Introduction to winding nozzles: an essential component of the motor coil winding process
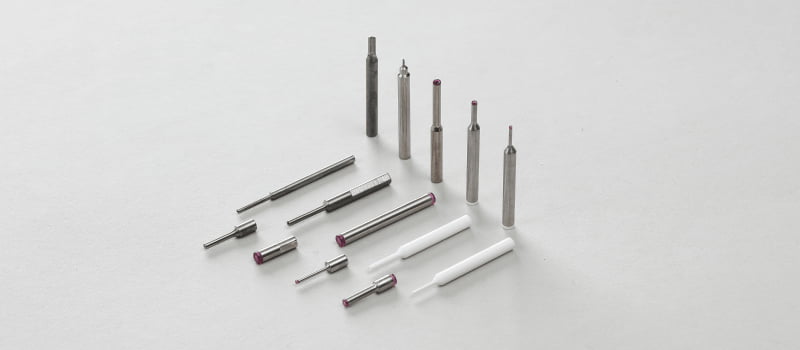
Electric motors are found all around us in our modern world, from cars to home appliances, and office equipment to industrial machines. Motors use coils which are made by winding a wire coated with an insulating film. Demand for high-performance, powerful motors has increased in recent years, mainly due to the growing popularity of electric vehicles. This has in turn increased demand for the production of coils with much higher quality and performance than ever before.
Winding nozzles are an essential component when producing motors that use coils. In order to wind high-quality, high-performance coils, the winding nozzles must be very precise, durable, and resistant to wear and tear.
Table of contents [close]
What are winding nozzles?
Coils are made by tightly and evenly winding metal wire such as copper or aluminum that has been treated with an insulating coating. This coiled wire has useful electrical characteristics, such as generating a magnetic field when electrified and, conversely, producing an electric current when the magnetic field around the coil is changed. Electric motors use these characteristics to convert electric energy into rotational, axial, and vibrational kinetic energy.
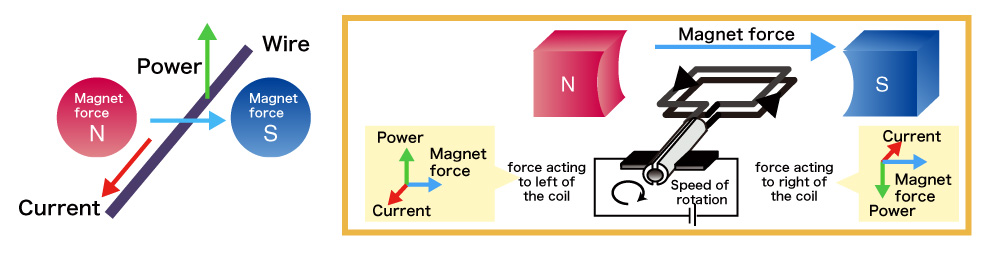
There are different types of motors depending on their structure and the principle of operation.
Brushed motor
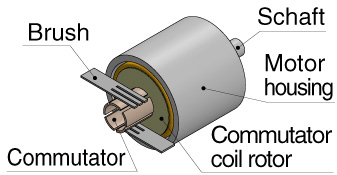
A brushed motor rotates by switching the flow of electricity through the coil using a commutator. The commutator contacts the coil using soft conductive materials called brushes. A brushed motor does not require drive circuits, is easy to control, and has good responsiveness. However, since the brushes and commutator are in physical contact with each other, they wear down over time, leading to shortened service life. In addition, when the contact point with the commutator changes, electrical noise due to sparks and other noise from friction often occur.
Brushed coreless motors (DC coreless motors)
A brushed coreless motor is a motor in which a cup-shaped rotor made of copper wire rotates around a cylindrical magnet placed in its center. Because the rotor does not have an iron core, it is light, has a small moment of inertia, and has excellent responsiveness and acceleration. In addition, vibration (cogging) due to attractive action from the magnet does not occur, so rotation is smooth and there is less vibration and noise.
Brushless motor
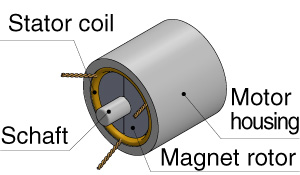
A brushless motor uses a drive circuit to precisely control the current flowing through the coil in order to rotate the magnet located inside the coil. Some coils have no core, while others are wound around a core made of materials such as iron. Since there is no brush, there is little wear and tear, leading to long service life. In addition, large currents can be used to drive the motor since there are no physical contacts. A dedicated control circuit is required for driving.
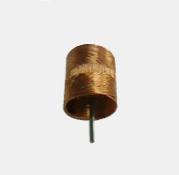
The coil (winding) is a foundational element of motors. The performance of the coil depends on several factors; in addition to the types of metals that are used, the winding machine and winding nozzle have significant influence on the final product. The wires are wound using a coil winding machine, and the winding nozzle is a vital component of this machine. It sends out the wire for the core and plays a vital role in determining the final quality of the motor. The winding machine sends the metal wire from the wire reel to the winding nozzle via a bearing roller (winding guide). The wire passing through the winding nozzle is wound into the coil, either by rotating the nozzle around the core, or by rotating the core itself. By precisely controlling the pitch and tension of the wire, the winding machine can wind coils very finely and evenly. The denser the winding, the stronger the magnetic field produced, resulting in a more powerful motor.
Durability and wear resistance required for winding nozzles
The performance of the coil varies greatly depending on how the metal wire is wound. Uniform, high density winding is of utmost importance for high performance. The winding machine must apply high tension to the metal wire to achieve this. It must also send out the metal wires faster and wind them at higher speeds in order to meet productivity demands.
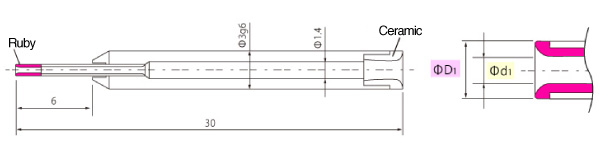
For these reasons, a strong force is always applied to the winding nozzle by the metal wire, and a high frictional force is generated between the nozzle and the wire, leading to wear and tear such as scratches and bends in the tip of the nozzle. Winding with a worn or bent winding nozzle can cause the metal wire to break or be wound incorrectly, resulting in serious product defects. In addition, a worn out nozzle can cause pinholes or scratches on the insulating coating of the wire, which can lead to a decrease in the motor’s output as well as other serious issues. Manufacture of winding nozzles requires advanced capabilities, from material selection to processing technology. The winding nozzle needs to be able to hold up against strong and constant frictional forces. It must be made of an extremely hard material that has excellent durability and wear resistance and low frictional resistance. It is also important that the R shape of the entrance and exit of the winding nozzle, as well as the surface roughness inside the hole, is processed more smoothly in order to reduce frictional force. Furthermore, in order to accurately feed the metal wire, the nozzle hole must also have high accuracy.
Types and characteristics of winding nozzles
There are three main types of materials used in winding nozzles: ruby, ceramic, and carbide.
Ruby winding nozzles
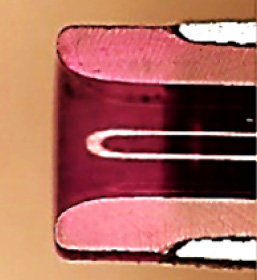
Ruby winding nozzles use rubies at the outlet end or at both the inlet and outlet ends of the nozzle. Ruby is the second hardest material on Earth, next only to diamond. It has excellent durability and abrasion resistance, and can be continuously used for long periods of time. It also has little frictional resistance, allowing the metal wire to be fed smoothly without being damaged during winding. These favorable characteristics last over time, with minimal occurrence of breakage, pinholes, scratches, etc. Ruby nozzles can be used for ultra-fine wires, but advanced processing technology is required to form the fine and smooth holes and R-shapes necessary.
Ceramic winding nozzles
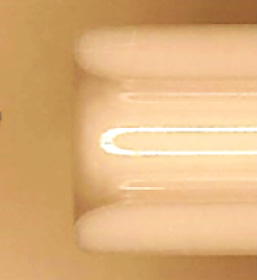
Ceramic winding nozzles are made entirely of ceramic materials. High quality ceramic materials have wear resistance characteristics similar to ruby. Orbray’s precision molding and processing technology makes it possible to form the fine holes and smooth R-shapes required in the nozzles.
Hard metal winding nozzles
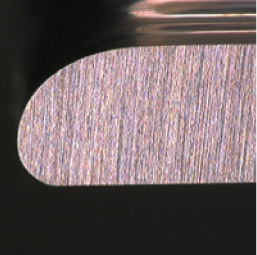
Hard metal winding nozzles are made of cemented carbide. By selecting fine-particle cemented carbide materials, high surface accuracy and durability can be achieved. These nozzles are often used for high tension winding and winding of thick wires.
Comparison of each nozzle type
Properties | Ruby nozzles | Ceramic nozzles | Carbide nozzles |
Force / load on the coil | ○ | ○ | △ |
Abrasion resistance | ○ | ○ | △ |
Ultra-fine wires | ○ | △ | ○ |
Thick wires | △ | △ | ○ |
Ease of threading coil | △ | ○ | ○ |
Suitable for special applications | ○ | △ | ○ |
More information of Orbray's winding nozzle:
-
What are Audio isolation feet? Overview and Effects
-
What is a Ferrule? : The history and development of the ferrule continues today with its ever pursuit of high accuracy of 1um or less at reduced costs
-
Production of Sapphire
-
TIME Asia interviewed President Riyako Namiki
-
Introducing Bioceramics: Challenges, features, and applications
-
The Bright Future Being Created by Diamonds