光実装技術(ダイボンディング/ワイヤーボンディング)

光学素子、電子部品、MEMS等の微小部品の実装とは
トランジスタや抵抗、IC、半導体レーザー、フォトダイオードなどの各種電子部品、光学素子は、それぞれの機能を満たすように装置や基板上に実装されます。特に、光学的に機能させる必要のある光学素子の実装やMEMS等の微小部品の実装は、高精度の位置決め精度が求められるため、高い技術や特殊な装置が必要となります。
挿入実装と表面実装
電子部品をプリント基板にはんだ付けなどにより取り付け、電子回路を形成することを基板実装といいます。基板実装には、挿入実装と表面実装の2種類があります。電子部品から出ている金属端子(リード線)を基板に開けられた穴(スルーホール)に挿入してはんだ付けを行う方法が挿入実装です。リード線の形を整えて(カット・フォーミング加工)スルーホールにセットし、溶かしたはんだを入れた槽の上を基板が通る際にスルーホールにはんだを流しこんで固定します(フローソルダリング)。挿入実装は、部品の接続強度が比較的高く、人の手による部品挿入、はんだ付けも可能です
表面実装は、プリント基板の表面に電子部品を直接はんだ付けします。非常に微細な電子部品もはんだ付けできるので、挿入実装よりも高密度の実装が可能です。表面実装では、部品が取り付けられる位置に穴を空けたマスクを用いて、基板上にペースト状のはんだをあらかじめ塗布します。はんだを塗布したら、プリント基板に取り付ける電子部品を設置します微細な部品は人の手で取り付けることが難しくなるため、チップマウンターなどにより正確に位置決めされて取り付けられます。部品を取り付けた後、リフロー炉で加熱することではんだを溶融させて部品取り付けます。
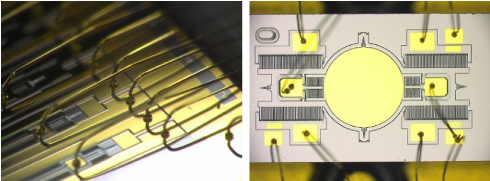
近年、電子機器の小型、薄型化により、電子部品は非常に小さくなり、加えて高密度の基板実装が求められるようになりました。挿入実装では、プリント基板の強度確保でスルーホール間にある程度距離が必要となるため、高密度の実装が困難です。そのため、高密度実装が可能な表面実装が多くを占めるようになっています。
高精度が求められる光実装技術とは
半導体レーザー、フォトダイオード、レンズ、光導波路、光ファイバーなどの光学素子を、光学的に機能するように基板上に取り付けることを光実装と言います。光実装では、電子回路からの電気信号を光信号に変換して送信するため、電子部品と接続されるとともに、光学素子間で光信号を受送信できるように回路を形成する必要があります。
半導体レーザーなどの半導体デバイスのチップ(ダイ)は、電気を通すためのリードフレームと電気的に接続するため、リードフレームが組み込まれたケースに固定されます。チップの固定では、はんだ、Agペースト、UV接着などの接合材料を塗布して固定するダイボンディングと、リードフレームとチップを金などのワイヤーで接続するワイヤーボンディングがあります。ダイボンディング、ワイヤーボンディング後のチップは、気密封止され、光学素子として基板上に実装されます。
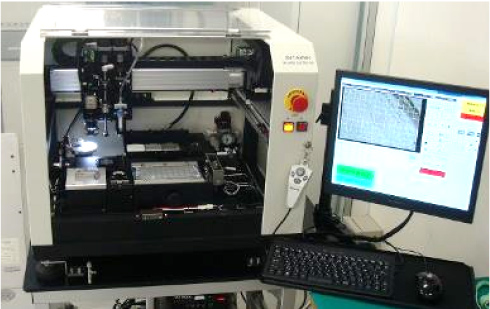
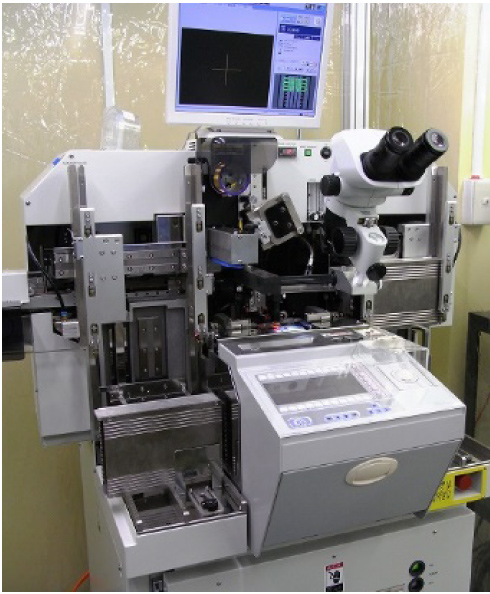
光学素子は、電子機器の小型、薄型化が進むことで、電子部品と同様に非常に小さくなっています。そのため、チップも微細になり、ダイボンディング、ワイヤーボンディングによる実装では、より高い精度と再現性が求められるようになってきました。
また光実装では、電子部品の実装とは異なり、接続されているだけでは反射や軸ずれにより光信号を上手く伝達することができない場合があります。光学的に機能するように、正確に位置や軸を合わせることや、反射損失を低減させる処理が必要です。
求められる正確な位置決めと高い再現性
光学素子や、微小な電子部品、MEMS等の微小部品の実装には、高い技術や特殊な装置が必要です。近年の電子機器の高機能化により、光学素子、電子部品は肉眼でははっきり見えないほど微小になってきました。また、電子機器内にジャイロやマイクロスイッチのような、MEMS技術により形成されたパーツも多く用いられるようになっています。
これらの部品を高密度で基板実装するには、正確な位置決めを高い再現性で実現する必要があります。高密度の実装では、部品点数が多く、他の部品との距離も近くなるため、他との干渉などがないように、高速に連続で搬送しなければなりません。また光実装では、光信号の損失や反射の影響を抑えるため、光路を最適に配置する必要があり、光学素子自体が非常に高い寸法精度で製造されているため、求められる位置決め精度もその分高くなります。より、高度な位置合わせが必要です。
お問い合わせは下記フォームに入力し、確認ボタンを押して下さい。
※お問い合わせフォームからのセールス等はお断りいたします。送信いただいても対応いたしかねます。