Classification, features, and applications of pumps
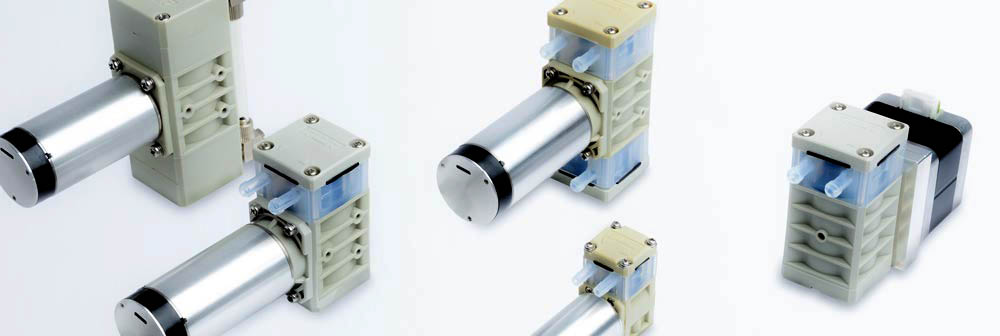
There are various types of pumps, depending on their operating principle, structure, etc. A diaphragm pump is a special type of pump for moving liquids and gases.
Table of contents [close]
What is a positive displacement pump?
A positive displacement pump is a pump in which fluid in a fixed-volume space is transferred by changing that volume using reciprocal or rotational motion.
For example, in pumps that use reciprocal motion, a piston or rod-shaped plunger is combined with two valves. The volume in the pump chamber is changed by the reciprocating motion of the piston or plunger to convey fluid.
Another type of pump is a diaphragm pump, which conveys fluid by changing the volume of the pump chamber through the motion of an elastic diaphragm.
Pumps that use rotary motion include gear pumps and screw pumps which move fluid by guiding it between the meshed teeth of rotating gears or screws.
Tube pumps, which move fluid in a tube by using rotating rollers to squeeze the tube, are also classified as positive displacement pumps.
Apart from these, there are also non-positive displacement pumps that use a rotating impeller, creating centrifugal force that moves fluid by applying pressure and creating an axial flow.
Pulsation of a positive displacement pump
In a positive displacement pump, the suction and discharge phases occur alternately, causing a pulse-like delivery of the fluid. This is called pulsation. However, if the vibrations from the pulsation are strong enough, they can damage the pump and piping, causing them to degrade quickly. To mitigate the effects of pulsation, multiple pistons or plungers with opposing suction/discharge timing can be used to cancel out the vibrations. Air chambers or accumulators that act to absorb the vibrations can also be used to reduce the impact of pulsation in the system.
Features and applications of various pumps
This section explains the structure and features of each type of pump.
Piston pump
The piston pump is a pump that sucks in and transfers fluid by a reciprocating piston in a cylinder.
Along with the piston, there are two valves: one on the intake side and one on the discharge side. The piston has a seal to prevent fluid from leaking out between the piston and the cylinder.
The operating principle is that when the piston moves in one direction, the valve on the discharge side closes while the valve on the intake side opens, sucking fluid into the chamber.
Next, when the piston moves in the opposite direction, the valve on the intake side closes, and the valve on the discharge side opens, discharging the fluid.
By repeating this process, movement of the fluid continues. Piston pumps are used for operations such as pumping well water.
Diaphragm pump
The diaphragm pump sucks in and transfers fluid by changing the volume in the chamber using the push-and-pull motion of a diaphragm.
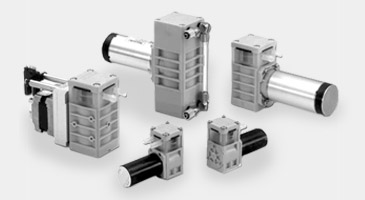
In addition to the diaphragm, it also has check valves on the suction side and the discharge side. The diaphragm is moved by air, hydraulics, a motor, a solenoid, etc.
First, the diaphragm is pulled to increase the volume in the chamber and reduce the pressure.
This causes, the check valve on the discharge side to be pulled shut, while the check valve on the suction side is pulled open, allowing fluid to be sucked into the chamber.
The diaphragm is then pressed, which increases the pressure in the chamber.
This pushes the check valve on the discharge side open, allowing the fluid to be discharged, while the check valve on the suction side closes.
Volumes of fluid continue to be conveyed through the repetition of this suction and extrusion operation.
The diaphragm is commonly made of a durable, highly elastic material such as rubber, while the inside surface of the chamber, which comes into contact with the fluid, is made from chemical- and corrosion-resistant material such as silicon resin or Teflon.
A diaphragm pump is simple in construction and easy to take care of, and the amount of fluid moved is easy to measure, so this type of pump is used to transport a wide variety of fluids in addition to ordinary gases and liquids.
See Orbray's diaphragm pump lineup
diaphragm pump is also discussed in the following article:
What is a diaphragm pump? The features and structure explained
Plunger pump
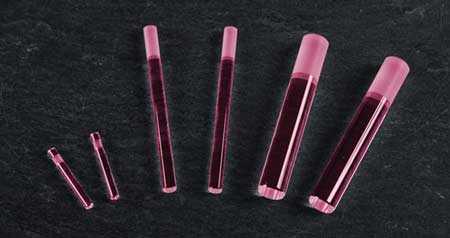
Like a piston pump, a plunger pump sucks in and transfers fluid using the reciprocating movement of a plunger.
It has a plunger, an inlet valve, and an output valve.
Plunger pumps differ from piston pumps in that the seal is stationary inside the pump body rather than on the plunger.
Plunger pumps are suitable for high-pressure fluid transport, and are also used in high-pressure washers.
Gear pump, screw pump

Gear pumps and screw pumps are pumps that suck in and convey fluid by engaging and rotating gears and screws.
For example, in a gear pump that uses two external gears, the fluid is sucked in by the negative pressure generated when the gears mesh with each other.
Fluid that enters between the teeth of the gear is conveyed along the inner wall of the case to the discharge side, and when the gear engages again, the fluid is pushed out and discharged.
These pumps have a powerful conveyance force, and are used for hydraulic equipment and high-viscosity liquids.
Tube pump
The tube pump sucks in and transfers fluid by squeezing a flexible tube with a rotating roller.
Negative pressure is generated when the roller continuously squeezes the tube and rotates, and fluid is sucked in.
The fluid is then pushed by the roller and discharged.
Fluid can be dispensed at a fixed rate under constant pressure, so tube pumps are used in applications such as medical equipment and chemical transport.
AC pumps, DC pumps, large pumps, small pumps
Aside from their operating principle and structure, pumps are sometimes classified as AC or DC pumps, according to the type of power supply used for the motor or solenoid.
In a diaphragm pump, the motor driving the cam or crank to push and pull the diaphragm can be either an AC or a DC motor, so the pump can be classified as an AC pump or a DC pump based on this.
In Japan, since the frequency (Hertz) of AC power supply varies across regions, AC pumps tend to differ in performance depending on the region, so they are made to be robust and durable.
DC pumps are often used in medical and laboratory equipment because of their low amount of noise, heat generation, and vibration, as well as their ease of speed adjustment.
Pumps may also be classified as large or small pumps depending on their physical size as well as their capacity, which is determined by factors such as flow rate (the amount of fluid the pump can take in and discharge in a certain period of time), and pump head (a measure of vertical pumping height based on how much pressure, velocity, etc., the pump can apply to the fluid).
Most large pumps are non-positive displacement pumps such as centrifugal and axial flow pumps. They are often used in places requiring large-capacity conveyance, such as water supply, sewerage, river drainage, and liquid feed in production plants.
Small pumps usually operate through positive displacement and include the diaphragm pump, plunger pump, and tube pump, They are mainly used in applications requiring constant pressure and delivery.
Small pumps use precision-made check valves and cylinders, along with small, lightweight, high-efficiency motors as the driving source, making stable delivery of fixed amounts of fluid possible.
They are widely used in industrial applications for air and liquid conveyance to various precision instruments, as well as in environmental analysis, medical care, biotechnology, food production, and other applications that require the delivery of fluids at a fixed amount and speed.
-
What is a collaborative robot? An introduction to the functions and performance of collaborative robots
-
Robotic Hands
-
Brushless motor vs brushed motor: The features of the Orbray brushless motor.
-
The Story of Motor - Rule, principle and history -
-
What are End Effectors?
-
Servo-drivers: How they are made and how they are used