The advantages and characteristics of ceramic watches
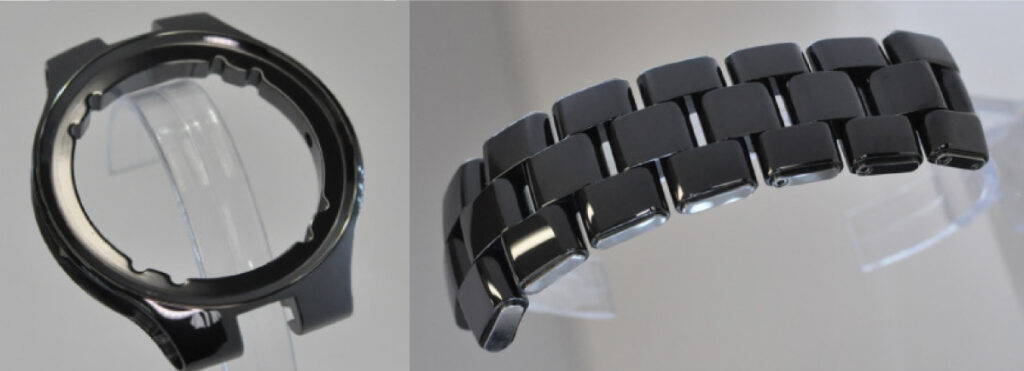
Ceramics are gaining popularity as a material for making watches. Foreign fashion brands have started making luxury watch casings and wrist bands out of ceramics. The popularity of such watches has increased dramatically in recent years, along with the range of products available.
Table of contents [close]
Ceramics are the perfect material for watches
The word “ceramic” comes from the ancient Greek “keramos,” which refers to objects that were made by hardening clay in a fire. Bowls and other pots have been made this way for millennia, and can be considered the first ceramics. Perhaps this is the material you imagined when you first read “ceramic watches.”
Modern ceramics are not made by just baking clay in ovens. For these advanced materials, refined nonferrous metallic powders such as zirconia and alumina are mixed in precise proportions with other ceramic materials, then sintered at very high temperatures. These are called “fine ceramics.” They are very hard and have a luxurious finish when polished. As with all ceramics, they are corrosion resistant and never rust. They are the perfect material for making watches.
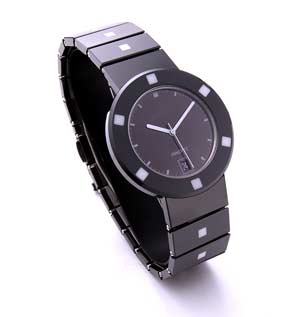
Ceramics started being used to make watches in the 1980s. Ceramics are difficult to manufacture and were used in a limited number of applications in the beginning. Production methods have improved over time, so that ceramics are now used in a wide range of products. Watch casings, wrist bands, and even internal parts can now be made from ceramics. Orbray’s ceramics have garnered significant attention for their use in watches offered by global fashion brands.
Advantages of using ceramics in watches
Ceramics are very hard and do not get scratched
With a Mohs hardness of 9, the hardness of ceramics is bested only by diamonds, the hardest material on Earth. On the Vickers scale, ceramics score 2300, compared with 200 for stainless steel (SUS304). When metallic watches are worn for a long time, they accumulate scratches, resulting in a used, tired look. Ceramics rarely get scratched, even if they experience strong impacts. Ceramics are also heat, corrosion, and wear resistant, and they have electric insulating properties. They will stay “like new” for a lifetime.
Ceramics can be polished to give a unique and lasting shine
Ceramics are not shiny right after sintering. However, if they are polished using the proper techniques, they become smooth and give off a beautiful luster. By making the most of their hardness and shine, ceramics have started to even be used in jewelry.
Ceramics can be made in a variety of colors
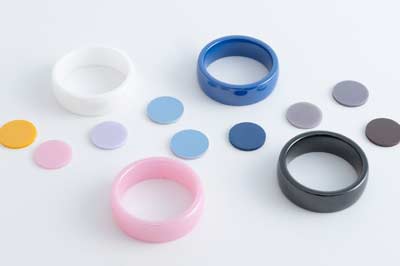
Ceramics can be made in a wide variety of colors by doping the raw materials with additives (colored zirconia). In addition to the classic black and white, colors such as pink, yellow, red, blue, and many other colors can be added. The colors can be subdued and gentle, or vivid and striking. With the proper mixing technique, patterns, such as marbling, can also be created.
Ceramics are gentle on the skin (hypoallergenic)
Ceramics do not corrode and do not cause allergic reactions. Therefore, they are often used in dentures and artificial bones. People with sensitive skin or allergies to metals can wear ceramic watches and jewelry comfortably.
Ceramic production process
Alumina, zirconia, reinforced alumina (alumina with zirconia additive), silicon nitride, silicon carbide, and aluminum nitride are some of the raw materials for making ceramics. The production process is as follows:
- Ceramic powders, binders, sintering aids, and reinforcing compounds are carefully measured and blended.
- The mixture is kneaded.
- The kneaded powder is shaped in a mold.
- The molded ceramic is sintered.
- The hardened ceramic is polished.
As ceramics are sintered after creating the desired shape in a mold, complex shapes can be made. Shapes that are difficult to make with metals can be made with ceramics that are harder and lighter than metals.
One difficulty in manufacturing ceramics is that the product shrinks during the sintering process. To account for this, during the prototyping process, the sintering process is repeated many times to thoroughly examine the shrinkage rate to ensure a uniform and accurate product. After sintering, the piece must be polished. Since it has a hardness second only to diamond, polishing ceramics precisely requires experience and advanced craftsmanship. Multiple polishing methods are used to produce high-precision ceramic products.
Mechanical processing of ceramics takes full advantage of diamond tools and uses multiple methods before reaching the final polishing step. The polished surface of a watch case must be not only practical, it must also be beautiful.
Bringing out the unique luster of ceramics to meet the exacting demands of luxury watches requires deep understanding of the special characteristics of ceramics, and the effective utilization of techniques cultivated through many years of working with the material.
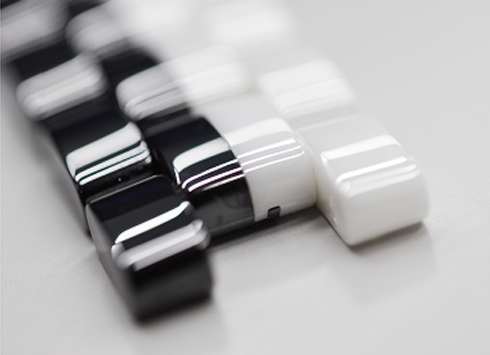
Orbray has been working with ceramic watches since the 1980s. In the beginning, we were one of only a few companies making watch parts out of ceramics. Black was the only color available at that time. It was not until several years later that color variations were available. White ceramic watches had the look and feel of pearls. This was much more desirable that plastic watches. White was also a color that was rare for watches at that time. These characteristic made them extremely popular with women, and sales of ceramic watches exploded.
Orbray’s ceramic watch components have been used for many years by top international fashion brands. Please feel free to contact us to provide sophisticated ceramic watches made in colors and shapes that meet your needs.
We provide watch cases and bands made of fine ceramic, which has gained attention as a hard material.
-
Metallic Glass Features and Applications of a New Type of Metallic Alloy
-
Introduction to winding nozzles: an essential component of the motor coil winding process
-
Watch glass [Story of Watch 2]
-
Dispenser Nozzles: Applications for dispensing liquids and selecting the right one
-
Pioneering the Future of Multi-Core Optical Fiber Connections : Orbray's Optical Fiber Bundling and Light-Induced Self-Written Optical Waveguide Technology
-
Hard materials and cemented carbides: Characteristics and processing methods