Bore Measuring Equipment
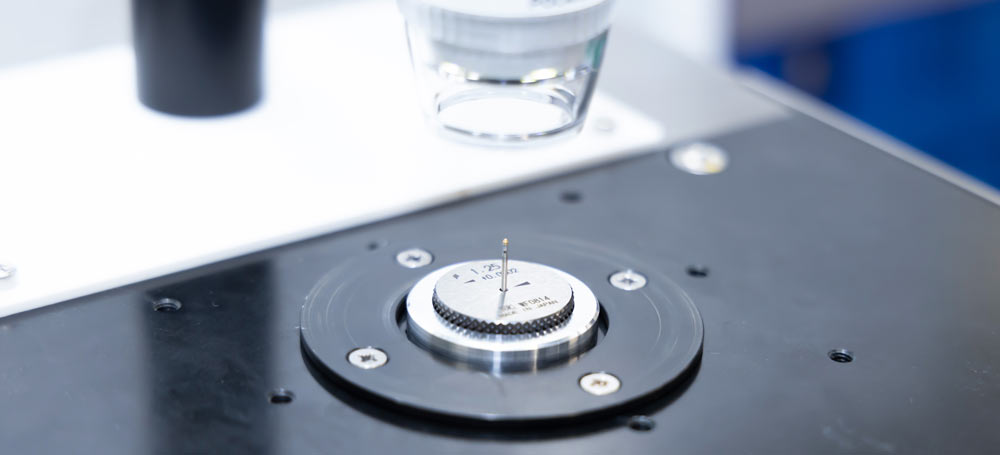
There are two methods for measuring the inner diameter of a hole: contact type and non-contact type.
Traditionally, measurements have been taken using contact-type products, such as pin gauges, caliper gauges, hole tests, and contact-type displacement sensors.
With this method, the guage head comes into contact with the inside of the hole. This may cause damage, so it is not suitable for measuring parts that require high-precision machining.
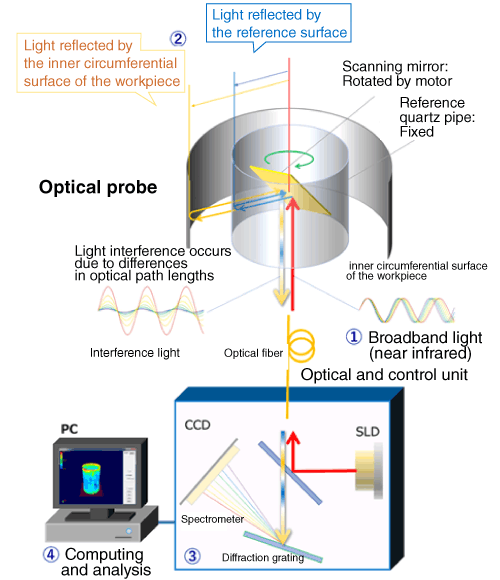
Non-contact methods of measurement use devices such as optical measuring microscopes or projectors to measure inside the hole.
These devices can only measure the inner edge of the hole, so they are not suitable for taking measurements deeping inside.
Instead, they are used for measuring holes drilled in thin objects, and for checking the shape of the ends of the hole.
For non-contact type measuring inside of the hole, air microsensors can be used.
With these, a stylus with a nozzle is inserted into the hole and the inner diameter measured based on changes in pressure.
Measurements such as mean bore diameter require multiple nozzles.
Optical sensors, such as laser displacement meters and optical interferometers, can be used for more accurate and stable measurement of inner diameter.
A probe to which the sensor is attached is inserted into the hole, and measuring is performed by rotating either the probe or the object itself.
By using an optical sensor, it is possible to take a wide range of measurements, including minimum/maximum inner diameter, and internal shape.
Orbray's optical inner wall precision measuring system negates the need for separate measurements on dedicated equipment. Our device is capable of non-contact, simultaneous measurement of inner diameter, roundness, roughness, and shape. Click here for more info.
-
The World’s Smallest Hollow Shaft Motor
-
Roundness and Cylindricity Measuring Machines
-
What is a Ferrule? : The history and development of the ferrule continues today with its ever pursuit of high accuracy of 1um or less at reduced costs
-
Visual Defect Inspection Equipment
-
What is our Optical Inner Wall Metrology System?