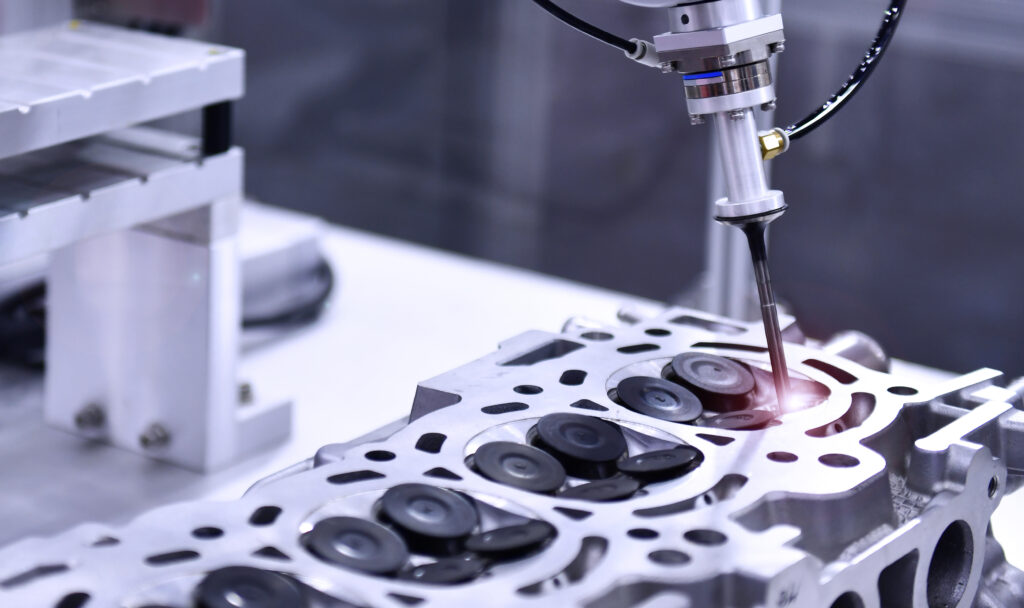
Laser processing technology emerged as a practical tool in the 1960s and 1970s. It offers many advantages over conventional processing methods. Thus, it is used in a wide range of applications across various industries, including the manufacture of industrial products, information and communications technology, and medical technology.
Table of contents [close]
What is laser processing technology?
This section briefly summarizes what laser processing technology is and how it can be used, along with basic principles of the technology.
What laser processing can accomplish
Laser processing technology allows very precise control over the amount of energy delivered to the target area of a material by adjusting the laser output and focus.
This precision allows for the accurate processing of not only hard materials like metal and resin but also various other materials such as wood and leather.
The capability for such fine processing, which is not possible with conventional methods, paves the way for the development of innovative and previously unattainable technologies.
For example, advanced processing of optical fibers using lasers is driving technological development across a broad range of industries, such as information technology, medical devices, industrial machinery, and sensors.
In the field of medicine, lasers can be used to destroy cancer cells through targeted light using specialized optical fibers. In addition, research is progressing into performing bypass surgery without halting blood flow, using an ultra-compact fiberscope system.
In the information and communications sector, there are high expectations for the practical deployment of quantum communications. This technology will utilize the dual particle and wave properties of light to facilitate communications with a capacity more than 1,000 times greater than current methods and significantly lower energy consumption.
In these ways, laser processing technology is fueling the development of various innovative technologies that were not possible with conventional processing methods.
Principles of laser processing technologies
The history of laser processing technology dates back to when theoretical physicist Albert Einstein predicted the phenomenon of “stimulated emission of light,” which laid the groundwork for the laser technologies of today. Light produced by stimulated emission is uniform in wavelength and highly directional. Such emission of light is known as laser light.
Light of a laser is highly directional, and focusing the light with a lens allows for precise focusing of light onto a specific area. Moreover, because laser light has a more consistent wavelength than general light, it interacts more intensely with the target, delivering large amounts of heat to the focal area. This capability enables precise processing of various materials through heating.
Laser beams are primarily controlled through the use of polarizers. When the directions of multiple polarizers are aligned, the laser light is able to pass through. Rotating any of the polarizers will start to filter some of the light energy.
However, due to the wave properties of light, it cannot be completely blocked, and some light leaks through. The ratio of this leaked light to the laser output is known as the extinction ratio. The better this ratio, the higher the performance of the laser system.
5 advantages of laser processing
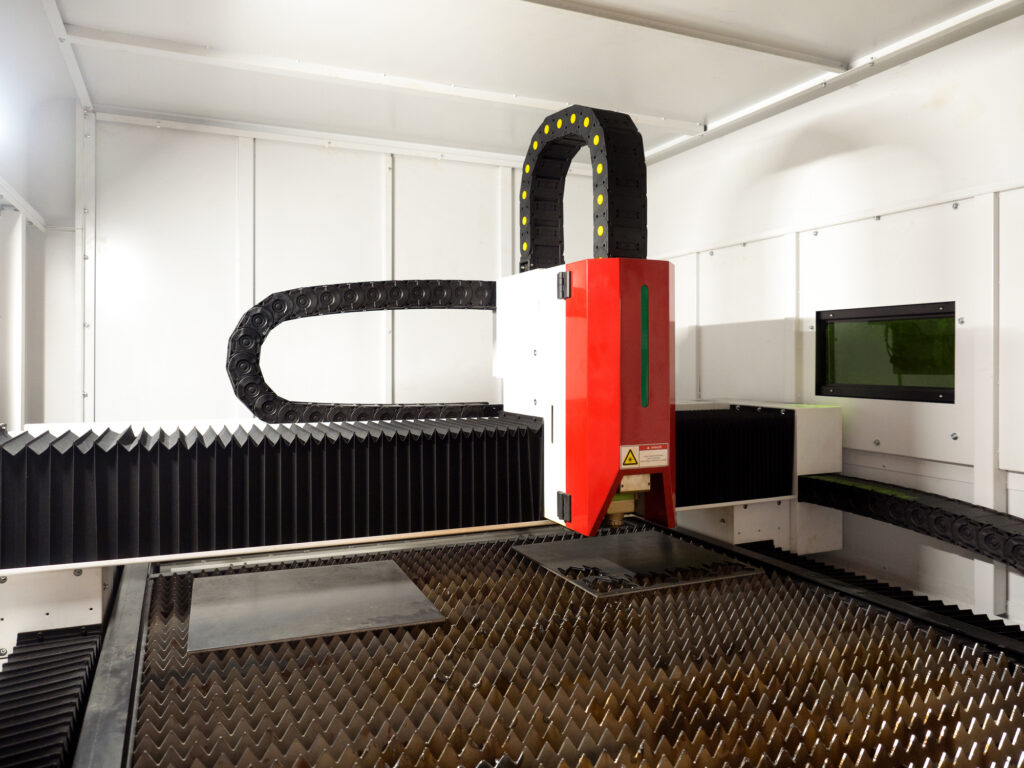
Laser processing has many advantages over conventional processing methods.
This section describes five of these advantages.
Can be applied from small-scale to large-scale processes.
Common methods for processing metals and resins in industrial production include techniques such as press processing and injection molding. Such methods rely on pre-made molds and processes that require highly specially tools developed just for that purpose. However, the creation of molds and specialized machine tools is both expensive and time-consuming, making them unsuitable for small-scale production.
In contrast, laser processing equipment operates by directing laser beams onto specific areas according to a programmed routine. Once this program is established, a single machine can manage multiple processes. This allows for the handling of small-lot production without the need for the development of new molds or specialized machine tools for each process.
Additionally, once a program is developed, the same process can be consistently replicated, enabling mass production. This repeatability allows laser processing to accommodate the production needs of both small-scale and large-scale processes.
Can flexibly accommodate changes to products.
While mass production via mechanization is efficient, it is not easily adaptable to accommodate product changes. With traditional methods that use molds or specialized machine tools, even minor changes in product design require replacement of the molds or physical modifications to the machining tools.
In contrast, laser processing machines, which operate based on programmed instructions, can quickly adapt to design changes simply through adjusting the parameters of the program. Furthermore, by tweaking hardware aspects such as laser output and lenses, changes in material types can also be accommodated. This flexibility allows for prompt response to minor product changes or defects as needed.
Has micro-level precision.
Laser processing technology utilizes a highly directional beam of laser light to perform pinpoint processing, allowing for extremely fine work. The targeted area is heated precisely without physical contact. This helps ensure high processing accuracy by eliminating the likelihood of bending or distortion caused when a tool presses on an object.
Nanometer-scale processing has been achieved using laser processing technology. This level of precision is unattainable with other machine tools. As a result, laser processing is increasingly used in the manufacture of electronic and medical equipment, which requires ever-smaller components.
Can accommodate a wide range of products.
Laser processing technology has the ability to precisely adjust processing accuracy and temperature by modifying the laser output and the focusing lens. This allows for tailored responses to the physical properties of different materials, such as melting points and ignition temperatures.
Even materials that are heat-sensitive can be processed with minimal thermal distortion through careful adjustments. Moreover, because the laser operates without physical contact, it can process a diverse range of materials, from hard substances like metals and resins to softer materials such as leather and fabrics.
Laser technology is not limited to drilling and cutting; it can also be used for engraving and etching by carefully controlling the heat, making it highly versatile for many applications. As it can handle a wide array of materials, it is suitable for producing a variety of products.
Low maintenance leads to increased efficiency.
Unlike traditional methods such as polishing or cutting, laser processing technology does not involve direct contact between the tool and the material being processed. This eliminates wear and tear and the need for oil replenishment, leading to a reduction in maintenance time and costs. In addition, laser processing produces fewer byproducts such as chips and dust during processing, reducing the cleanup and making the work process more efficient.
While laser processing machines are not completely maintenance-free, they require much less upkeep compared to other machine tools. For instance, cleaning equipment like lenses is less costly and demands less effort, further enhancing overall efficiency.
Orbray’s laser processing technology
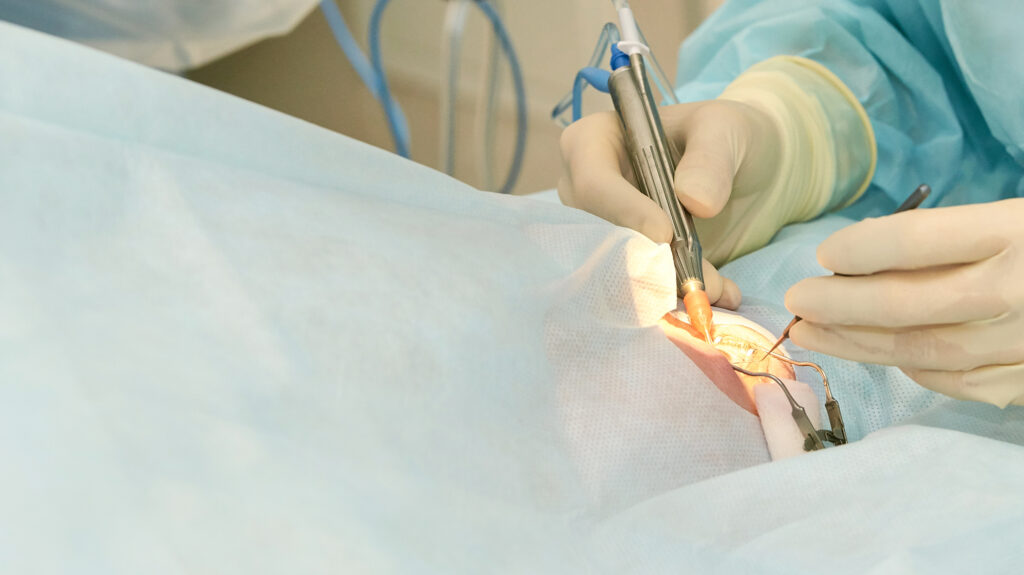
Orbray uses laser processing technology for applications that require high precision, such as optical fiber tip processing and strip processing.
In optical fiber tip processing, laser technology enables the precise shaping of fiber tips into various shapes, allowing us to create optical connections with significantly reduced insertion loss. Additionally, by crafting the end face into specialized shapes, the emitted beam's shape can be controlled, making it applicable to diverse fields such as medical equipment and sensor technology.
For strip processing, laser technology has made it possible to efficiently remove coatings from optical fibers, which were challenging to strip with conventional methods. For instance, polyimide coatings, known for their high heat and chemical resistance, can be removed using laser processing without damaging the underlying optical fibers.
Through these applications, Orbray continues to research, develop, and provide advanced solutions based on laser processing technology, enhancing performance and versatility in various industries.
Femtosecond laser processing
As the name suggests, Femtosecond lasers emit extremely short pules of laser light that are just femtoseconds in length (1.0 x 10-15 seconds). Femtosecond laser processing uses these lasers in the production process.
Using lasers with such a brief pulse minimizes the amount of time that a material is exposed to the laser energy. This allows heat-sensitive materials to be processed without causing heat distortion or cracking.
Furthermore, when focused, this technology achieves high laser intensity near the focal point, enabling pinpoint heating. This capability allows for the processing of materials that are typically unmanageable with standard laser processing techniques.
⇒ For more information about Orbray’s femtosecond laser processing, click here.
https://orbray.com/en/product/jewel/technology/femtosecond-laser.html
UV laser processing
UV laser processing utilizes a laser with a wavelength of 355 nm, which is shorter than the wavelength of violet light (360 nm to 400 nm), for precise laser processing.
Because of this very short wavelength, the laser can be focused into a very small diameter using a lens, allowing for even more precise processing than typical laser processing.
This technology allows for the processing of materials, such as sapphire, that are typically unmanageable with standard lasers. Consequently, it broadens the range of materials that can be effectively processed.
⇒ For more information about Orbray’s UV laser processing, click here.
https://orbray.com/en/product/jewel/technology/uv-laser.html
CO2 laser processing
CO2 laser processing uses lasers generated using carbon dioxide gas.
Co2 lasers have long wavelengths of 9.2 to 10.8 µm. Of the various laser processing technologies, CO2 laser processing has a long history and is the most widely used technique for laser processing.
It is capable of processing a broad range of materials and is particularly effective with materials that do not absorb light, such as acrylic and glass, as well as non-metallic materials like wood and leather.
Another benefit of CO2 laser processing is its high energy efficiency. Additionally, it is generally more cost-effective and easier to install compared to other laser processing machines.
Green laser processing
Green laser processing uses a laser with a wavelength of 532 nm, which is in the green range of visible light.
Green laser light has high wavelength absorption capabilities and can process a wide range of materials. It is particularly effective with highly reflective metal materials such as gold and copper, making it widely used in the manufacturing of various industrial products.
Due to its ability to easily condense light, the green laser can perform precise processing on small, targeted areas. Furthermore, by using low power, specific heat processing can be achieved without damaging the material.
Semiconductor laser processing
Semiconductor laser processing uses diodes to generate the lasers used for processing materials. Diodes are highly energy efficient as they directly convert electricity into light, allowing for high-output processing while conserving power. In addition, due to their simple structures, the processing machines are relatively small and require minimal maintenance, making them suitable for use in various locations.
The versatility of diode lasers, based on their wavelength characteristics, extends to applications such as fusing resins together and, more recently, fusing resins with metals. They are also commonly used for soldering precision electronic components.
YAG (yttrium aluminum garnet) laser processing
YAG laser processing uses lasers generated using artificial crystals. This ensures that there is no deterioration over time, allowing for stable processing over a long lifespan. The versatility of YAG lasers is enhanced by their ability to be transmitted not only through mirrors and lenses but also through fibers. This capability gives them a small turning radius, enabling complex processing tasks.
With the ability to operate at high output, YAG lasers are particularly effective for metal processing, and are commonly used for cutting, drilling, and laser welding. Laser welding with YAG lasers offers the advantage of precise, contact-free welding, enhancing the quality and precision of the welds.
Summary: Laser processing technology
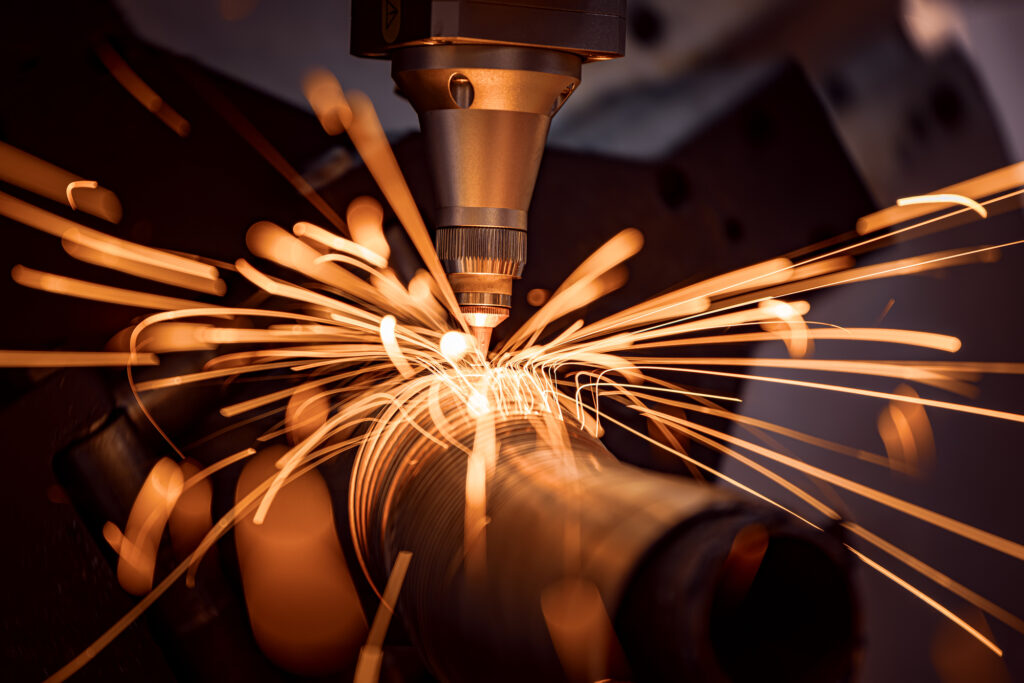
This article explored the characteristics and potential applications of laser processing technology. The key advantage of laser processing is its precision, which allows for flexible application across a wide range of products.
If you would like to learn more about Orbray’s laser processing technology, please visit our detailed explanation page for further information.
-
What is LiDAR? How it works, technologies, and applications
-
Drilling methods for micrometer to nanometer sized holes and their applications
-
All About Lasers: How they work, their properties, and their uses
-
Jewel bearings: Orbray and the watch industry [Story of Watch 1]
-
Lensed Fibers: Brief introduction to the functions and manufacturing methods