Lensed Fibers: Brief introduction to the functions and manufacturing methods
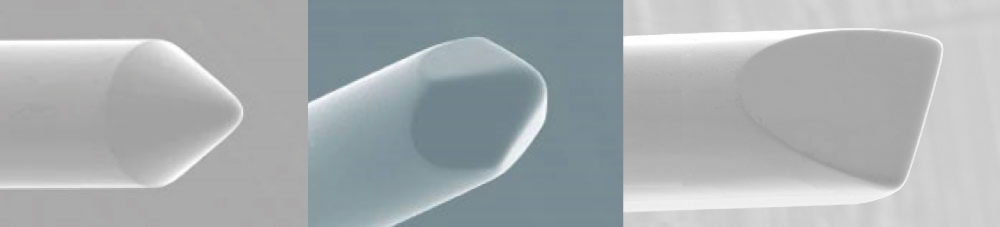
Semiconductor components such as laser diodes, light-emitting diodes, and photo diodes are used in optical communications. These components work by converting electrical signals into light signals or vis-versa, in a process called photoelectric conversion. Optical signals are carried to the semiconductor component through optical fibers and the lensed fibers are used to efficiently connected the optical fiber to the component. Lensed fibers greatly simplify the connection between semiconductor devices and optical fibers.
Table of contents [close]
Essential parts for connecting to the semiconductor devices
Semiconductor components used in optical communications are packed together with other semiconductors, optical parts, and electrical components using metal and resin, as an example the LD butterfly package. In addition to the laser diode chip, isolators that prevent reflected and external light from entering the LD chip, PD to check the output changes of the LD, thermistor to measure LD temperature, and thermoelectric coolers to cool the devices are all packaged together. Each component is connected by leads and wires and the entire package is filled with dry nitrogen gas and sealed tightly.
The optical fiber attached to the package carries the optical output of the LD to other components. To efficiently inject light into the core of the optical fiber, the light must be precisely focused on the center of the core. Conventionally, this was achieved with a lens installed inside the package. In this case, the LD, lens, and optical fiber had to be in very precise alignment and this process was time consuming. This issue is not unique to butterfly packages and photo pump modules (semiconductor optical amplifiers) face similar issues. High precision alignment of lenses with light-receiving and light-emitting elements are required.
The advent of optical fibers with built-in lens functionalities resolved many of these issues. Such lensed fibers have been widely used to greatly simplify the manufacturing process. When lensed fibers are used, only the light emitting/receiving element and the fiber need to be aligned, significantly reducing the time required for the centering process. The number of parts is also reduced, resulting in a much simpler package. Lensed fibers help improve the reliability of the package while reducing the cost of parts.
Select lens type based on the beam pattern
Lensed fibers are available in many shapes, depending on the shape of the light (beam pattern).
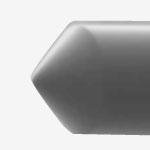
For example, in a Spherical Lensed Fiber (SLF), the end of the optical fiber is processed into a conical shape so that the apex matches exactly with the core of the fiber. SLFs have excellent coupling efficiency for light with circular beam patters. They are often used for optical communication LD modules, optical waveguides, silicon wire waveguides, output to PDs, and for illuminating very minute areas.
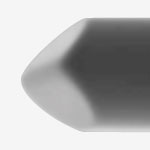
A Cylindrical lensed fiber (CLF) is created by cutting flat incline planes parallel to the core’s axis. This creates a shape like a flat-head screwdriver. The tip of the driver is processed into a semi-cylindrical shape to create a cylindrical lens. CLFs have excellent coupling efficiency for flatly diffused elliptical beam light patters. They are used in LD optical amplifiers, high-power LD packages, optical wave guides, etc.
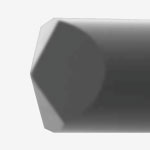
Biconic Lensed Fibers are created by taking the screwdriver shape (CLF) and further cutting equivalent incline planes on orthogonal planes, creating a pyramid-like shape on the tip of the fiber. Each axis acts a lens, corresponding to the long axis and short axis of the elliptical beam pattern. BLFs are used in LD optical amplifiers and optical wave guides. Other shapes, such as ball lenses and diagonal lenses are also available. In addition to beam patterns, lenses can be matched with wavelength ranges (such as 980 nm and 1480 nm) according to the required application.
Processing with low deviations
There are several methods for processing the ends of optical fibers to create lenses, such as etching, melting stretching, grinding, and laser processing. Etching uses the difference in etching rate between the fiber core and cladding to achieve the desired lens shape. In melting-stretching, the lens is created by heating and stretching the fiber, creating a tapered core. The grinding method allows the fiber to be processed into any shape necessary to create the lens. The shape and curvature are selected, and the lens is processed according to the intended use and wavelength range. When grinding a lens, it must be done so that the apex of the lens overlaps with the core of the optical fiber. Even the smallest deviation will greatly reduce coupling efficiency. However, the optical fiber a mere 125 microns in diameter with a core diameter of only 10 microns (single mode) or 50 microns (multi-mode). The highest precision grinding technology is required for creating lensed fibers in this manner. The core position can be monitored to reduce deviations during the grinding process.
-
Ultra-Polishing of Sapphire along the c-Plane
-
Photoelectric fusion devices and silicon photonics
-
Fiber Optic Connector types and applications
-
Drilling methods for micrometer to nanometer sized holes and their applications
-
All About Lasers: How they work, their properties, and their uses
-
Optical attenuators and terminators: How they work and why they are important