Bionic (Prosthetic) Hands and Micro-motors
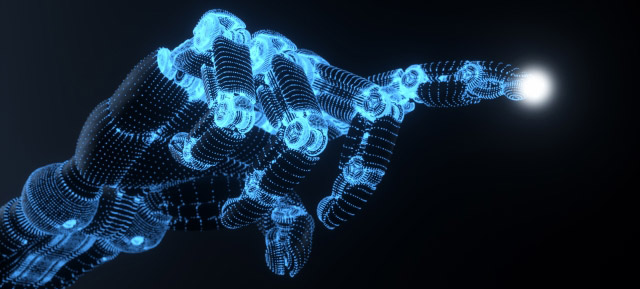
In the 1970s, an American TV drama entitled “The Six Million Dollar Man” became a huge hit. It was a fictional story about Colonel Steve Austin, a NASA astronaut, who was seriously injured in a space flight accident which left him blind in one eye, and paralyzed in his right arm and both legs.
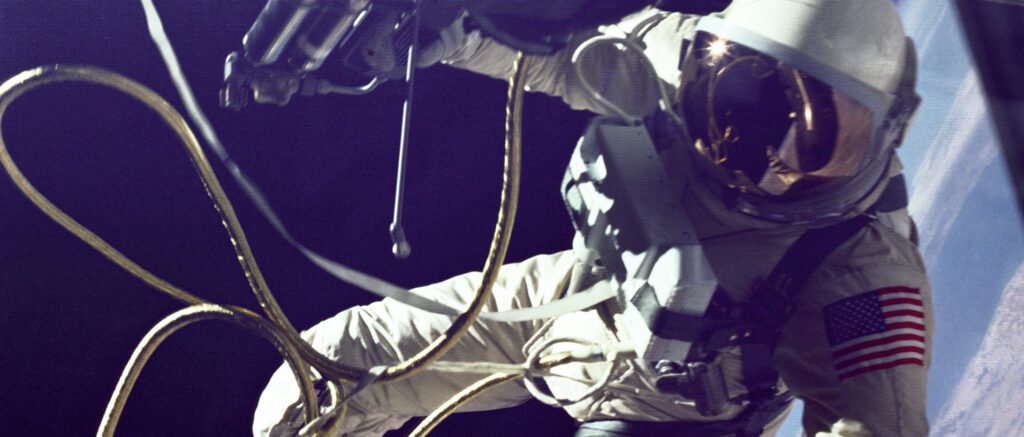
The injured areas were restored with bionic body parts which gave Colonel Austin extraordinary abilities. The surgery cost six million dollars, the namesake of the TV show, equivalent to almost 42 million dollars today.
As time has advanced, so has technology. Bionic prosthetics are no longer rare, and costs have decreased significantly. Therefore, although still not perfect, more people than ever who have lost limbs or function in their limbs have access to bionic prosthetics to help them regain function.
This is especially true of the hands. Loss of function of the hands can have significant negative effects on a person’s quality of life. Prosthetic devices such as bionic hands can mimic normal hand functions and can form the foundation for physical and mental recovery.
Table of contents [close]
Customized Devices
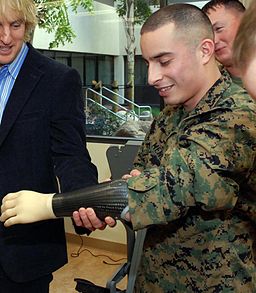
Prosthetics for complex structures (such as bionic hands) need to be customized to the specific needs and characteristics of each patient. Good prosthetics are reliable and replicate tactile movements well. Bionic hands typically weigh 400 to 600 grams. This is similar to that of a typical human hand. They are controlled by myoelectrical signals and other small electrical signals produced by muscle contractions in the patient’s body. The electrical signals can be measured by sensors on the surface of the skin, similar to electrocardiograms used in cardiac diagnoses. Electrodes installed in the prosthetics detect the myoelectrical signals and transmit them to the control board where the signals are amplified and sent to activate five small motors (one for each digit) to move the fingers and thumb to open and close the hand. The strength of the muscle contraction controls the speed and strength of the grip. A weak contraction would send a weak signal and cause a slow motion. A strong contraction would cause a fast motion. Each finger of the prosthetic hand is equipped with its own motor for very precise control. The four motors for the fingers are located in the palm of the hand, while the fifth motor is located in the thumb. Each motor is equipped with an encoder to accurately detect the position of the fingers at any time.
Micro-motors
DC coreless micromotors are used in bionic hands because they are lightweight, durable, small, and have a high output/volume ratio. In addition, they are very energy efficient, allowing the prosthetic to be used for several days between charges.
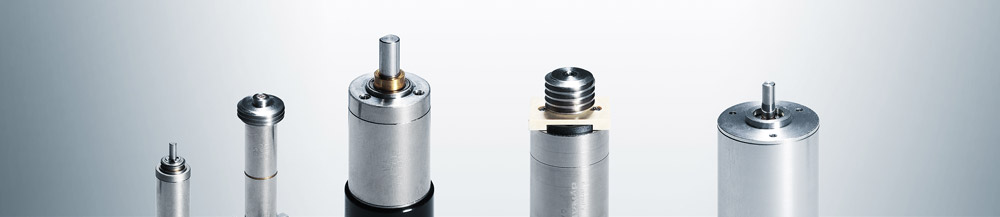
Research and development of prosthetic hands is ongoing to provide users with more advanced features, including control of each individual finger and transmission of sensations. With such control, actions such as picking up flat objects, operating remotes, typing, carrying certain objects, and holding eye glasses can become possible.
Achieving quick, accurate movements of the hand and fingers has been a major challenge in the past. However, the current state of the research is quite advanced. There are two types of sensors that can be incorporated into prosthetics: the position sensor and the tactile sensor. Position sensors provide proprioceptive data and tactile sensors provide pressure and tactile data. Both types of data are fed back to the brain through the nervous system. There are several types of prosthetics, and while functional prosthetics are currently the type often used in Japan, the use of myoelectric prosthetics is expected to increase in the near future.
-
What is a collaborative robot? An introduction to the functions and performance of collaborative robots
-
Small Motors: Applications and Required Technology
-
The World’s Smallest Hollow Shaft Motor
-
Small Servo Motor for Robot Joints
-
Micro Mechanism
-
Brushless motor vs brushed motor: The features of the Orbray brushless motor.