What is a diaphragm pump? The features and structure explained
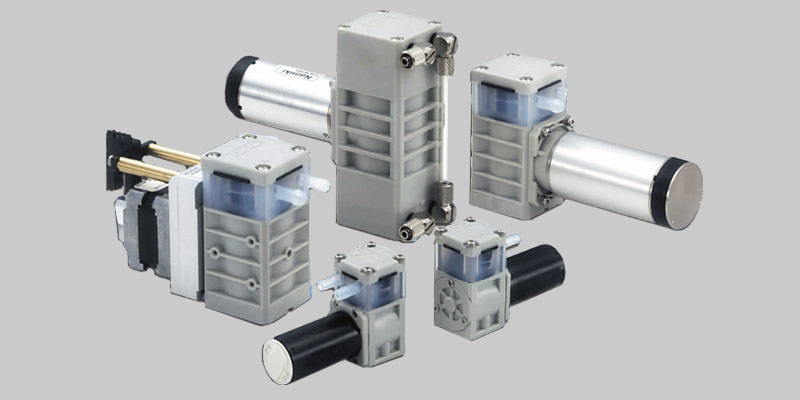
There are various types of pumps used to convey fluid, depending on structure and the principle of fluid transport.
The diaphragm pump is one of them.
Diaphragm pump have a simple structure, are easy to handle, and are used in a wide range of fields.
Table of contents [close]
Types of pumps
Pumps can be broadly classified into three types: positive displacement, non-positive displacement, and special types.
Non-positive
displacement pump
Spiral pump
Diffuser pump
Axial flow pump
Mixed flow pump
Special pump
Cascade pump
Positive displacement pump
- Air-driven diaphragm pump
- Hydraulic diaphragm pump
- Direct drive diaphragm pump
Plunger pump
Piston pump
Bellows pump
Gear pump
Rotary pump
Screw pump
A positive displacement pump is a pump in which fluid in a fixed-volume space is transfered by changing its volume using reciprocal or rotational motion.
In non-positive displacement pumps, a rotating impeller creates centrifugal force, which conveys fluid by applying pressure and creating an axial flow.
Special type pumps convey fluid using force of air or gravity.
Diaphragm pump is classified as positive displacement pumps.
Fluid is transported by changing the volume in the chamber where one surface is separated by an elastic diaphragm.
In addition to diaphragm pump, positive displacement pumps also include plunger pumps that reciprocate a plunger to transfer fluid like a syringe, piston pumps that pump well water, and gear pumps that deliver fluid using gear rotation.
Positive displacement pumps have good quantitativeness and are suitable for ensuring a fixed flow rate at regular intervals, and the amount of fluid that can be drawn up (lift) and conveyed is also relatively large.
Non-positive displacement pumps include spiral pumps that apply radial pressure using swirl blades and centrifugal force, and axial flow pumps that convey liquid in the axial direction.
Since the power of the pump itself to suck up the fluid is weak, it is necessary to fill the pump with fluid (priming) before driving.
The high-speed rotation of the impeller enables relatively continuous conveyance at a high flow rate.
Principle, structure, and application of diaphragm pump
The diaphragm pump has a structure as shown in the figure below.
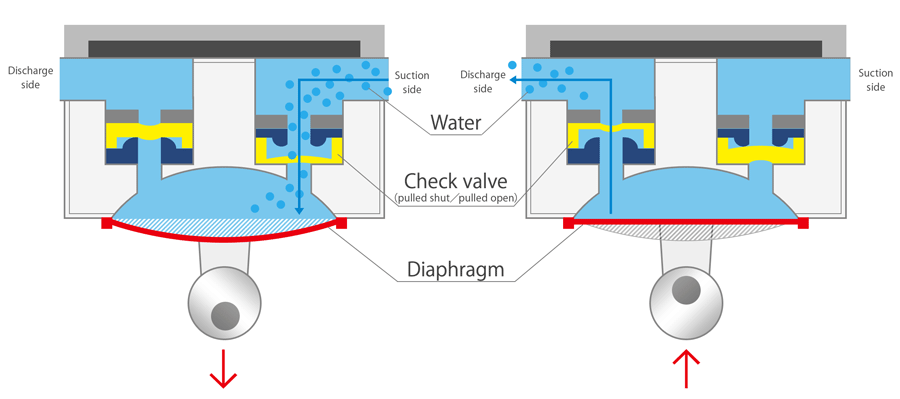
First, the diaphragm is pulled to increase the volume in the chamber and reduce the pressure.
At this time, the check valve on the discharge side is pulled shut, while the check valve on the suction side is pulled open, allowing fluid to be sucked into the chamber.
Then, the pressure in the chamber is increased by pressing the diaphragm.
The check valve on the discharge side is pushed open, the check valve on the suction side closes, and the fluid is pushed out from the discharge side.
The fluid is conveyed through the repetition of this suction and extrusion operation.
Rubber, which is durable and highly elastic, is often used as the material for the diaphragm, while materials with excellent corrosion resistance and chemical resistance are used on the chamber-side surfaces which come into contact with fluids.
Similarly, the pump head and check valve use materials such as resin or stainless steel depending on the type of fluid being handled.
This allows the diaphragm pump to carry a wide range of fluids in addition to air and water.
In addition to air-driven pumps that use compressed air, there are various types of diaphragm pump available based on the power source used to push and pull the diaphragm, such as hydraulic, motor, and solenoid-driven pumps.
Fluid conveyed by the diaphragm pump flows intermittently at regular intervals (pulsation) as suction and discharge are repeated.
By changing the size and speed of the reciprocating movement, it is possible to change the amount of fluid transported and the speed at which it is moved.
While not suitable for handling continuous flow of large volumes, as in the case of drainage systems, diaphragm pump can carry a stable amount of fluid at regular intervals, and do not change the properties of the fluid.
Therefore, they are often used for transporting various chemicals, for example as lightweight, compact chemical injection pumps in the medical field.
In addition, they are used in a wide range of other fields, including life sciences and new manufacturing processes, and in the latest equipment for the next generation, such as cell-separation equipment, 3D printers, and commercial printers.
Diaphragm pump characteristics and precautions
When using a diaphragm pump, there are some points to note in terms of the characteristics.
Diaphragm pumps use check valves that alternate between suction and discharge based on the movement of the diaphragm to convey fluid. If foreign matter accumulates near a check valve, it may obstruct the valve seal, disrupting suction and or discharge of the fluid and the pump's performance may deteriorate. In some cases, flushing with water or other fluids may dislodge the obstruction, restoring the valve seal and pump performance. Scratches and other damage can also cause inadequate sealing of the check valve, causing loss in performance. Therefore, check valves must be kept in good condition.
In addition, since diaphragm pumps create flow by pushing fluid out of the chamber one stroke at a time, if there is a clog or other obstruction on the downstream pipe, pressure will increase in the chamber. Even if the outlet is completely closed (dead head condition) and the check valve is not moving, the pressure in the chamber will increase to the diaphragm actuating power. If flow is impaired by clogging in the discharge pipes, and even if the check valve can't move, pressure will increase on the power that moves the diaphragm. This can cause weak parts in the pump or pipes to burst, or damage to drive devices such as motors and pistons. To avoid such accidents, it is important to install safety valves (relief valves) that relieve pressure and safety switches that detect overload and stop operation.