What is a Motor Driver?
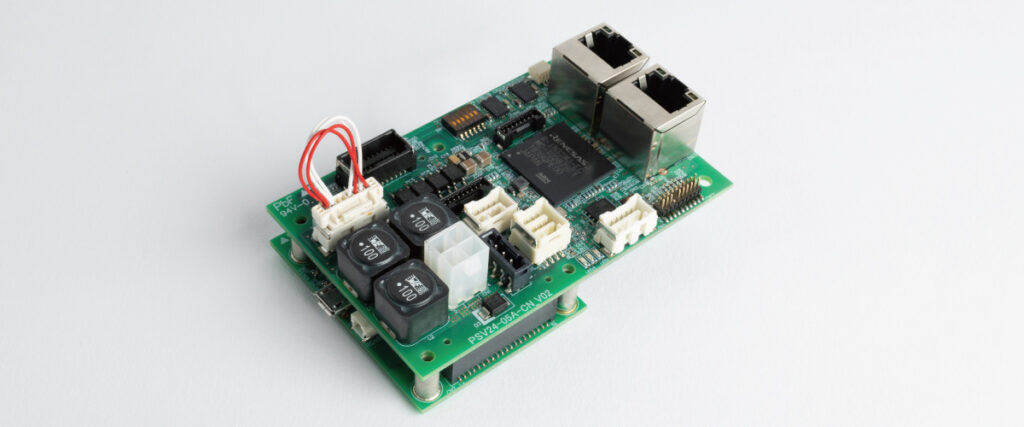
Have you ever wondered how electric motors inside drones, CNC machines, and robots are controlled? The motor driver is the hidden controller of these electronic components. Depending on the external control input signal, it can provide enough power to manipulate the motor's speed, torque, and direction.
This blog will enlist different types of motor drivers. But first, let's dive deep into the basic functioning of the driver and motor control module like motor driver:
Table of contents [close]
The Role of a Motor Driver
It’s an electronic device that can change motor attributes by amplifying current followed by input signals. There are many types of motor drivers classified based on motor categories. Some of them are created specifically for brushless motors, while some possess unique pulsing technologies for Servo motors.
At its core, a motor driver is a intermediary between the host controller and the motor itself. Since the host controller cannot directly run the motor, the driver supplies power in response to the host controller’s signals. As for the motor’s torque and speed, the driver uses controller commands to adjust the parameters.
One thing common across all these drivers is that all of them control and manipulate motor torque or speed in some way. Besides, motor types are not the only parameters that can be used to classify drivers. There are some special attributes, such as drive status, system compatibility, and I/O numbers, that make one motor driver different from the other.
For instance, some models have I/Os that output the motor drive status to external devices. They are also useful for the designated system in understanding the driving status of the motor.
How Does a Motor Driver Work?
The driver can switch between forward/reverse rotation depending on the signal.
In the conventional method, speed and torque are changed by the variable voltage.
In some cases, drivers use Pulse Width Modulation (PWM) driving instead of variable voltage. It is a control that repeatedly turns on and off at a constant voltage and is characterized by its compatibility with semiconductors. Therefore, the driver configuration can be simplified and the efficiency of the driver itself can be increased.
Why Do We Need a Motor Driver?
Many reasons necessitate driver usage. That's why the global motor driver IC market size is expected to hit USD 1567.3 million by 2032.
Here are some reasons why the motor driver is used in electric motors:
- The characteristics that the motor needs to change in order to use it. It must be adjusted using a motor driver to make it happen.
- Every motor has a specific need that is fulfilled by the motor driver. In the case of a servo motor, it is needed for precision and movement.
When it comes to brushless motors, we need the drivers for seamless rotation. That’s because brushless motors cannot be driven by a simple DC input (+/-). - An uncontrollable motor is a hazard for every industrial application. That’s why motor drivers are essential to ensure motor safety. They give control over the motor’s speed, torque, and rotation, which prevents overcurrent and motor burnout.
Types of Motor Drivers
Every motor type has a different mechanism of action. Therefore, its controller unit will also have distinct valuations. Based on the motor types, the drivers are classified into various categories. We would focus on the most common types only:
Brushed DC Motor Driver
In a brushed DC motor, rotation is achieved by applying DC. To obtain the characteristics suitable for the application, input power must be controlled. While there are multiple ways to control this power, a brushed DC motor driver is considered the best. The brushed DC motor driver gives complete control over motor attributes, which enhances the safety and makes its operation more functional.
Brushless DC motor driver
Brushless motors do not have brushes to switch the direction of the current flowing in the coil. Therefore, it is necessary to switch the current for each phase of the coil as described above.
The motor driver alternatively switches the current direction by changing the current for each phase of the coil. That means each alternative switch will generate magnetic field toward rotor. As a result, the motor keeps rotating consistently without any hindrance.
Some brushless motors are equipped with a Hall sensor, and some are not.
The sensor can detect the rotor position and know which phase to apply current to. On the other hand, without a sensor, no detection is possible, and starting performance tends to be inferior to the type with a built-in sensor.
Rotation control improves operating accuracy and user control over the motor. For example, the FG output, a type of I/O, outputs pulses according to the rotational speed, helping the user to know how fast the motor is rotating.
Stepping motor driver
Stepping motors are motors that can accurately specify rotation speed and stop position according to pulse signals.
The driver outputs a pulse command corresponding to the specified number of steps. The stepping motor operates upon receiving this command.
Stepping motors are often used in open-loop control, where they are driven only by unidirectional commands from a higher-level host without feedback of current position, and are easy to control.
Servo motor driver
Servo motors can accurately control angles and rotation speeds by feeding back signals from an encoder.
This driver receives the command input and applies the corresponding current to the motor. A full closed loop (a control method that acquires the current position of the motor and provides feedback) is commonly used.
Examples Of Different Motor Drivers:
In our recent discussion, we have comprehensively outlined the mechanisms by which motor drivers operate. It is our hope that this explanation has highlighted the critical importance of choosing the correct motor driver tailored to each unique type of motor.
At Orbray, we are pleased to offer a diverse selection of motor drivers. These are specifically designed to enhance the performance and efficiency of small motors. Each driver in our catalog has been meticulously developed and manufactured within our facilities. So, you always get the highest standards of quality and reliability.
We are confident that you will find a solution in the coming motor driver examples that exceeds your technical requirements.
Brushless Motor Driver SSD06-R5A:
The SSD06-R5A is a dedicated sensorless 3 phase brushless motor driver, compatible with Orbray's BMN04-08XX and BMN07-12XX motors. Its frequency generator output provides 1 pulse per rotation.
Brushless Motor Driver SHSD24-01A:
The SHSD24-01A is designed for speed control of Orbray's brushless motors, including those with built-in hall sensors and sensorless models. It features various protections and status monitoring via LED or LCD options, as well as analog output. The driver supports external input/output signals for speed and direction control.
Micro Servo Driver PSV24-05E:
The PSV24-05E is a compact servo driver compatible with Orbray's coreless brushed and brushless motors. A motor with an encoder is required for servo drive. It supports various control models such as speed/torque(current)/position and I/O options. Besides, it offers compatibility with EtherCAT and RS485 for synchronous multi-axis control by daisy chain.
Conclusion:
It is important to choose the right motor driver for your motor. It ensures the motor's functional operation for a longer duration. Orbray offers drivers for small motors to help you in your prototyping research and development. If you are looking for a motor driver, please contact us.