What are smart factories? The benefits of introducing IoT in factories.
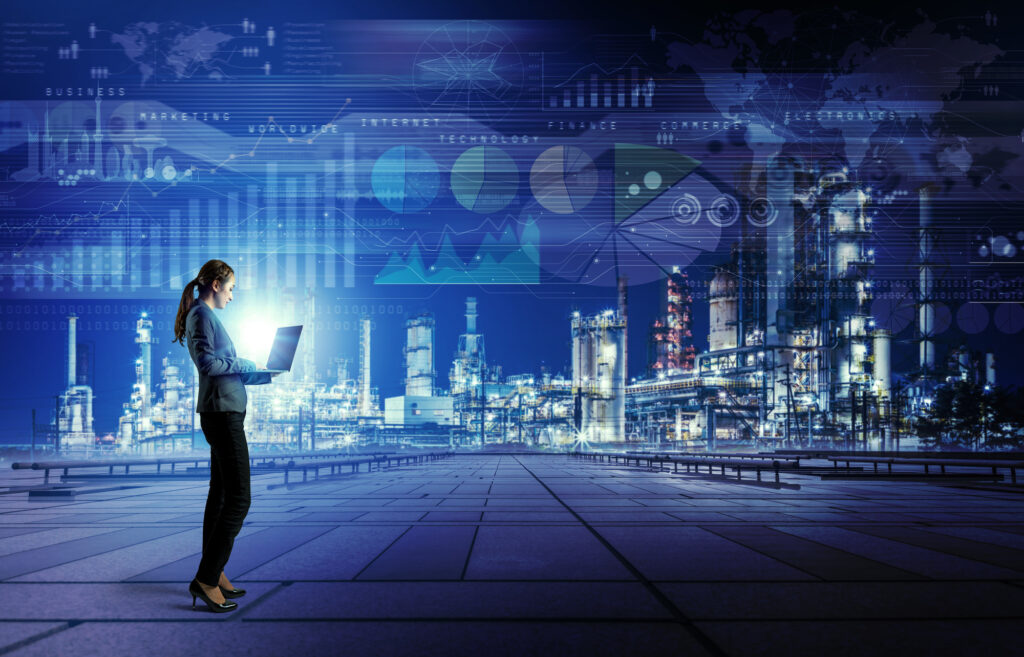
A "smart factory" is a new type of factory that heavily incorporates IoT technology in its operations. It has gained attention in the manufacturing industry in recent years as a solution to various issues experienced in traditional factories. This article introduces the meaning, benefits, and challenges of smart factories.
Table of contents [close]
What is a smart factory? IoT in factories
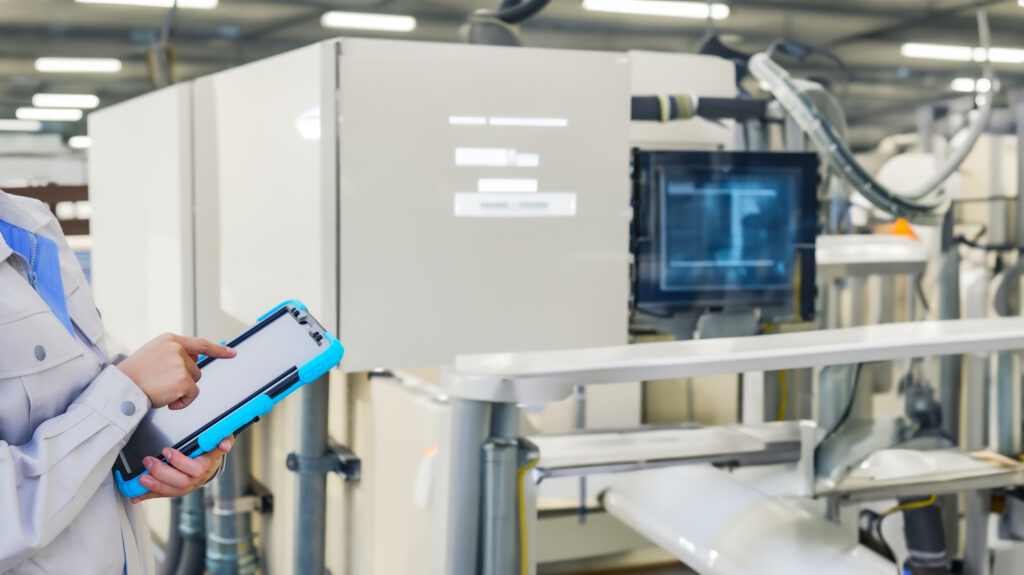
A smart factory enhances productivity by acquiring and analyzing various data through IoT technology. However, this description is probably insufficient to provide a clear image of what IoT, digitalization, and smart factories are. This article provides brief descriptions to offer a clearer understanding of what a smart factory is.
What is IoT?
IoT, or the "Internet of Things," refers to the concept of things being connected to the internet or other networks and able to communicate through them. Traditionally, only devices like computers and smartphones had access to the internet. More recently, many other devices can also be connected to the internet to operate and obtain data.
Familiar examples might include being able to operate your air conditioner when you are not at home or checking your health condition with a smartwatch. Additionally, with the rise of IoT and digitalization, the number of internet-connected devices is increasing, such as refrigerators that provide optimal recipes based on the ingredients inside.
In the industrial sector, technology that connects each device to a network and analyzes the acquired data is becoming more prevalent. This interconnected approach enhances efficiency, enables predictive maintenance, and improves decision-making processes within factories, paving the way for the development of smart factories.
What are smart factories?
A smart factory is one where manufacturing machines, core systems, and management systems are interconnected through a network using IoT technology. This allows for the collection and analysis of detailed data in real time.
In conventional factories, improving the manufacturing process requires workers to manually inspect the site, collect data, and analyze recorded information. In contrast, a smart factory automatically stores data collected through IoT devices on servers, making it readily available for use. This automated data collection allows visualizations of the factory to be made and processes to be monitored more effectively.
Smart factories can accurately obtain data that previously relied on human senses, enabling precise analysis and data-driven decision-making. This capability contributes to sustainable improvements in manufacturing processes, maintaining enhancements in quality and productivity. By leveraging IoT technology, smart factories can achieve higher efficiency, reduced downtime, and improved overall performance.
Advantages of smart factories
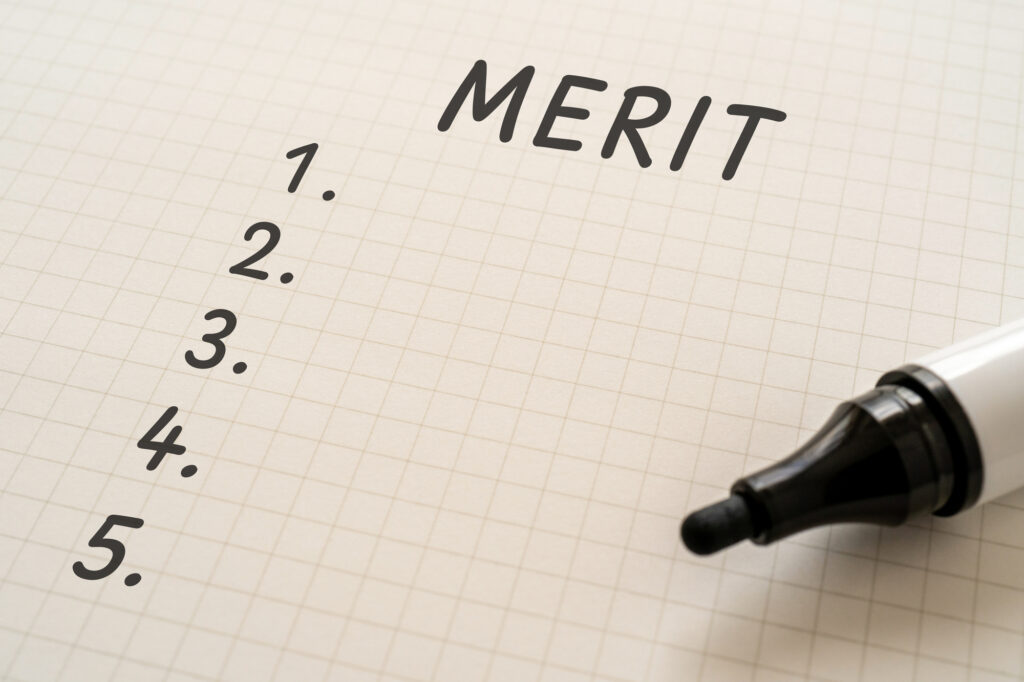
Smart factories are able to collect and analyze data through IoT and digitalization, but what are the specific benefits of this? This section introduces five advantages of smart factories over traditional factories.
Improving quality through visualization
A smart factory is a factory where all of the equipment on the production line is connected to the core system and other systems via a network. By constantly collecting data on each device and the products being manufactured, it becomes possible to accurately monitor factory operations and create accurate visualizations of the factory and its processes.
This connectivity allows for the quick detection of problems such as the sudden occurrence of defective products or inconsistent quality due to equipment failure. Additionally, by accumulating data before and after a problem occurs, it is possible to investigate the cause of defects and improve the processes that cause them, helping to reduce the occurrence of defective products and stabilizing quality.
Moreover, by understanding which tasks are highly productive and which are not, it is possible to identify bottleneck processes and develop improvement measures that will led to increased productivity.
Saving energy and reducing production loss
In a smart factory, the operating status of each device is constantly being monitored and related data is accumulated. This enables the visualization of waste occurring in the factory. This information can be used for cost reductions through energy saving and the reduction of production loss.
By understanding the operating status of all equipment, energy can be saved by stopping equipment with low utilization during certain hours or by leveling out the operating status to avoid peaks. Given the enormous amount of energy used in factories, including electricity, cost reduction through energy saving can have outsized effects on profitability.
In addition, by analyzing the manufacturing capacity and shipping status of each production line, it is possible to optimize inventory, improve yield rates, streamline logistics within the factory, and adjust production volume to meet demand. This can result in a significant reduction of production losses.
Resolving labor shortages
In a smart factory, accurate digitalization of the manufacturing process enables efficient automation through the introduction of AI and robot manufacturing equipment. Even in processes that cannot be fully automated, it may be possible to reduce the number of personnel required by improving work procedures, reviewing work hours, and streamlining personnel deployment.
In Japan, where the birthrate is declining, labor shortages are becoming more serious. Production can stall if enough workers cannot be hired, and higher wages may be needed to attract them. Through the implementation of smart factory technologies, the number of workers required can be reduced, contributing to stable production even in the midst of labor shortages.
Responding effectively to breakdowns and other issues
Since breakdowns in production equipment can halt the production line, preventing them is essential for the stable operation of any factory.
In conventional factories, breakdowns are typically prevented by regularly replacing parts based on a set schedule. However, in a smart factory, the operating status of each piece of production equipment is constantly monitored. This continuous monitoring helps create visualizations of the causes of potential issues, such as the deterioration of parts and the need to replenish consumables, allowing for more efficient maintenance.
Additionally, if an unexpected problem does occur, such as a breakdown or a stoppage of the production line, the issue can be immediately detected and addressed. Since data is constantly collected and accumulated, identifying the cause is straightforward, and measures to prevent recurrence can be effectively and quickly implemented.
Preserving and passing down know-how
In many industries, technical expertise gained over decades of experience is not being passed down to the next generation due to a shortage of younger workers. The loss of these skills and knowledge is a growing concern. Smart factories are addressing this issue by creating comprehensive manuals of manufacturing processes that traditionally relied on the experience and intuition of veteran workers. By leveraging data analysis, smart factories can capture and document these valuable skills.
For instance, cameras and various sensors can record the movements of experienced workers. This data is then analyzed by AI to extract essential techniques and knowledge, which are compiled into detailed manuals.
This digitalization and creation of manuals allow for more efficient training of new employees, including foreign workers and local staff at overseas factories. Overcoming language barriers that previously hindered on-the-job training, smart factories can now provide consistent and effective training, ensuring the transfer of critical skills and expertise. This approach not only preserves valuable know-how but also helps in securing and developing a skilled workforce for the future.
Challenges facing smart factories
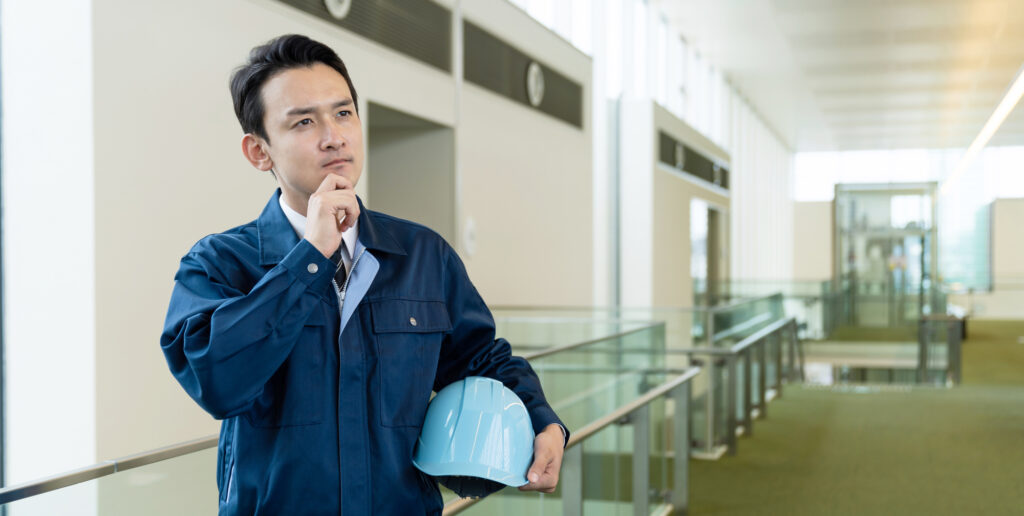
While smart factories offer many benefits and are expected to become the standard in the manufacturing industry, their introduction comes with several challenges. This section introduces some of the key challenges associated with implementing smart factories.
High installation costs
To make equipment IoT-enabled and create a connected factory, it is necessary to update each manufacturing device, install sensors, and set up computers and other equipment required to store and analyze the acquired data. In addition, construction work is required to connect each device and piece of equipment to a network, resulting in significant initial costs.
Furthermore, the equipment in smart factories is highly specialized and is not commonly found in conventional factories. These devices require ongoing maintenance, leading to increased running costs.
When considering the introduction of a smart factory, it is essential to compare the potential cost reduction benefits with the initial and ongoing costs of implementation.
Know-how needed for implementation
In a smart factory, data is constantly collected and stored from each manufacturing facility. This results in the accumulation of a large volume of information. Analyzing this vast amount of data requires specialized skills. Without the expertise to analyze and manage the data, it cannot be used effectively. If a company lacks this know-how, it will need the assistance of external experts such as data scientists. Hiring new staff requires additional labor costs, so careful consideration is necessary.