Connecting the world: Our ferrules play an essential role in optical communications
Orbray’s Future,Vol.3
On January 1, 2023, we changed the name of our company,
Adamant Namiki Precision Jewel Co., Ltd., to Orbray Co., Ltd.
Through the years, every department of Adamant Namiki has developed many technologies and capabilities by working side-by-side with our customers. Our Photonics Department has developed and grown in step with the internet and the fiber-optic communication industry since the 1980s, to become one of Adamant Namiki’s core business divisions.
How our ferrules are used in connecting the world
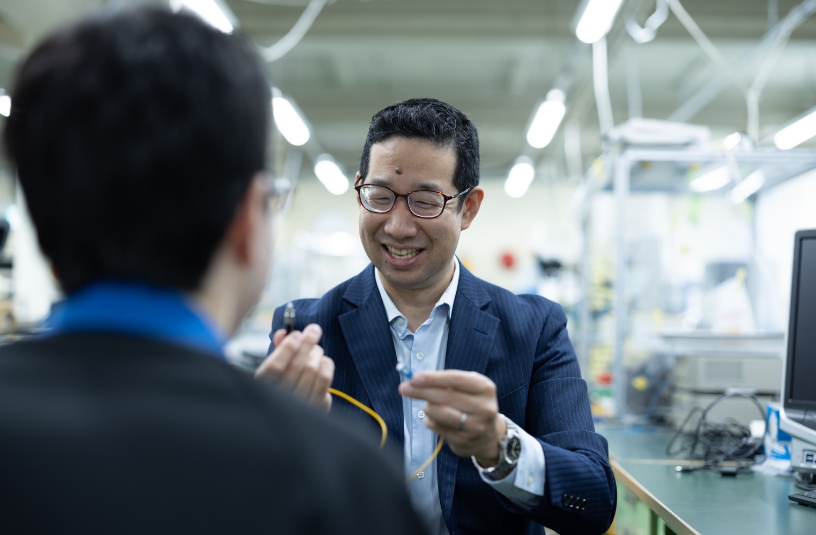
Photonics is the study and application of photons, or light. One of the main applications of photonics is fiber optics, which is used for telecommunications and computer networking, along with other important applications. In the past, large-volume communications were transmitted using coaxial cable. However, today very thin optical fibers made of glass are used to transmit even greater volumes of data. The fibers are a mere 125 microns in diameter, or about the width of a human hair. These optical fibers are connected to each other as well as to other components using zirconia ceramic ferrules. If the fibers in the ferrules are even slightly misaligned, by so much as one micron, the loss in signal is significant.
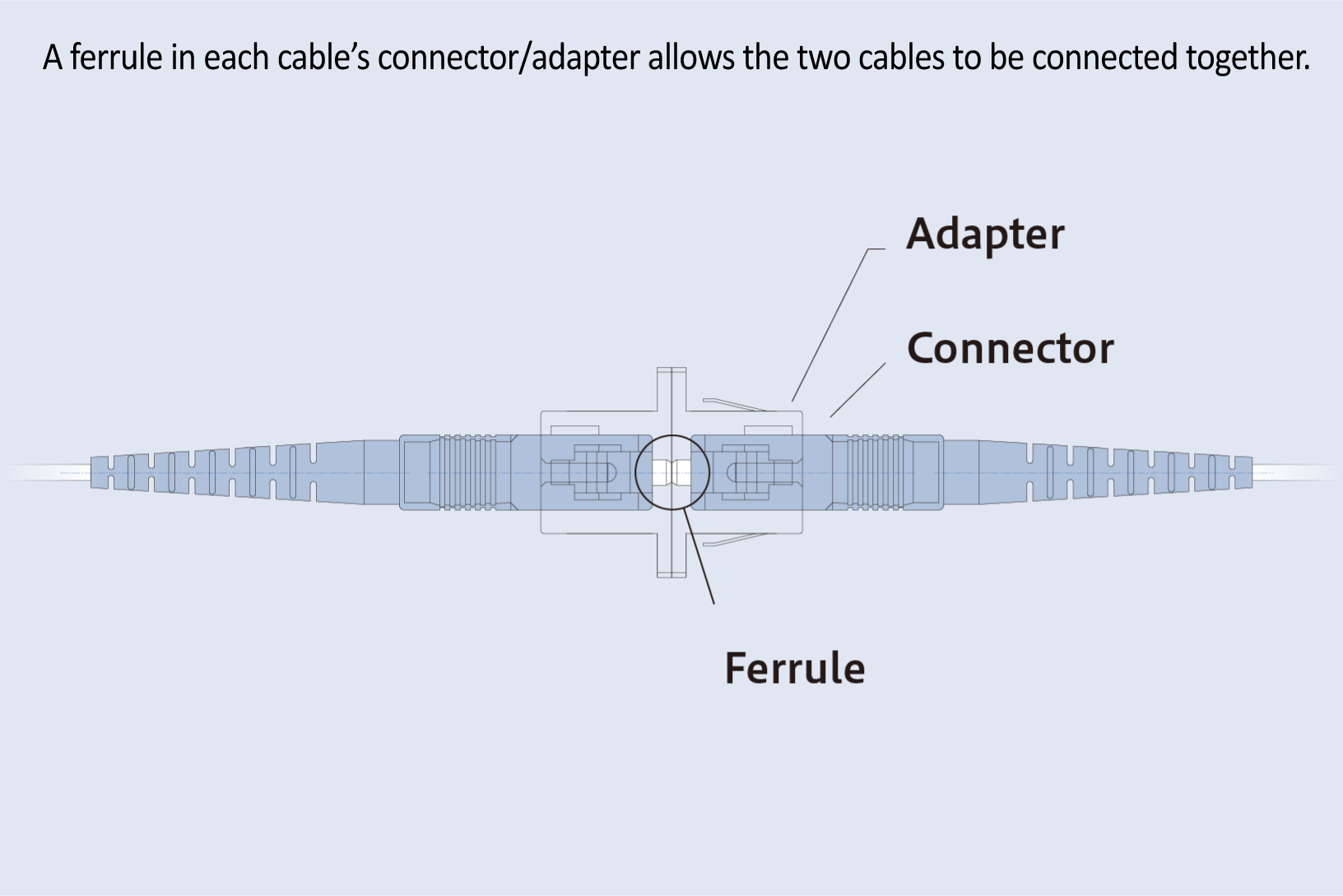
Ferrules are high-precision ceramic parts, with tolerances of less than 1 micron
These simple-looking white objects are ferrules. At first glance, they may appear easy to mass produce, but these ferrules are made of high-tech ceramics. Ceramics are hard, inorganic materials similar to pottery but much more sophisticated. As ceramics contract or shrink during the sintering process which requires extremely high heat, the shaping of the ceramic ferrules to within tolerances of less than one micron is not easy. It requires a process with over fifteen additional advanced steps, such as accounting for the shrinkage and changes that take place during sintering, alignment of the holes, and polishing, each of which is backed by years of Adamant Namiki’s technical expertise.
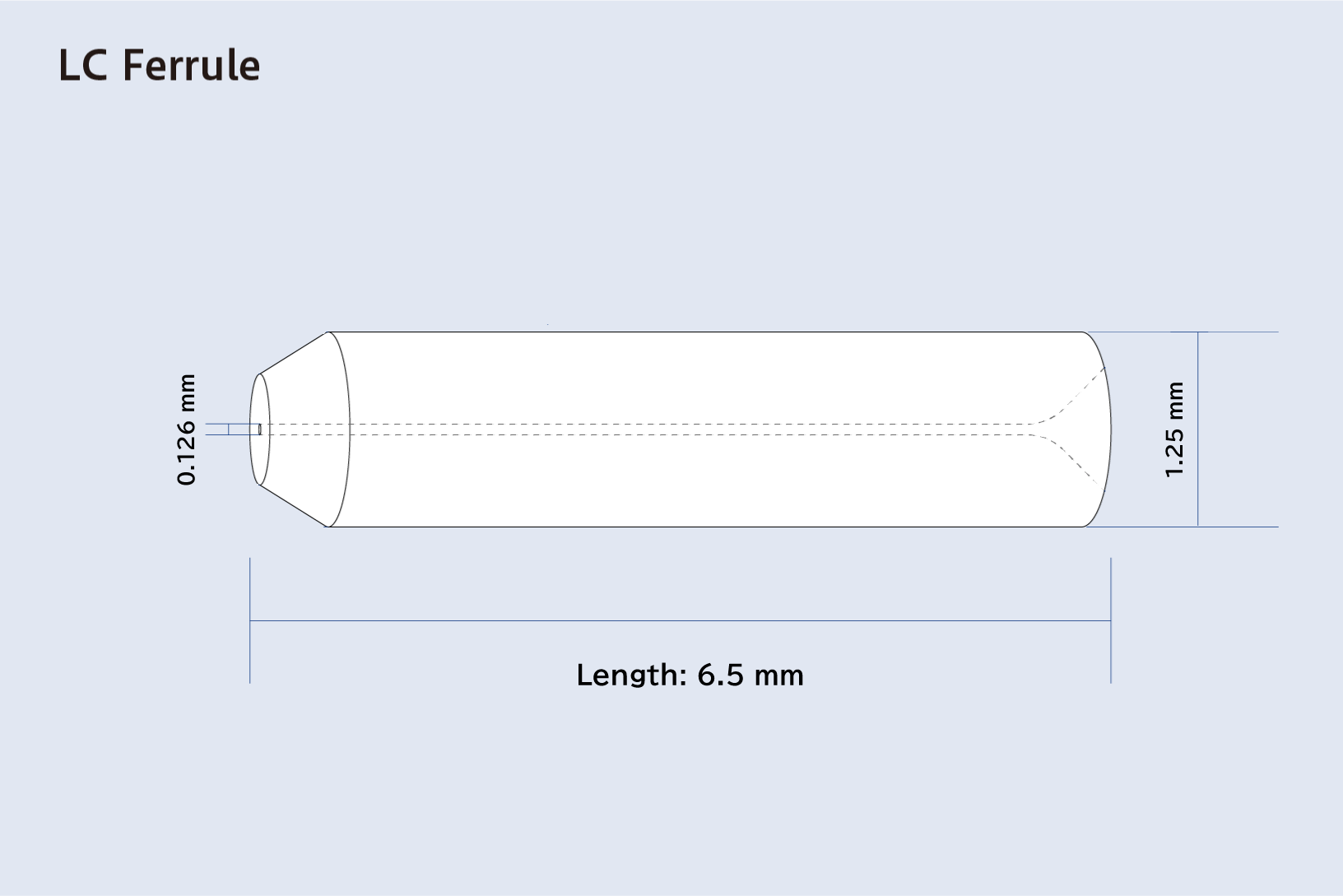
Top industrial jewel processor applies its expertise to ferrules, becomes global leader in ferrule production
Because Adamant Namiki possesses core technologies relevant to making high-precision ferrules, the rapid expansion of the internet around the world has resulted in significant business growth. Adamant Namiki continues to be one of the top ferrule manufacturers in the world.
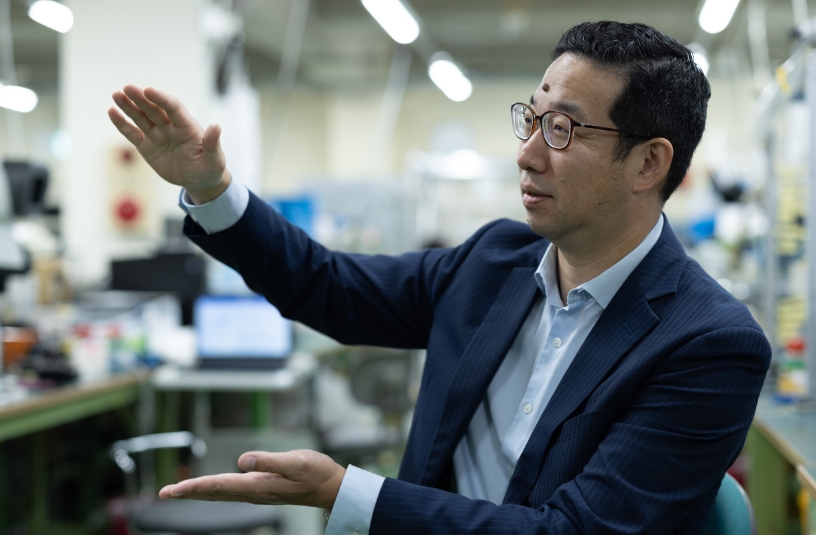
Ferrule development began in 1978 with a request from NTT (formerly Nippon Telegraph and Telephone Corporation). At the time, Adamant Namiki was known for its ability to accurately drill tiny holes in jewels to mass-produce axle bearings used in electric meters and watches. This combination of precision and mass production capability was the target of NTT’s request. Since it was the early days of fiber-optic communications, processing machines, inspection equipment, and methods were all developed in-house. Adamant Namiki incrementally improved and refined each process until the first alumina ceramic ferrules with the required precision were created two years later. The ferrules were introduced in an exhibition in the United States and have been a staple of optical communications ever since.
In recent years, optical connections in the home have become widespread. Optical Network Units (ONU) are internet modems that convert incoming optical signals into electronic signals that routers and computers can process. Ferrules are used in these ONU connections.
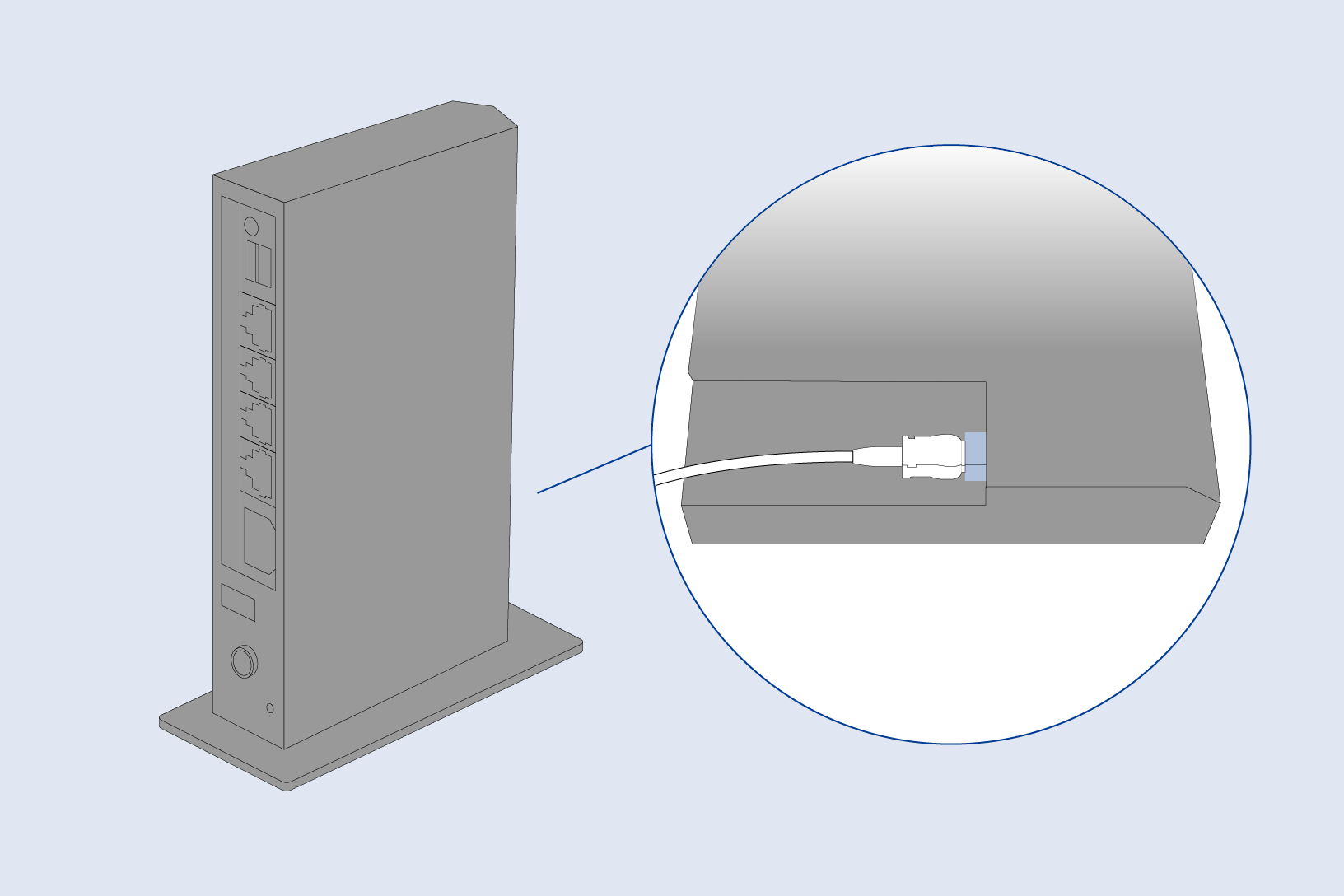
As fiber optics rapidly spread in the mid-1980s, demand grew for the connectors able to transmit large volumes of data with minimal signal loss. At the time, the ends of the ferrules were polished flat. To ensure a good optical connection and prevent signal loss, refractive index matching material had to be applied to the connecting surfaces. Again, at the request of NTT, Adamant Namiki developed technology to polish the ends into a rounded shape to ensure good optical connections without the need to apply any refractive index matching material.
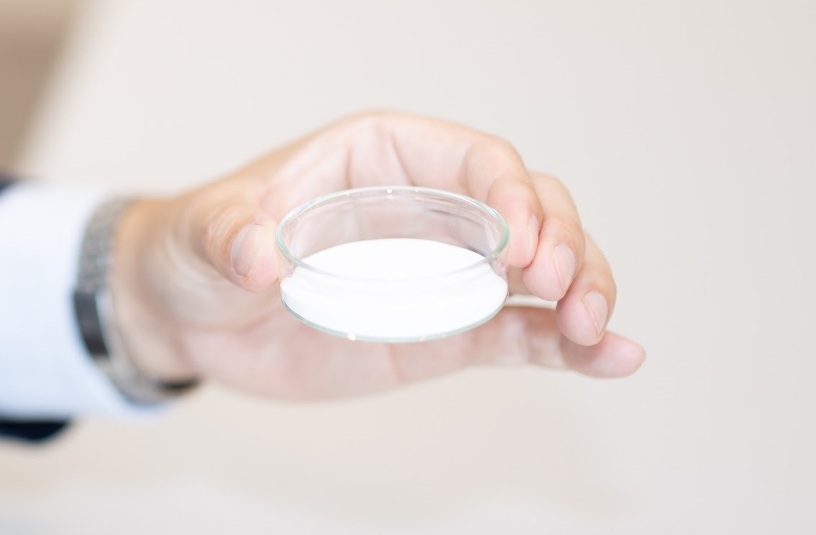
In further advancement of our technology, Adamant Namiki developed zirconia ceramic ferrules in 1987. Zirconia ceramics is much stronger than alumina ceramics, increasing the durability and precision of the ferrules.
Price competition started to increase around this time. Up to this point, extrusion molding was used to manufacture the ceramic ferrules. In this process, a ceramic powder compound was extruded through a die, and the resulting piece was cut to the desired length and sintered to harden. Holes were drilled, and the entire ferrule was polished as required.
The extruded parts were made slightly bigger than required so they could be cut and polished down to the correct dimensions. This required many cutting and polishing steps, needing long labor hours and significant cost. Rejected pieces were also quite common. In addition, the hole for the optical fiber needed to be drilled perfectly smooth, as the fiber could be damaged if the hole surface was rough.
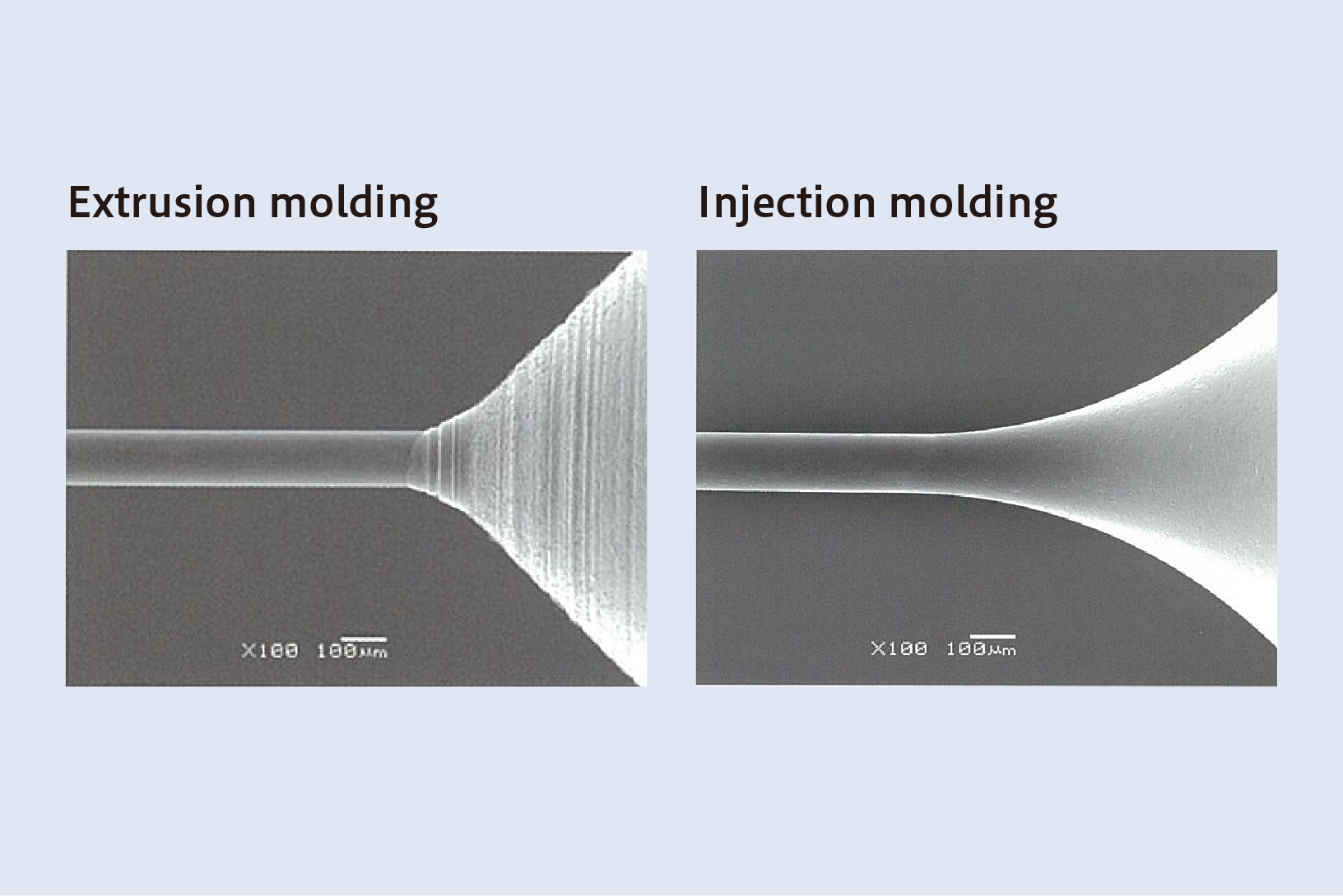
R&D and production in Japan support the sophisticated needs of our customers
In trying to overcome these challenges, Adamant Namiki engineers considered injection molding. At the time, injection molding was generally considered inferior to extrusion molding in terms of cost and precision. However, by applying its proprietary injection-molding technology and expertise cultivated during the development of other products, Adamant Namiki developed new injection-molding technology for ferrules. The innovative technology eliminated the need for drilling. It also saved time and cost because it did not require parts to be made larger, then cut and polished down. Mass production using this high-precision injection molding technology has become the standard at Adamant Namiki.
Ongoing advancements in automation, refinements in the in-house production of zirconia compounds, and improvements in processing equipment and in the process itself have continued to improve our manufacturing performance.
Today’s ferrule market is beset by fierce price competition, as many ferrule manufacturers have emerged, especially in Asia. Although many peer companies have been closing factories in Japan, Adamant Namiki continues to mass-produce ferrules in Japan.
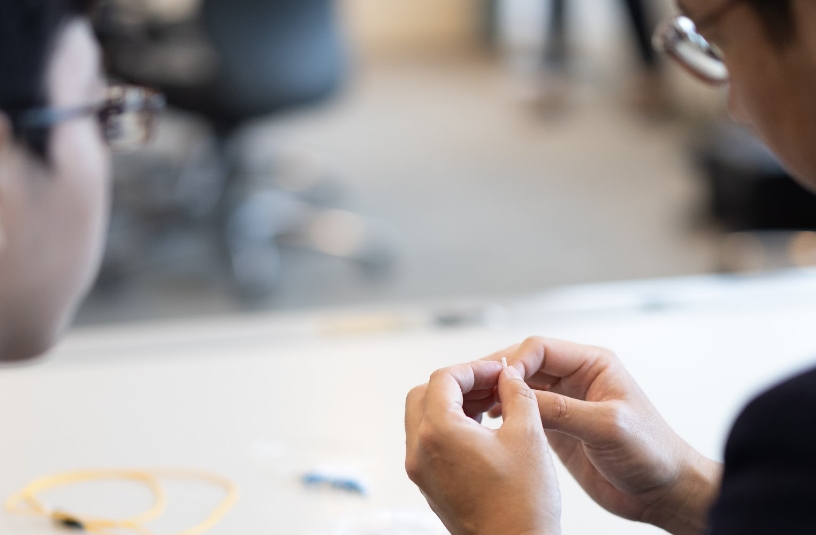
Although overseas production can result in cost savings, it can also bring uncertainties related to natural disasters or geopolitical influences. That is one reason that Adamant Namiki has maintained its capabilities in Japan, with its research and development (R&D) division in Tokyo, and main production in Akita, Fukushima, and Kagoshima prefectures. Maintaining a production base in Japan also allows the company to advance its R&D more smoothly and with greater speed, and thereby develop new products quickly to meet the exacting needs of our most demanding customers, while maintaining the high reliability they have come to expect.
Having its production and R&D in Japan also allows Adamant Namiki to innovate into related areas. For example, in addition to ferrules, Adamant Namiki has expanded into the production of components and devices that incorporate ferrules and has launched many such products into the market.
That is why over 200 customers, including major domestic telecommunications companies, electrical companies, and international semiconductor manufacturers and IT service providers have come to depend on Adamant Namiki and our products.
Demand for ferrules continues to rise, as ferrules are used in a wide array of optical devices, in addition to communications. Within communications, as the world transitions from 4G to 5G technology, demand for optical devices and ferrules is rapidly increasing. This is because 5G signals do not travel as far as 4G signals, so a larger number of antennas and relay stations are required.
Furthermore, as streaming services such as Netflix continue to grow, and as major technology companies such as Google, Amazon, Facebook, and Apple continue expanding their service offerings, data centers are also increasing. This will add to further ferrule demand.
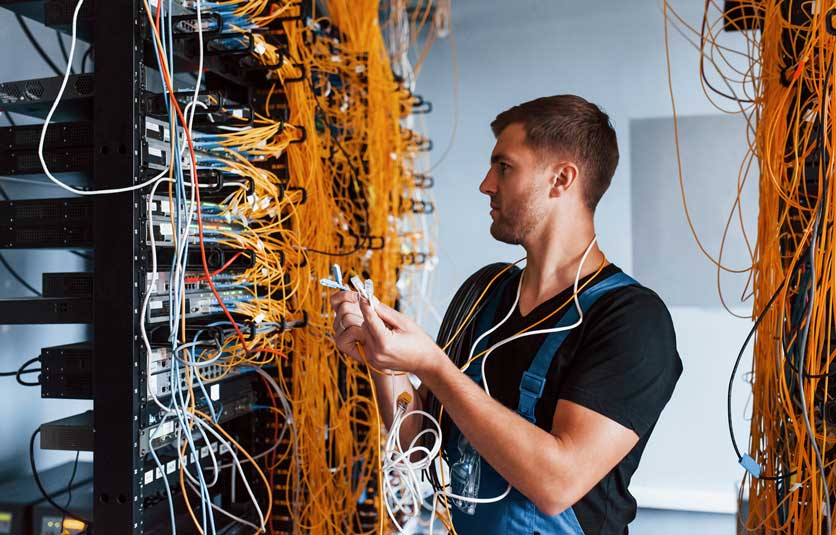
Developing new ferrules to accommodate new standards and increasing data volumes
Growth in demand for fiber-optic applications is spurring interest in finding ways to increase the transmission capacity of fiber-optic cables. Optical fibers have a single, 125-micron core. The maximum transmission capacity of such a core is thought to be around 100 to 150 terabytes per second (Tbps). To transmit larger volumes of data through the same size cable, research into multi-core optical fibers and other technologies is being conducted.
Adamant Namiki is conducting its own research in the field to solve such problems as the great difficulty in aligning multiple optical cores with the extremely high accuracy that is required.
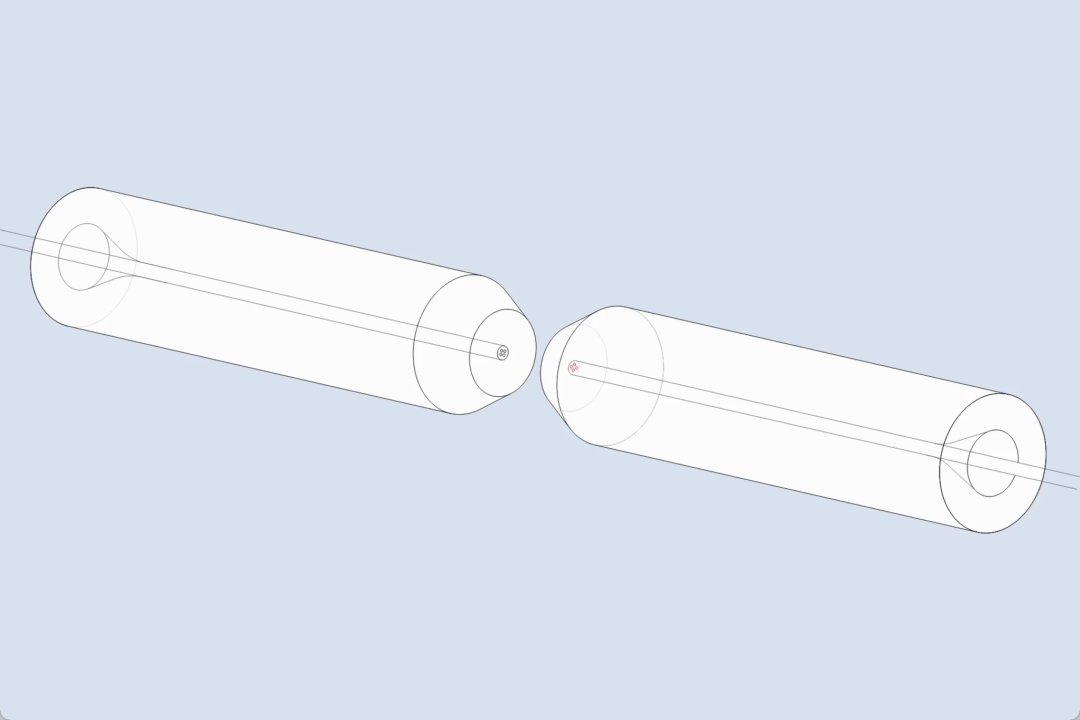
Research into improving transmission speed is also underway. Currently, optical signals reach the ONU and are then sent to the modem or router, which directs signals to the computers or other devices. In the future, it might be possible to connect optical fibers directly to computers.
Ever expanding applications of ferrules: Improving the safety of autonomous vehicles
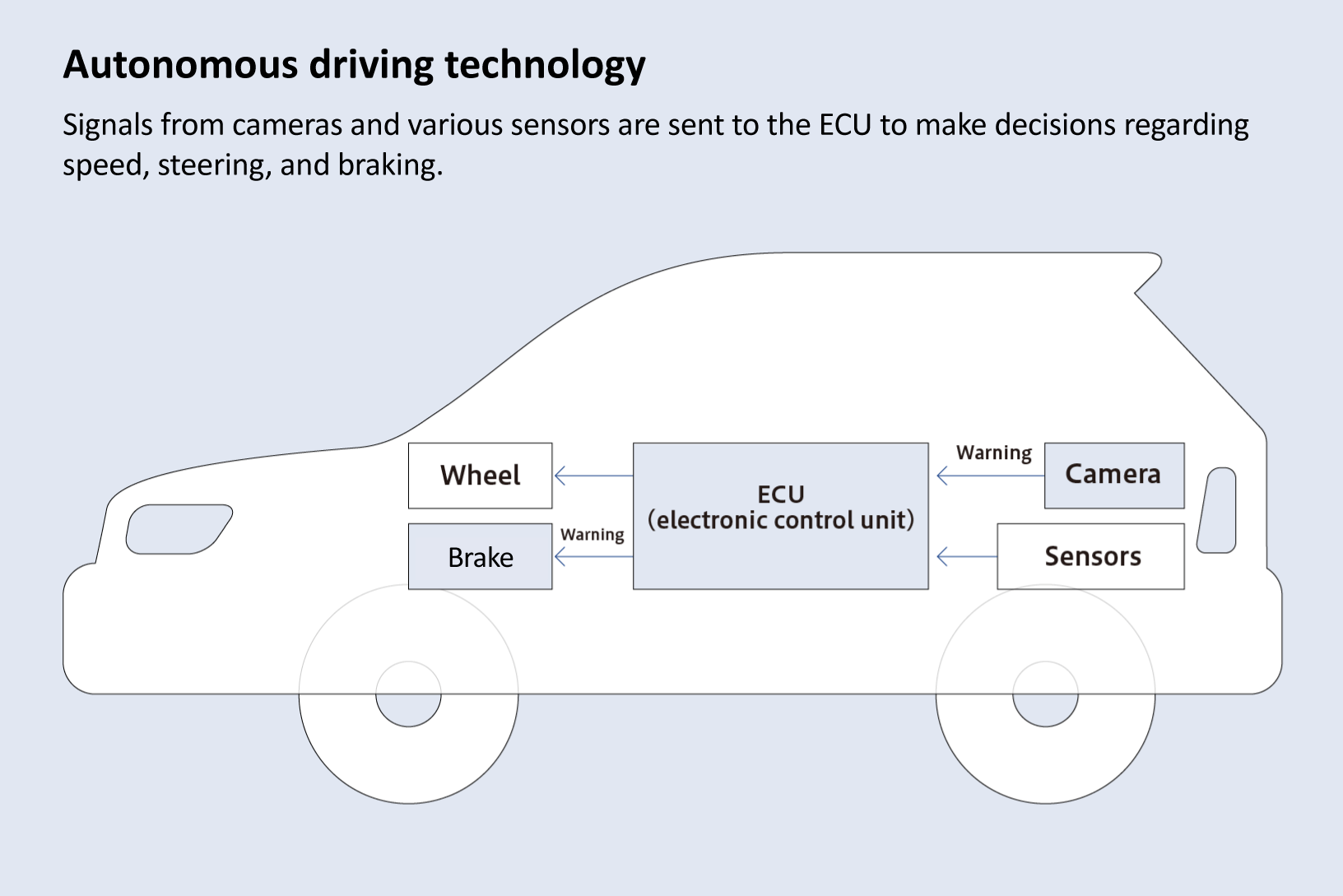
Autonomous driving technologies have advanced greatly in the last 20 years. Stakes are high, and all vehicle components must operate reliably in any condition to ensure absolute safety. Unlike climate-controlled data centers, vehicles require connections that can withstand extreme temperatures and vibrations. Cameras and sensors are connected to a central computer, which operates the steering wheel, brakes, and accelerator to safely navigate the vehicle. All these connections are currently made though electrical wires bound together in a wire harness, which can weigh over 100 kilograms. To increase data transmission speeds between the components, the use of fiber optics for vehicle applications is being researched. Switching from wire cable to optical fiber would also significantly reduce the weight of the vehicle. Adamant Namiki is participating in this field through industry-academia joint-research projects for products such as ferrules for in-vehicle applications.
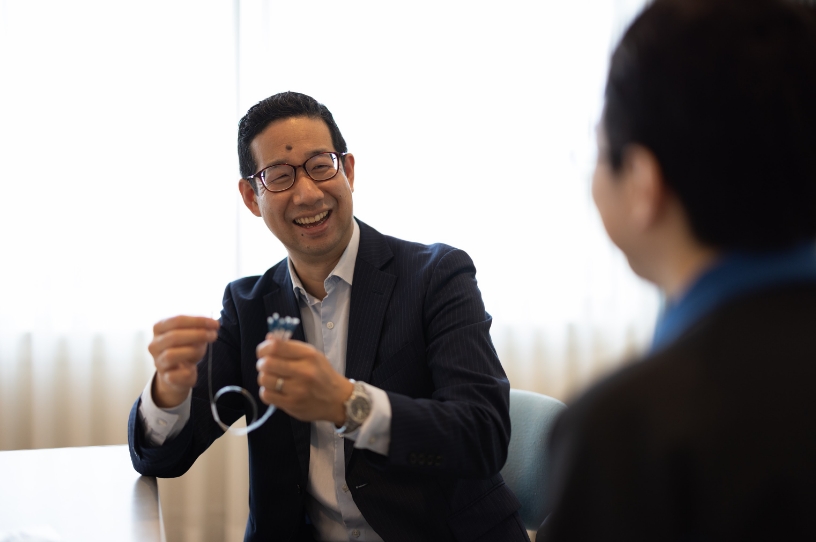
Although they may look small and simple, ferrules have been integral components for the expansion of high-speed internet and high-capacity communications over the past several decades, and Adamant Namiki has been one of the leading innovators. Adamant Namiki plans to continue this culture of leadership in the field by making use of the array of technological capabilities we have cultivated and by engaging in further research and development.