Watch glass [Story of Watch 2]
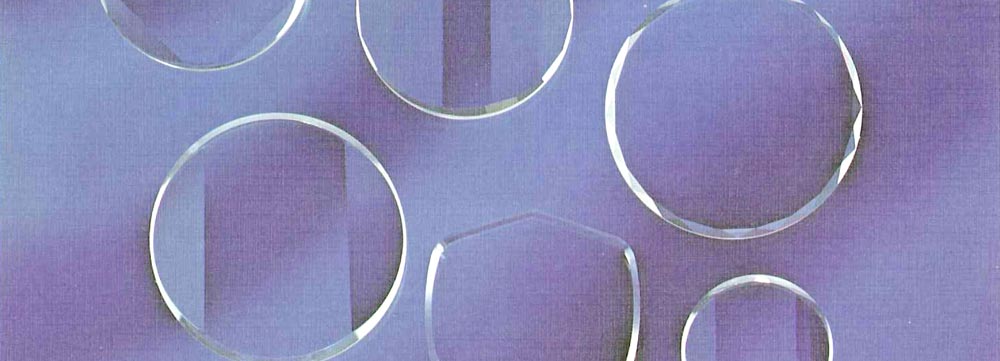
Table of contents [close]
The birth of crystal glass
With the demands of the time, the plastic that had previously been used for watch glass was replaced with crystal glass that didn't discolor or scratch.
Though plastic was an inexpensive, transparent material that was easy to mold and process, when used as an exterior part of a wristwatch, it was prone to discoloration from ultraviolet rays, and scratched and cracked more easily than metal cases.
Against this backdrop, Orbray developed a revolutionary high-strength crystal glass.
In the 1970s, this crystal glass made Citizen’s Crystal Seven line of watches become widely known for being unbreakable.
Chemically-strengthened glass: The ion exchange process
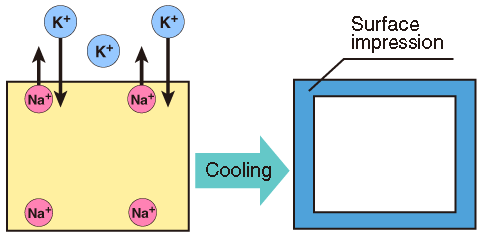
When soda-based glass is soaked in molten potassium nitrate at 300-400℃ for 8 hours, sodium ions (Na+) in the glass seep into the molten salt and are replaced by larger potassium ions (K+).
This process is called the ion exchange process.
Alkali | Ionic radius(A) |
Li+ | 0.60 |
Na+ | 0.95 |
K+ | 1.33 |
Rb+ | 1.48 |
Cs+ | 1.69 |
Compressive stress is generated on the ion-exchanged glass surface layer, which greatly increases the hardness of the surface layer compared to the middle layer, and results in stronger glass that is less likely to break.
This method of strengthening glass is called "chemical strengthening" to distinguish it from physical strengthening methods such as air-cooled strengthening.
K1 glass was developed from this chemically strengthened glass.
Developed in 1980 in collaboration with Ishizuka Glass Co., K1 glass is a high-strength glass with a colorless transparency like white plate glass.
By deepening the ion exchange processed layer, the strength of the watch glass was maximized, making it possible to reduce the glass thickness from 1.2mm to 0.8mm while still ensuring it met the required load capacity. Because of its strength, this glass was adopted for diver’s watches as well as Casio’s G-Shock.
Thus, exquisite Japanese wristwatches resistant to breakage, scratches, and discoloration were accomplished using chemically-strengthened glass as the cover glass.
The barn factory system: Agriculture and industry combined
Inspired by a clock workshop in the Jura Mountains in Switzerland, Orbray's founder started a barn factory system in the early 1970s where farmers could work during the off-season. This system allowed for a workshop with machines for light processing or assembly work to be set up inside a farmer's barn.
When the barn factory program was submitted for approval to Akita's prefectural office, then-Governor Obata was impressed by the plan.
Akita Factory was designated as the central hub with the barn factories as satellite workshops, creating the first satellite base in Oshima village. Within two years, operations had expanded to 12 villages and 42 satellites workshops.
Every morning, materials were distributed to each barn factory, and finished parts were collected and brought to Akita Factory for inspection and final assembly.
The system was well-received by farmers, since it meant they no longer needed to leave their homes to find work in the winter.
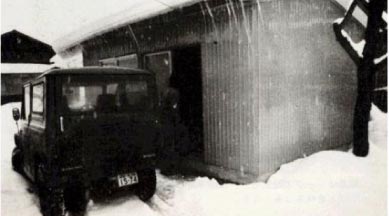
Even today, we as a watch component manufacturer have continued launching unique watch parts.
-
Watch Parts: Beautiful work of craftsmanship -the world's first artificial diamond parts-
-
The advantages and characteristics of ceramic watches
-
Crystal of Jewel
-
Jewel bearings: Orbray and the watch industry [Story of Watch 1]
-
Metallic Glass Features and Applications of a New Type of Metallic Alloy
-
Hard materials and cemented carbides: Characteristics and processing methods