Servo-drivers: How they are made and how they are used
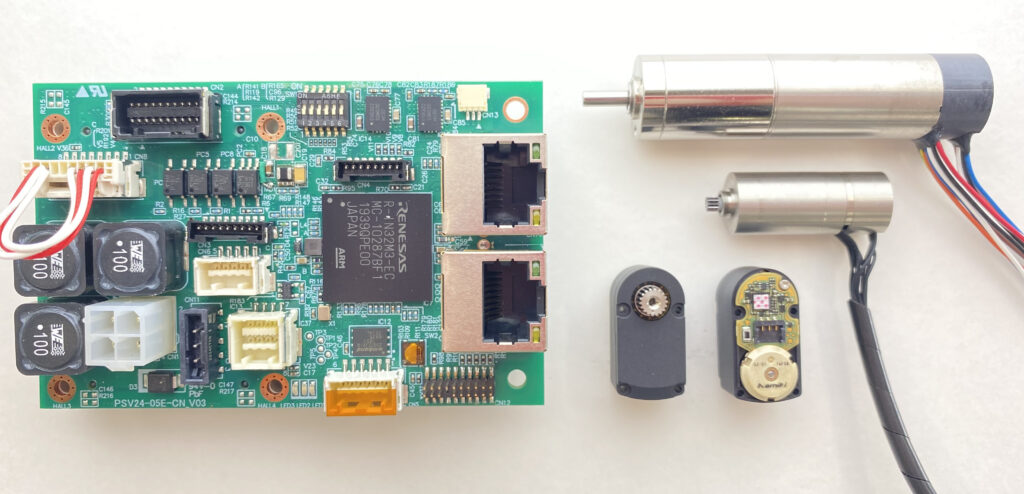
Servomotors are motors that are used in servomechanisms. They are important because they allow the position, speed, torque, and other movements of equipment to be controlled very precisely. Servomotors are often used in drive mechanisms of equipment that require precise positional control, such as in the joints of robotic arms and the movements of processing tables used in semiconductor manufacturing equipment. A motor alone cannot perform precise movements. It must be coupled with servo-drivers that precisely control the motor movements.
Table of contents [close]
Servo-drivers: Controlling servomotors
Servomotors, servo-drivers, controllers, encoders, and other components make up a complete servosystem. Servo-drivers are components that precisely control the movements of a motor according to the settings and signals of the controller.
In order to move a piece of equipment with high speed and accuracy, power to the servomotor must be supplied precisely based on preset values. This is where the servo-driver comes in.

The servo-driver supplies the required power to the servomotor based on drive settings such as rotational speed, position, output, etc., received from the PLC (programmable logic controller) or other controllers. However, the actual position of the servomotor after the operation is indeterminable at this point. Therefore, the servomotor is equipped with an optical encoder (consisting of a light-emitting diode, a disc with slits, and a photodiode), a magnetic encoder (consisting of a magnetic disk and a Hall effect sensor), or a position detection system in order to determine the position of the motor. This data is fed back to the servo-driver, and if there is any discrepancy between the set value and the actual position, the controller sends another set of signals to the servomotor until the error is eliminated.
How servo-drivers work
.jpg)
A servo-driver consists of a power supply circuit and a control circuit. The power circuit delivers controlled power to the servomotors. It includes a power transistor or inverter that converts voltage and current. The control circuit contains circuits that transmit, receive, and process signals from the controller and encoder, and controls the power supplied to the servomotor.
In a servo-system, feedback signals detected by the encoder are returned to the servo-driver, completing a closed loop. This is therefore called a closed-loop control system. Servo-drivers require separate control loops for each dimension of movement, such as rotational speed, position, and output of the servomotor.
.png)
There are two types of closed-loop control systems: full-closed-loop control and semi-closed-loop control. In full-closed-loop control, the position of the driven object is read directly by a sensor, and the servomotor is controlled while comparing this with the set value. A semi-closed loop does not directly detect the position of the driven object, but rather detects and controls the position and speed of the servomotor with an encoder or the like. Many servosystems use semi-closed-loop control systems.
Miniature robots and the compact servo-drivers they require
Servosystems are used in a wide variety of industrial equipment. To operate the joints of large-arm robots, such as those used in automobile manufacturing, servosystems must have the power to lift heavy objects and also the capability of very precise position control. Manufacturing equipment and inspection equipment found in production factories use servosystems to position processing tables that move and rotate the product, and to control the movement of various parts. Servosystems are also used in processing equipment that performs high-precision press work by precisely controlling the movement of the moving parts of the press. In addition, servosystems are indispensable in equipment with drive units that require precise position control, such as in automobiles, trains, theme park equipment, and various home appliances. Servo-drivers have played an important role in such servosystems. Any device that requires a servomotor also has a servo-driver.

The use of drones and small industrial robots has increased in recent years. These systems require servomotors that are small but have high low-end torque. Very precise movements are also required. Currently, servomotors are being developed that are optimally designed for the joints of small robots by arranging parts such as drive motors and gears in a precise and optimal layout to fit in a limited space.
Servo-drivers must also be installed inside the devices. Each type of servomotor requires particular types of servo-drivers to optimize the motor’s performance. For example, servo-drivers installed in robots must be very compact.